Programmable Logic Controllers (PLCs) are central to the design and operation of modern industrial automation systems, enabling precise control over complex processes. This article provides a comprehensive guide to the design, programming, and commissioning of control software using PLC systems, highlighting key programming languages such as Ladder Logic, Function Block Diagram, and Structured Text. It addresses the development and implementation of control algorithms that optimize industrial processes and enhance system efficiency. The integration of automation systems into existing production environments is examined, focusing on communication protocols and strategies to minimize downtime. Additionally, the article covers troubleshooting techniques for PLC programs and methods for optimizing control software to ensure reliability.
The commissioning process is detailed, including testing, calibration, and verification procedures critical to achieving operational excellence. The article also explores emerging trends in industrial automation, such as Industry 4.0 and IoT integration, emphasizing the importance of continuous professional development for engineers in the field. This work serves as a practical resource for engineers seeking to expand their expertise in PLC programming and industrial control systems. By Alireza Alidadi, Cademix Institute of Technology
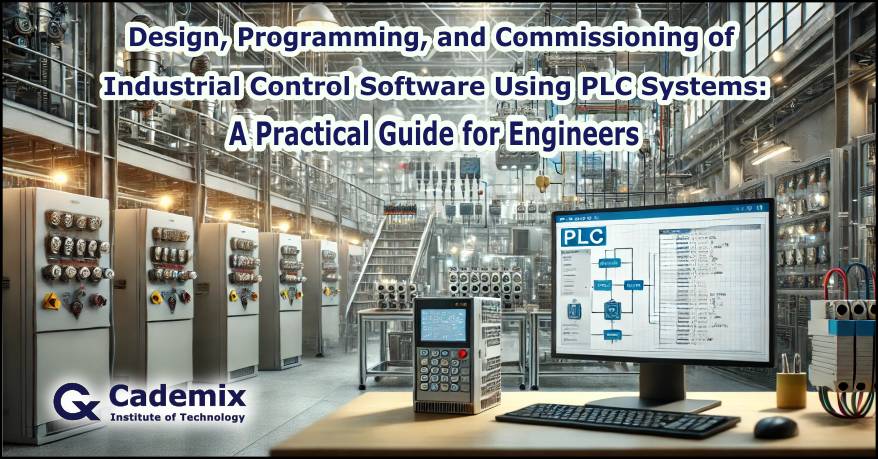
1. Introduction
In today’s industrial landscape, Programmable Logic Controllers (PLCs) are essential in automating production processes, increasing efficiency, and ensuring precision across various industries. As the backbone of industrial automation, PLC systems enable the control of machinery, processes, and complex workflows, transforming traditional manufacturing environments into interconnected and highly optimized systems.
A PLC is a specialized computer designed to operate in demanding environments, capable of processing real-time data and executing control actions based on predefined logic. Unlike traditional computers, PLCs are built to handle harsh conditions, operate continuously, and maintain stability and reliability in critical applications. Key industries—from automotive to pharmaceuticals, food production, and energy—rely on PLCs to maintain productivity and safety.
The foundation of PLC-based automation lies in effective control software design and programming. To meet the demands of modern industrial processes, engineers must master a variety of PLC programming languages, each with unique advantages suited to different tasks. The most widely used languages, defined by the IEC 61131-3 standard, include Ladder Logic, Function Block Diagram, and Structured Text. Proficiency in these languages allows engineers to create custom solutions, optimizing equipment and systems for both efficiency and reliability.
This article aims to provide a detailed overview of the PLC programming process, from design to commissioning, with an emphasis on implementing control algorithms, integrating systems into existing production environments, troubleshooting, and optimizing performance. Additionally, the article examines key advancements, such as the role of Industry 4.0 and the Internet of Things (IoT), which further drive automation’s potential in creating agile, interconnected, and responsive systems. For engineers in automation, continuous learning is critical to keeping pace with these innovations, as they redefine the future of industrial control systems.
