This article delves into the pivotal role of Variable Frequency Drives (VFDs) in enhancing motor control within automation systems, spotlighting their significance in improving energy efficiency, operational cost reduction, and extending the lifespan of machinery. Focusing on applications across diverse industries such as manufacturing, water treatment, HVAC systems, and renewable energy, particularly within the European context, including Germany and Austria, it underscores the strategic advantages of VFD technology. Through a comprehensive analysis, the piece addresses technical considerations and challenges in VFD implementation, including selection criteria, installation, and maintenance.
Moreover, it explores the future trends in VFD innovation, such as advancements in power electronics, integration with the Internet of Things (IoT), and contributions to sustainable and green automation practices. By providing insights into real-life case studies and offering guidelines on overcoming common issues, this article aims to equip engineering professionals and hiring managers with the knowledge to leverage VFD technology effectively. The inclusion of key applications, benefits, and future directions of VFDs within automation underscores the strategic value they offer to modern industrial operations, making the narrative not only informative but also relevant to potential employers looking to innovate and enhance efficiency in their processes. By Alireza Alidadi, Cademix Institute of Technology
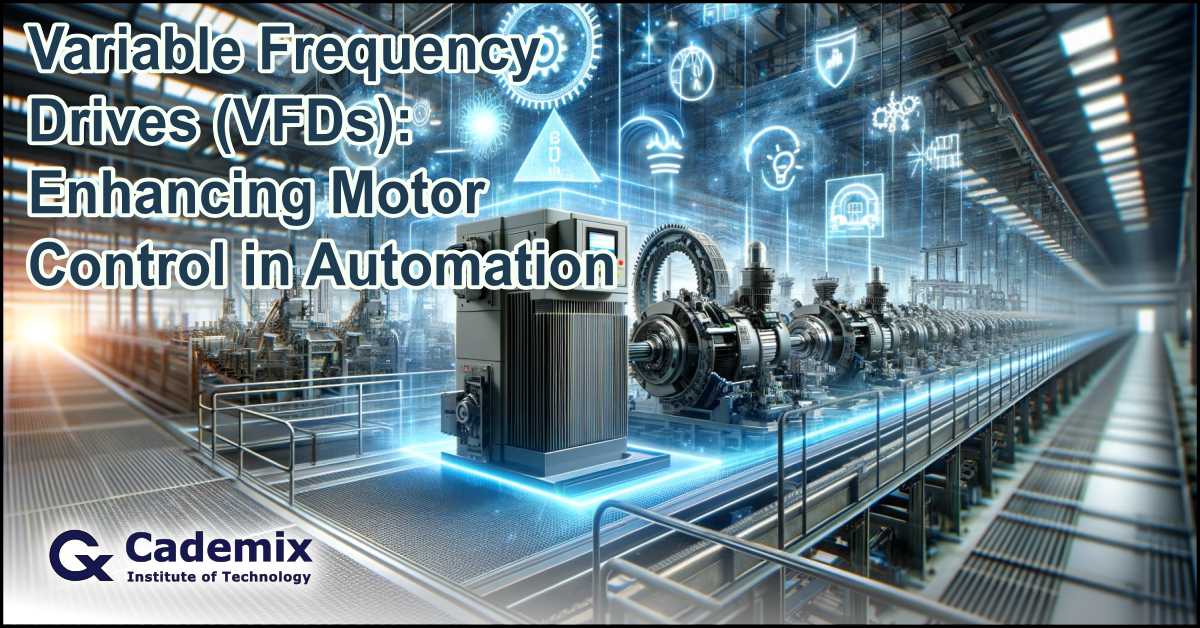
1. Introduction to Variable Frequency Drives (VFDs)
Variable Frequency Drives (VFDs) are crucial tools in industrial automation. They let us control how fast and with how much force electric motors operate. Essentially, VFDs adjust the power to the motor, making it possible to change the motor’s speed to match what’s needed for the job. This means motors can work more efficiently, saving energy and reducing wear and tear.