2. Designing Control Software Using PLCs
Designing control software for PLC systems is a structured process that requires a detailed understanding of the industrial environment and specific operational goals. Engineers begin with defining the application’s requirements, such as optimizing energy use, minimizing machine downtime, or enhancing process accuracy. A clear outline of these objectives forms the basis of the software’s design, ensuring that the final program aligns with the broader goals of the facility.
The process starts by selecting an appropriate PLC programming language from the IEC 61131-3 standard. This standard includes five primary languages: Ladder Logic (LD), Function Block Diagram (FBD), Structured Text (ST), Instruction List (IL), and Sequential Function Chart (SFC). Each language offers unique strengths, making it important to choose one that fits the application’s complexity and requirements.
- Ladder Logic (LD) is the most common language, designed with a structure similar to electrical relay logic. Its visual, ladder-like structure makes it accessible for applications that involve sequential processes or relay-based systems. Due to its readability, Ladder Logic is often used in applications requiring real-time troubleshooting and fast fault identification.
- Function Block Diagram (FBD) is a graphical language based on the flow of function blocks that represent control logic. FBD is ideal for systems that rely heavily on modular design, as engineers can easily adjust each function block independently. It is often used in applications needing high modularity and scalability.
- Structured Text (ST) is a high-level language that resembles programming languages like Pascal or C. This text-based language is efficient for complex calculations and data handling, making it suitable for advanced automation processes with intricate mathematical operations or logic flows.
- Instruction List (IL) is a low-level language similar to assembly code. Though it offers precise control, IL is less commonly used today due to its complexity and the increased popularity of more visual languages.
- Sequential Function Chart (SFC) provides a flowchart-based structure for defining sequences of operations, often used for multi-step processes requiring a clear order of execution. It is particularly useful in applications where processes follow distinct stages.
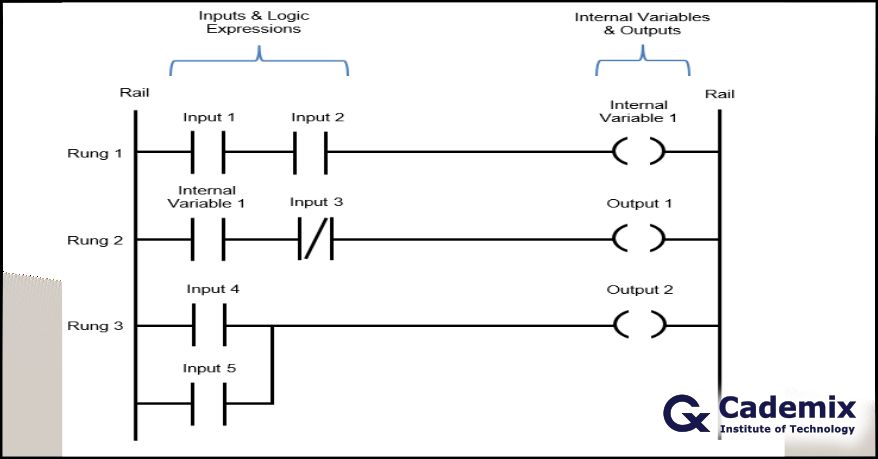
Once the programming language is selected, engineers move on to defining the Input-Output (I/O) mapping, which assigns specific inputs and outputs to sensors, actuators, and other devices that interact with the PLC. Proper I/O mapping enables the PLC to receive real-time data, process it based on the defined logic, and send the necessary commands to execute actions on the connected machinery. This mapping is especially critical in large, complex systems where PLCs may interact with hundreds of devices simultaneously.
The next step is to define communication protocols, such as Modbus, Ethernet/IP, or Profibus, which enable the PLC to interface with other control systems, sensors, Human-Machine Interfaces (HMIs), and Supervisory Control and Data Acquisition (SCADA) systems. Selecting the correct protocol ensures seamless data flow between the PLC and other devices, improving the speed and accuracy of data exchanges. Integrating a standardized protocol also enhances the scalability of the control system, making it easier to add new components without major reconfigurations.
After defining the I/O structure and communication protocols, engineers create the logical flow of the software. This includes setting up control sequences, safety interlocks, alarms, and fault-handling logic to prevent equipment damage or hazardous conditions. Safety interlocks are particularly critical in applications where malfunctions pose a risk to personnel or equipment. In these cases, software-based safety mechanisms act as a first line of defense, shutting down equipment if certain thresholds are breached.
Modular programming is a best practice that improves both the design and future maintenance of PLC software. By breaking down the program into smaller, manageable modules, each handling a specific function (such as motor control, sensor processing, or alarm handling), engineers create a structured framework that is easier to update, test, and troubleshoot. This modular approach also allows sections of the code to be reused or repurposed in future projects, saving time and reducing the potential for errors.
Finally, testing and simulation play a crucial role in the design process. Engineers use simulation tools to emulate real-world scenarios, ensuring the logic performs as expected before deployment. Through simulation, they can verify that each module functions correctly, that all I/O mappings respond as intended, and that the overall program meets safety and performance requirements. By thoroughly testing each component, engineers minimize the risk of failures or unexpected behaviors during commissioning and operation.
Designing control software for PLCs is a meticulous and iterative process that requires balancing performance, reliability, and safety. Each design decision, from language selection to modular programming and protocol configuration, contributes to building a system that is not only robust but also adaptable to future technological advancements. In an era of rapid industrial change, well-designed PLC control software enables facilities to operate efficiently while staying agile in the face of evolving demands.
Programming Language | Description | Best Use Cases | Advantages | Disadvantages |
---|---|---|---|---|
Ladder Logic (LD) | Resembles electrical relay logic; uses ladder-like structure with contacts and coils. | Sequential control, motor control, relays | Easy to learn; highly visual; widely used | Limited for complex algorithms or calculations |
Function Block Diagram (FBD | Block-based, graphical language where functions and variables are represented as blocks and wires. | Modular, reusable logic; process control | Easy to visualize; supports modular design | Can be less readable with complex systems |
Structured Text (ST) | High-level, text-based language similar to Pascal or C. | Complex calculations, data processing | Suitable for complex logic; powerful syntax | Less visual, harder to troubleshoot in real-time |
Instruction List (IL) | Low-level, text-based language with assembly-like instructions. | Simple control tasks, small programs | Very precise control; highly efficient code | Steep learning curve; less commonly used today |
Sequential Function Chart (SFC) | Flowchart-style representation for multi-step sequences; structured as steps and transitions. | Batch processes, multi-step workflows | Easy to manage sequential processes | Can become complex with numerous steps and transitions |
3. Programming PLC Systems
Programming PLCs involves developing precise control logic to achieve specific industrial automation tasks, from simple motor control to complex system management. The programming process starts with a clear understanding of the system requirements and goals, as well as any constraints related to the machinery or processes being automated. In industrial environments, PLC programming needs to be both reliable and maintainable, making it essential to write clear, efficient, and adaptable code.
Selecting the Right Programming Language
Choosing a suitable programming language from the IEC 61131-3 standard is a foundational step. Each language offers unique benefits, making it ideal for certain types of control tasks:
- Ladder Logic (LD) is visually similar to electrical relay diagrams, making it intuitive for technicians with electrical backgrounds. It is excellent for systems with sequential or repetitive tasks, such as conveyor belt operations or lighting control. Ladder Logic’s visual layout simplifies troubleshooting, as it is easy to follow each step in the sequence.
- Function Block Diagram (FBD) is ideal for modular designs where blocks can represent distinct control functions. This block-based approach is highly effective in process automation, where complex functions can be pre-built and linked for quick implementation. Engineers benefit from FBD’s modularity, which simplifies updates or changes.