The development of VFD technology is a story of constant improvement. Starting with basic versions in the early 20th century, VFDs have become much more advanced over the years. Today, they use sophisticated electronics to control motors with great precision. This evolution reflects the ongoing search for better ways to manage motor speed and efficiency in industries.
VFDs are vital for making industrial processes more efficient. By adjusting motor speeds to the exact needs, they help save energy and cut costs. This not only leads to better performance but also makes processes more sustainable. VFDs are used in a wide range of applications, from moving conveyor belts to running pumps and fans, showing just how important they are in modern automation.
The picture number one shows the author at work, where industrial automation equipment is widely used. This image shows the author’s hands-on experience with VFD technology, adding a personal touch to the discussion on how these drives are used in real-world settings.
In short, VFDs are key to improving industrial operations, making them more efficient and adaptable. As industries continue to evolve, the role of VFDs is expected to grow, leading to further advancements in how we use and control energy in automation.
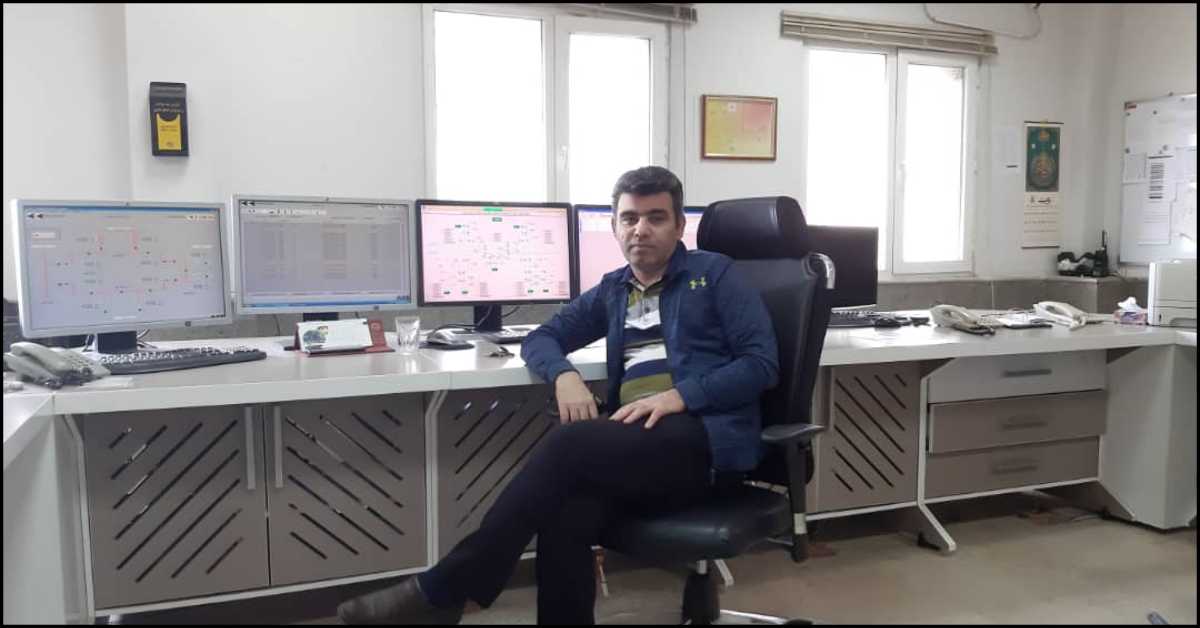
2. Advantages of VFDs in Automation
Variable Frequency Drives (VFDs) bring several key benefits to automation, making processes more efficient and cost-effective. Let’s delve into these advantages:
Energy Efficiency: One of the main benefits of using VFDs is their ability to save energy. By adjusting the speed of motors to match the actual needs of the operation, VFDs ensure that no energy is wasted. This is especially useful in applications where the motor doesn’t need to run at full speed all the time. For example, in a conveyor system, the speed can be reduced when there are fewer items to move, saving a significant amount of energy over time.
Extended Equipment Lifespan: Motors can wear out quickly if they are constantly running at full speed, especially if they don’t need to. VFDs help by ensuring that motors run only at the speed necessary for the task at hand, reducing mechanical stress and wear. This means that the motors and the machinery they power can last much longer, reducing the need for replacements and repairs.
Improved Process Control: VFDs offer precise control over motor speed, torque, and acceleration, making automation processes more reliable and efficient. This precise control is crucial in applications requiring a high degree of accuracy, such as in the mixing of ingredients in food production or the control of airflow in ventilation systems. With VFDs, operators can fine-tune processes, achieving better outcomes and reducing waste.
Cost Savings: The combination of energy savings, reduced wear and tear on equipment, and improved process efficiency leads to significant cost reductions. Lower energy consumption means lower utility bills, while extended equipment lifespan reduces maintenance and replacement costs. Additionally, improved process control can reduce waste, further cutting down costs.
Case Study: Siemens AG, a global powerhouse in electronics and electrical engineering, operating in the industry, energy, and healthcare sectors, provides a notable example of VFD implementation in their manufacturing facility in Munich, Germany. The company faced challenges with the energy consumption of their extensive HVAC system, crucial for maintaining precise conditions in both production areas and offices. To address this, Siemens AG integrated VFDs into their HVAC system, enabling dynamic control of fan and pump speeds according to real-time demand rather than running them at full capacity continuously.
This strategic move led to a remarkable 25% reduction in energy usage for their HVAC operations, translating into significant annual savings on energy costs. Beyond financial benefits, this initiative underscored Siemens AG’s commitment to environmental sustainability and operational efficiency, showcasing the practical and economic advantages of leveraging VFD technology in industrial settings.
In summary, VFDs are transformative in automation, offering energy efficiency, extending equipment lifespan, improving process control, and generating cost savings. The case study from Germany illustrates how these benefits play out in real-world applications, showcasing the potential of VFDs to revolutionize industrial operations.
3. Key Applications of VFDs in Various Industries
Variable Frequency Drives (VFDs) are versatile tools that have found applications across a wide range of industries. Their ability to precisely control motor speed and torque makes them invaluable in many sectors.
Manufacturing Sector: In the manufacturing world, VFDs are crucial for automation processes. They help in controlling the speed of conveyor belts, ensuring that products move through the production line at the right pace. For example, in automotive assembly lines, VFDs adjust the conveyor speed to match the assembly requirements, improving efficiency and reducing the risk of errors. This precise control leads to smoother operations and better product quality.
Water and Wastewater Treatment: VFDs play a significant role in water and wastewater treatment facilities. They are used to control the speed of pumps, allowing for efficient management of water flow and pressure. This is critical in processes such as water filtration, where the flow rate needs to be carefully controlled to ensure effective cleaning while conserving energy. By using VFDs, these facilities can reduce energy consumption and operational costs, contributing to more sustainable practices.
HVAC Systems: Heating, Ventilation, and Air Conditioning (HVAC) systems also benefit greatly from the use of VFDs. In a modern building in Europe, for instance, VFDs are used to control the speed of fans and pumps in the HVAC system, adapting to the building’s heating and cooling needs in real-time. This adaptability not only makes the system more energy-efficient but also enhances the comfort of occupants. Such implementations can lead to significant energy savings, particularly in large commercial buildings where HVAC systems are a major energy consumer.
Renewable Energy: The renewable energy sector, including wind turbines and hydroelectric power plants, utilizes VFDs to maximize energy production efficiency. In wind turbines, VFDs adjust the blade rotation speed to match wind speeds, optimizing energy capture. In hydroelectric plants, they control the flow of water through turbines, ensuring that power generation is maximized without wasting water resources. This precise control is essential for increasing the efficiency and reliability of renewable energy sources.