- Structured Text (ST), a high-level language resembling traditional programming languages, is best suited for complex calculations or data handling tasks, such as temperature control algorithms or data analysis functions. Although it is less visual, ST is powerful for advanced applications and enables the creation of reusable code blocks.
- Instruction List (IL) is a low-level, assembly-like language offering precise control over commands. While less common today, it can be beneficial for simple, small programs due to its efficiency in resource-constrained environments. However, the language’s complexity often makes it less desirable for larger, intricate systems.
- Sequential Function Chart (SFC) uses a flowchart structure, making it ideal for applications requiring multi-step processes. Each stage or “step” is visually laid out, with transitions defining the movement from one step to the next. SFC is especially useful for batch processes, where a system must go through a series of distinct stages.
Setting Up I/O and Mapping
Once the programming language is chosen, the next step is setting up input/output (I/O) mapping. This involves assigning each input (such as sensors, switches, or buttons) and output (such as motors, valves, or alarms) a unique identifier in the program. I/O mapping allows the PLC to interpret signals from various devices, process the data according to programmed logic, and respond by activating or deactivating devices as needed. Proper I/O setup is critical for ensuring that signals are accurately interpreted and processed, maintaining system stability and control precision.
Programming Control Logic
Creating control logic requires defining conditions, actions, and sequences to manage system behaviors. Control logic includes setting up basic operations, such as activating a motor when a button is pressed, and complex functions, like controlling temperature by adjusting a heating element based on real-time sensor data. This logic can involve:
- Conditions and Timers: Conditions are fundamental to PLC programming, defining when actions should occur. For example, if a temperature sensor reads above a threshold, a cooling fan might activate. Timers are used to add delays or control the duration of specific actions, helping to manage process timing.
- Counters and Comparators: Counters track the number of occurrences of specific events, while comparators compare values to make decisions. These functions are crucial for managing production processes, such as counting items on a conveyor belt or triggering an alarm if a parameter exceeds safe levels.
- Error Handling and Safety Interlocks: Error handling ensures that the system can respond safely to faults, protecting both the equipment and operators. Safety interlocks prevent potentially hazardous conditions by enforcing specific checks before operations continue, such as requiring certain safety doors to be closed before machinery can operate.
Modular Programming
Modular programming involves dividing the code into distinct sections or modules, each responsible for a specific function. For example, separate modules could handle motor control, data processing, or alarm handling. This approach simplifies the programming process and makes the program more manageable for future updates or troubleshooting. Modular programming also allows for the reuse of code blocks, saving time when implementing similar functions in multiple programs or projects.
Testing and Verification
Before implementing the program, thorough testing is essential to ensure reliable operation. Engineers use simulation software to test how the PLC logic responds to various inputs and scenarios. Simulation allows for detecting and correcting errors without risking damage to equipment. By verifying each module and the entire program, engineers ensure that the logic performs as expected under all possible conditions.
Documenting the Program
Clear documentation of the PLC program is crucial for maintenance, troubleshooting, and future upgrades. Documentation includes describing each module’s function, explaining key variables, and outlining any specific requirements. Effective documentation enables other engineers and technicians to understand the program’s structure and operation, making future updates and repairs more efficient.
Programming PLC systems requires a combination of technical expertise, practical problem-solving skills, and a structured approach to code organization. Through careful selection of language, attention to I/O mapping, and rigorous testing, engineers can develop PLC programs that optimize industrial processes, enhance safety, and support long-term maintainability.
4. Development and Implementation of Control Algorithms
Developing effective control algorithms is essential for achieving optimal performance in automated industrial systems. A control algorithm is a set of instructions programmed into a PLC to process input data and produce desired outputs, enabling precise control over various machinery and processes. These algorithms can range from simple, like starting or stopping a motor, to highly complex, such as maintaining the balance of multiple variables in chemical processes. This section explores key considerations in developing control algorithms, from designing the logic flow to implementing and refining it in a live production environment.
Understanding the Process Requirements
The development of a control algorithm begins with understanding the process requirements and objectives. Engineers analyze the specific needs of the application, whether it’s maintaining a constant temperature, controlling fluid flow, or coordinating a series of sequential actions. Identifying measurable inputs (such as temperature, pressure, or speed) and desired outputs (such as valve positions, motor speeds, or alarms) guides the design of the algorithm’s logic.
For instance, in a temperature control application, an input sensor continuously monitors temperature, and the algorithm adjusts a heating or cooling element to maintain a target range. If temperature rises above a set threshold, the PLC triggers a cooling fan or reduces heat to restore the desired level. This straightforward principle forms the foundation of many automated processes, where the system makes real-time adjustments based on live data.
Types of Control Algorithms
Control algorithms are generally categorized into three main types:
- Open-Loop Control: In open-loop control, actions are performed without feedback from the system. For example, a conveyor belt system that moves for a fixed duration regardless of load variations is an open-loop system. Open-loop control is simple and cost-effective but may lack precision in applications where feedback is necessary.
- Closed-Loop Control: Closed-loop control relies on feedback to adjust system behavior based on real-time conditions. For example, in a heating system, temperature readings continuously feed back to the PLC, which adjusts heating output to maintain a constant temperature. This control method offers greater accuracy and is commonly used in applications where precise regulation is critical.
- PID Control: Proportional-Integral-Derivative (PID) control is a widely used closed-loop algorithm that continuously calculates errors between a desired setpoint and a measured process variable, applying corrections to reduce the error. PID controllers are highly effective for complex systems requiring precise control, such as maintaining pressure in a hydraulic system or adjusting the speed of a motor based on load changes.
Designing the Algorithm Logic
Once the control type is selected, engineers proceed to design the algorithm logic. This logic defines the steps and conditions that the PLC follows to achieve the desired outputs. Key elements in algorithm design include:
- Comparators and Conditions: Comparators (e.g., greater than, less than) define conditions under which actions are triggered. For instance, if temperature exceeds a threshold, the system activates cooling.
- Timers and Delays: Timers are useful for adding delays in control sequences, managing process timing, and preventing components from activating too quickly. For example, a delay could ensure that a pump only starts after a valve has fully opened, preventing backpressure.
- Counters: Counters track occurrences of events, such as the number of parts produced or cycles completed. Counters can trigger actions once a target count is reached, like sending a notification to refill material when a preset quantity is produced.
Simulation and Testing of Algorithms
Before deploying a control algorithm in a live environment, it undergoes rigorous testing and simulation. Simulation software emulates real-world conditions, allowing engineers to validate the algorithm’s logic, verify outputs, and identify potential issues. For example, a PID control algorithm can be tested in a simulated environment to ensure it maintains stable operation under varying loads and disturbances. Through simulation, engineers adjust parameters and refine logic without risking equipment damage or production losses.
Testing also includes fine-tuning setpoints and thresholds to achieve desired performance. In a motor speed control system, for example, the ideal PID values (proportional, integral, and derivative gains) are calibrated to achieve smooth acceleration and deceleration without overshooting. Testing ensures that the algorithm responds accurately to inputs and maintains stability under different operational conditions.
Implementation and Calibration
Following successful simulation and testing, the algorithm is implemented in the PLC, and live calibration is performed. Calibration adjusts parameters to account for real-world conditions that may differ slightly from simulations. For instance, environmental factors like temperature, humidity, and load variations may influence system behavior, requiring minor adjustments to maintain optimal performance.
During implementation, the system is carefully monitored, and adjustments are made as needed. Engineers observe the system’s response to inputs, fine-tuning the algorithm to ensure it performs reliably and meets performance criteria. Calibration also includes setting up safety interlocks and fault-handling mechanisms to protect equipment and operators in case of unexpected events.
Documentation and Maintenance of Control Algorithms
Comprehensive documentation is essential for the maintenance and future updating of control algorithms. Documentation details the algorithm’s logic, parameter values, and purpose, providing a reference for engineers and technicians who may need to troubleshoot or adjust the system. Documentation typically includes:
- Descriptions of Control Sequences: A step-by-step description of how the algorithm controls the process.