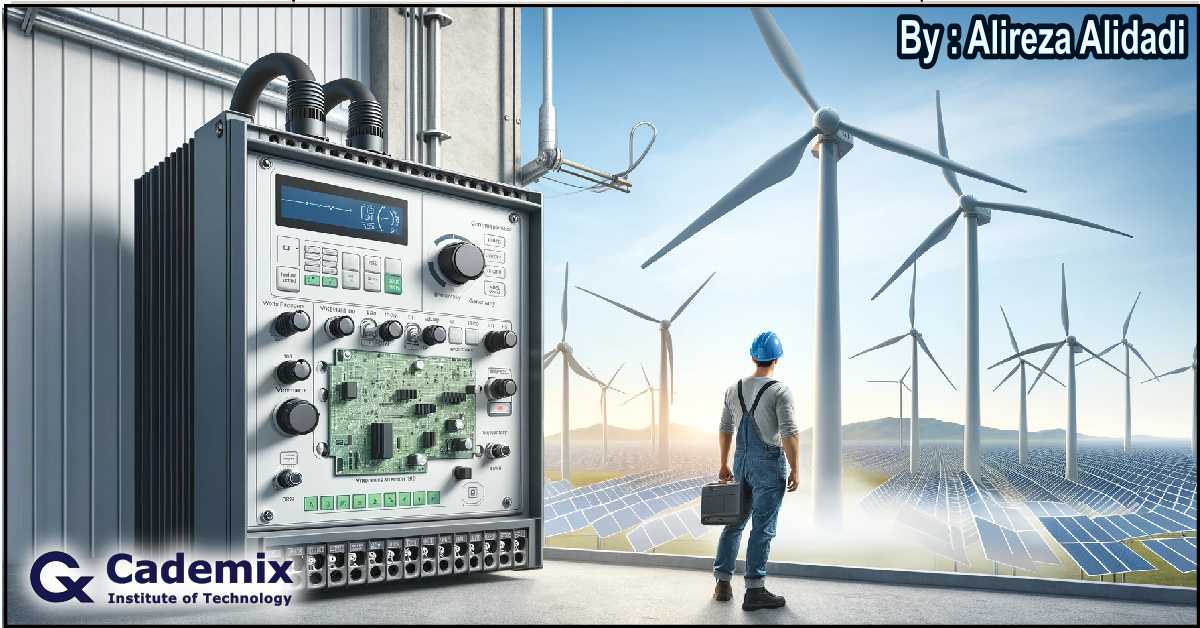
In conclusion, VFDs are key components in a variety of industries, improving efficiency, reducing energy consumption, and enhancing operational control. From manufacturing and water treatment to HVAC systems and renewable energy, the applications of VFDs demonstrate their versatility and critical role in modern industrial processes. Their widespread use across these sectors underscores the importance of VFD technology in achieving more sustainable and efficient operations.
4. Technical Considerations and Challenges
Implementing Variable Frequency Drives (VFDs) in industrial applications comes with several technical considerations and challenges. Understanding these aspects is crucial for ensuring the efficient and reliable operation of VFDs.
Selection Criteria: Choosing the right VFD is critical for the success of any application. When selecting a VFD, consider the power and speed range required by the motor it will control. The VFD must be able to handle the maximum power needs of the motor. Speed range is also important, as the VFD should offer the flexibility needed for the application’s varying speed requirements. Environmental factors, such as temperature, humidity, and the presence of dust or corrosive substances, must also be taken into account to ensure the VFD can operate reliably under the specific conditions of the installation site.
Installation and Integration: Proper installation and integration of VFDs into existing systems are key to maximizing their benefits. It’s important to follow the manufacturer’s guidelines for installation to avoid common pitfalls. Ensure that the VFD is compatible with the electrical system and that all connections are secure. Integration involves configuring the VFD to communicate effectively with the existing automation system. This might require programming the VFD for specific functions or ensuring it can communicate with other system components via industrial communication protocols.
Maintenance and Troubleshooting: Regular maintenance is essential for the long-term reliability of VFDs. This includes routine inspections, cleaning, and checking connections for signs of wear or damage. Keeping a log of any errors or issues can help in diagnosing problems that may arise. Common issues with VFDs include overheating, which can be mitigated by ensuring adequate ventilation, and issues with the power supply, such as voltage fluctuations. Understanding these common problems and how to troubleshoot them can save time and reduce downtime.
Addressing Electromagnetic Interference (EMI): VFDs can generate electromagnetic interference, which can disrupt the operation of nearby electronic equipment. To minimize EMI issues, it’s important to install proper filtering and shielding. Using shielded cables for all wiring associated with the VFD and grounding the system correctly can significantly reduce EMI. Additionally, installing filters or choosing VFDs with built-in EMI suppression features can help ensure that the VFD does not interfere with the operation of other equipment in the environment.
By considering these technical aspects and addressing the challenges head-on, users can ensure that their VFD installations are efficient, reliable, and free from common issues. Understanding the selection criteria, installation requirements, maintenance needs, and ways to mitigate EMI will lead to smoother operation and longer service life for VFDs in various industrial applications.
Consideration/Challenge | Description |
Selection Criteria | Consider the motor’s power and speed requirements. Account for environmental factors such as temperature, humidity, and dust. |
Installation and Integration | Follow the manufacturer’s guidelines for installation. Ensure compatibility with electrical systems and integrate with existing automation systems appropriately. |
Maintenance and Troubleshooting | Conduct routine inspections and cleanings. Be vigilant for overheating and voltage fluctuations. Maintain a log for easier diagnosis of issues. |
Addressing EMI | Utilize shielded cables and ensure proper system grounding. Install EMI filters or opt for VFDs with built-in suppression features to minimize interference. |
5. Future Trends and Innovations in VFD Technology
The landscape of Variable Frequency Drive (VFD) technology is witnessing rapid advancements, promising a future where efficiency, intelligence, and sustainability are at the forefront of industrial automation. These innovations are set to redefine how VFDs contribute to automation systems across various sectors.
Advancements in Power Electronics: The heart of VFD technology lies in its power electronics, where recent breakthroughs in semiconductor technologies have been transformative. Silicon Carbide (SiC) and Gallium Nitride (GaN) semiconductors are leading this revolution, offering superior efficiency and performance over traditional silicon-based components. These materials can operate at higher temperatures, voltages, and frequencies, significantly enhancing VFD efficiency and reducing their size. The result is more compact, energy-efficient drives that can be integrated into a wider range of applications, from heavy industrial equipment to portable devices.
Smart VFDs and IoT Integration: The integration of VFDs with the Internet of Things (IoT) marks a significant leap towards intelligent automation systems. Smart VFDs, equipped with IoT capabilities, enable real-time monitoring and control of motors from anywhere in the world. This connectivity allows for predictive maintenance, where potential issues can be identified and addressed before they lead to downtime. Moreover, data collected from smart VFDs can be analyzed to optimize operational efficiency, reducing energy consumption and improving system performance. The ability to remotely adjust VFD settings in response to changing operational conditions also enhances the adaptability of automation systems to meet dynamic demands.
Sustainability and Green Automation: In an era where sustainability is a global priority, VFDs are playing a pivotal role in promoting green automation practices. By optimizing motor speed and reducing energy consumption, VFDs significantly lower the carbon footprint of industrial operations. Furthermore, the development of VFDs using eco-friendly materials and processes is on the rise, aligning with broader environmental goals. The push towards renewable energy sources also sees VFDs at the forefront, where their precise control capabilities are crucial for maximizing the efficiency of wind, solar, and hydroelectric power systems. This focus on sustainability not only benefits the environment but also offers economic advantages through reduced energy costs and compliance with regulatory standards.
The future of VFD technology is marked by these trends towards more efficient, intelligent, and sustainable industrial practices. As advancements in power electronics continue to evolve, and as the integration of VFDs with IoT and green automation practices deepen, the potential for innovation in this field is boundless. These developments promise to enhance the capabilities of automation systems, making them more adaptive, efficient, and environmentally friendly.