- Parameter Settings: List of critical parameters (e.g., setpoints, PID gains) and their current values.
- Input/Output Mapping: Details on I/O assignments used in the algorithm.
Proper documentation simplifies future modifications, allowing engineers to efficiently update the system as requirements evolve or new technologies are integrated.
Optimizing Algorithms for Efficiency
Continuous improvement is a core principle in industrial automation, and control algorithms are regularly reviewed for optimization opportunities. Engineers analyze system performance data to identify inefficiencies, such as energy overuse, excessive wear on components, or slow response times. Optimization may involve adjusting algorithm parameters, incorporating predictive maintenance elements, or upgrading the PLC’s hardware. In high-demand systems, optimized algorithms can significantly reduce operational costs, improve productivity, and extend equipment lifespan.
The development and implementation of control algorithms are essential in transforming raw process inputs into precise, efficient automation. From understanding process requirements to selecting appropriate control methods, designing and testing the algorithm, and optimizing it for ongoing performance, each step contributes to a system’s overall effectiveness. Well-developed control algorithms enable automated systems to operate with accuracy, stability, and adaptability, supporting the continuous growth and efficiency of industrial automation applications.
5. Integration of Automation Systems into Existing Production Environments
Integrating new PLC-based automation systems into existing production environments is a complex yet essential task in industrial automation. Successful integration allows plants to upgrade processes, increase efficiency, and adapt to evolving production needs without extensive downtime or system overhauls. This section covers key stages of the integration process, including planning, compatibility assessment, communication protocols, testing, and optimization, each of which is critical for ensuring a seamless transition to an automated, high-performance production environment.
Planning and Assessing System Compatibility
Effective integration starts with detailed planning. Engineers first assess the existing production environment, identifying potential challenges related to compatibility, scalability, and specific operational requirements. They evaluate existing equipment, control systems, and network infrastructure to understand how the new automation system will fit into the current setup. This step is crucial to avoid conflicts that could disrupt production or create safety risks.
Compatibility assessment focuses on identifying whether the new PLC system can communicate with existing devices, sensors, and machinery. For example, many legacy systems operate on older communication protocols, such as RS-232 or Modbus, which may not be directly compatible with modern Ethernet-based PLCs. In such cases, engineers may need to implement protocol converters or additional interface modules to bridge compatibility gaps.
Establishing Communication Protocols
Communication between devices is foundational for successful integration, allowing the PLC system to collect data from sensors and provide commands to machinery. Communication protocols are the “language” through which devices share information, and selecting the right protocol is essential for smooth operation.
Several common industrial communication protocols are widely used:
- Modbus is a simple, open protocol often used in legacy systems, allowing data exchange between PLCs and a variety of devices.
- Ethernet/IP is a more modern protocol suitable for high-speed data exchange in larger, complex automation systems. It enables seamless integration of PLCs with higher-level control systems like SCADA (Supervisory Control and Data Acquisition).
- Profibus is a fieldbus protocol widely used in European automation systems, known for its robustness and reliability in harsh industrial conditions.
- Profinet is a newer protocol based on Ethernet, providing faster speeds and more flexible integration than Profibus. It’s ideal for real-time control and connecting various types of devices.
After selecting the protocol, engineers configure the network layout, which includes determining IP addresses, assigning communication channels, and establishing data exchange priorities. Proper network design helps prevent data collisions, bottlenecks, and communication delays that could impair system performance.
Setting Up Data Acquisition and Monitoring
Data acquisition involves collecting real-time information from sensors, machines, and other connected devices within the production environment. PLCs use this data to make decisions, track process variables, and send alerts if abnormalities occur. Effective data acquisition allows operators to monitor the system’s performance, optimize production, and improve quality control.