6. Conclusion: The Strategic Value of VFDs in Automation
Variable Frequency Drives (VFDs) are key to modern industrial automation. They help control motors in a way that saves energy, improves processes, and cuts costs. This article has covered how VFDs work, their benefits, where they are used, and the new trends that are making them even better.
VFDs are important for many reasons. They make machines run more efficiently and last longer. They are used in many fields, like manufacturing, water treatment, and energy. The future looks bright for VFDs with new technologies making them smarter and more connected. This means they can do their job even better, helping to save more energy and support the environment.
Call to Action for Employers: It’s important for companies to use VFDs in their projects. They offer many benefits, such as saving money and being better for the environment. As VFDs keep getting better, having experts who know how to use them will be very valuable. Hiring these experts can help your company stay ahead and be more successful.
In short, VFDs are very important for today’s industries. They offer a lot of benefits and are getting even more useful with new improvements. Companies that use VFDs and have experts who know about them will do well in the future.
Additional Resources
Industry Reports and Technical Guides
- IEEE Xplore Digital Library: Offers a range of papers and articles on VFD technology advancements and applications. Visit: IEEE Xplore
- The Association of Electrical and Mechanical Trades (AEMT): Provides guides on the maintenance and repair of electrical motors, including those used with VFDs. Check their resources at AEMT
- International Energy Agency (IEA) Reports: Offers insights into energy efficiency and the role of industrial automation technologies like VFDs in reducing energy consumption. Access reports at IEA
- Automation.com: A comprehensive resource for the latest articles, case studies, and white papers on automation technology, including VFDs. Explore: Automation.com
Leading VFD Manufacturers
- Siemens: A global powerhouse in electrical engineering and electronics, offering a wide range of VFD solutions. Learn more at Siemens Drive Technologies
- ABB: Known for their extensive range of drives and offering detailed technical resources on how to select and implement them. Visit: ABB Drives
- Schneider Electric: Offers innovative and energy-efficient VFDs suitable for a wide variety of applications. Discover more at Schneider Electric Variable Speed Drives
- Rockwell Automation: Provides a comprehensive range of VFDs under the Allen-Bradley brand, known for their quality and reliability. Check out: Rockwell Automation PowerFlex Drives
- Danfoss: Specializes in energy-efficient solutions, including VFDs for various industrial applications. Learn more at Danfoss Drives
These resources are a great starting point for anyone looking to deepen their understanding of VFD technology, its benefits, and its critical role in modern automation and energy efficiency initiatives. Whether you’re a student, a professional in the field, or simply curious about the latest technological advancements, these resources offer valuable insights and practical knowledge.
About the Author
Alireza Alidadi is a distinguished electrical power engineer with extensive experience in the energy sector, currently enriching his skills through the Cademix Acceleration Program. His career is highlighted by his tenure as a dispatching unit shift supervisor at Fajr Petrochemical Company. In this role, Alireza excelled in managing gas turbines, supervising high voltage power stations, and enhancing electrical safety protocols, significantly improving operational efficiency and safety within the energy industry.
He holds a Master of Science in Electrical Power Engineering from Khozestan University of Science and Technology and a Bachelor of Science in the same field from Azad University of Dezful. These academic qualifications have provided him with a robust understanding of electrical engineering, allowing him to address and solve intricate challenges in his field effectively.
Alireza is fluent in Persian and English and has a proficient understanding of German, enabling him to engage and collaborate effectively with a wide array of colleagues and partners across the global engineering landscape. His language skills also bolster his ability to participate in and contribute to international projects and research endeavors.
Committed to the advancement of electrical engineering and dedicated to promoting safety and efficiency, Alireza embodies a professional ethos focused on continuous improvement and innovation. His involvement in the Cademix Acceleration Program underscores his commitment to exploring new engineering frontiers, aiming to make significant contributions to the field. Alireza’s deep expertise and insights, especially in industrial automation and electrical engineering, make him an invaluable resource for potential employers and collaborators looking to address the challenges of contemporary manufacturing and energy production.