Data from the PLC is often sent to a central Human-Machine Interface (HMI) or SCADA system, which visualizes the production process for operators. Through the HMI or SCADA, operators can view real-time data, adjust setpoints, and control various aspects of the system. Properly designed data acquisition and monitoring frameworks enable operators to make informed decisions, reducing downtime and enhancing productivity.
Integrating Safety and Redundancy Systems
Safety is paramount in industrial automation, especially when integrating new PLC systems into existing production lines. Engineers design safety interlocks that prevent hazardous conditions by stopping machinery or triggering alarms if specific parameters are exceeded. For example, in a system with moving parts, safety interlocks can ensure that machines halt operation if a safety gate is opened or if an emergency stop button is pressed.
Redundancy is also critical in high-stakes production environments. By creating backup systems, engineers ensure that if one PLC or component fails, another system can take over, minimizing disruption. Redundancy can be implemented at various levels, including backup power supplies, parallel communication channels, and duplicate PLCs programmed to handle critical tasks.
Testing and Validation
Testing is a crucial phase of integration, ensuring that the newly integrated system functions correctly and meets performance expectations. Engineers conduct thorough testing, beginning with simulation and then moving to live tests.
- Simulation Testing allows engineers to validate the logic, communication protocols, and safety features without involving actual machinery, reducing the risk of damage.
- Field Testing is performed once the simulation is successful. Engineers run the integrated system under real-world conditions, verifying that the PLC responds accurately to inputs and communicates effectively with other devices. Field testing often involves “stress testing,” where the system is exposed to various scenarios to identify weaknesses.
Testing also includes verifying that the PLC correctly triggers safety interlocks, that redundancy mechanisms activate as needed, and that data acquisition functions reliably. This validation phase allows engineers to detect and resolve issues before full-scale deployment, protecting both the machinery and the workers.
Calibration and Fine-Tuning
After successful testing, the system is calibrated and fine-tuned to meet the specific needs of the production environment. Calibration adjusts settings to ensure precise performance, accounting for factors like environmental conditions, machine age, and production variables. For instance, in a temperature-sensitive process, calibration ensures the PLC adjusts heating and cooling components accurately within the specified range.
Fine-tuning further enhances system performance by optimizing the control algorithms and adjusting parameters based on real-world observations. Engineers may adjust timing, feedback sensitivity, or alarm thresholds to improve the system’s responsiveness and reliability.
Documentation and Training
Proper documentation is essential for future maintenance, troubleshooting, and potential upgrades. Documentation should include:
- System Overview: A high-level description of the integrated system, including components, protocols, and functions.
- Network Configuration: Details on IP addresses, communication channels, and network architecture.
- Safety and Redundancy: Information on safety interlocks, redundancy features, and emergency procedures.
- Operational Procedures: Step-by-step instructions for operating and monitoring the system.
Training operators and technicians on the new system is also critical to ensure smooth operation. Training includes understanding the HMI, recognizing alarm codes, and knowing how to perform basic troubleshooting. Well-trained staff can respond quickly to issues, minimizing downtime and ensuring that production remains efficient.
Optimization and Continuous Improvement
Even after successful integration, the automation system requires ongoing optimization to adapt to changing production demands. Engineers continuously monitor the system’s performance, identifying opportunities to increase efficiency, reduce energy consumption, and enhance process accuracy. Regular software updates, recalibrations, and hardware upgrades are part of this continuous improvement process, ensuring the system remains competitive and capable of handling future production needs.
Integrating PLC-based automation systems into existing production environments is a multi-faceted process that requires careful planning, rigorous testing, and ongoing optimization. By establishing clear communication protocols, implementing robust safety and redundancy systems, and providing thorough training, engineers enable a seamless transition to advanced automation. This integration not only improves operational efficiency but also enhances the safety, reliability, and scalability of production environments, supporting the long-term goals of industrial facilities.
6. Troubleshooting, Optimization, and Commissioning
Effective troubleshooting, optimization, and commissioning are crucial final steps in deploying a PLC-based automation system. Troubleshooting addresses any issues that may arise during setup or operation, while optimization ensures the system performs at its best. Commissioning is the process of putting the system into active operation and confirming that it meets all performance and safety requirements. Together, these steps contribute to the system’s long-term reliability, efficiency, and safety.
Troubleshooting Common PLC Issues
Troubleshooting is a systematic approach to identifying and resolving problems in PLC systems. Issues can arise from a variety of sources, such as hardware malfunctions, software errors, communication failures, or environmental factors. Engineers use structured methods to isolate and diagnose these problems.
- Identifying Input/Output (I/O) Problems:
- Many PLC issues originate from faulty input or output devices, such as sensors, actuators, or wiring. Engineers often start troubleshooting by verifying that all I/O points are functioning correctly. This involves checking sensors for proper readings and confirming that actuators respond as expected.
- In cases where specific inputs or outputs fail, engineers may trace the wiring connections or replace faulty devices to restore proper function.
- Diagnosing Software Logic Errors:
- Logic errors in PLC programming can lead to unexpected system behavior, such as motors starting or stopping at incorrect times. Engineers review the control logic to ensure all commands and conditions are accurately defined.
- Common software issues include incorrect timer settings, misconfigured comparators, or unintentional loops in the code. Debugging tools in PLC programming software, such as step-by-step execution, allow engineers to identify and correct logic errors efficiently.
- Resolving Communication Failures:
- PLC systems rely on communication networks to exchange data between devices, and failures in these networks can disrupt operations. Engineers troubleshoot communication issues by verifying protocol settings, inspecting network cabling, and checking for signal interference.
- Tools like protocol analyzers and network diagnostic software help identify and address communication faults, such as data packet loss or timing mismatches.
- Addressing Environmental Factors:
- Industrial environments can be harsh, with factors like temperature, humidity, dust, or electromagnetic interference affecting PLC performance. Engineers ensure the PLC is properly shielded, cooled, and protected from environmental hazards. Adjustments may include adding filters, rerouting cables, or installing temperature control systems to maintain stable operation.
Optimizing System Performance
Optimization ensures that the PLC system operates as efficiently as possible, meeting production goals while minimizing costs, energy consumption, and wear on equipment. Optimization is an ongoing process, with adjustments based on system performance data, maintenance feedback, and evolving production requirements.
- Adjusting Control Parameters:
- Fine-tuning control parameters, such as setpoints and PID (Proportional-Integral-Derivative) gains, can improve response times, reduce energy use, and enhance system stability. Engineers analyze historical data to identify areas for adjustment and may increase or decrease control sensitivity based on real-world conditions.
- Enhancing Cycle Time and Throughput:
- Reducing cycle time (the time taken to complete one production cycle) increases overall throughput. Engineers may adjust timing settings, modify logic sequences, or streamline communication between devices to optimize cycle time.
- Techniques like parallel processing, where tasks run simultaneously, or buffer optimization, where data is pre-loaded or pre-processed, can further reduce delays and improve production speed.
- Minimizing Energy Consumption:
- Automation systems often consume large amounts of energy, and optimizing energy usage can result in significant cost savings. Engineers analyze power usage data to identify high-consumption periods and explore options for reducing energy use.
- Optimization strategies may include scheduling non-critical tasks during low-demand periods, adjusting motor speeds, or using energy-saving modes on equipment.
- Implementing Predictive Maintenance Features:
- Predictive maintenance involves monitoring system data to anticipate equipment wear or failure before it happens. By integrating sensors that track parameters like vibration, temperature, or pressure, engineers can identify signs of impending issues and schedule maintenance proactively.
- Predictive maintenance not only reduces downtime but also extends equipment lifespan, as issues are addressed before they cause major damage.
Commissioning the PLC System
Commissioning is the final stage before a PLC system is fully operational. It involves a series of tests and checks to confirm that the system meets performance and safety standards. Commissioning ensures that the system is ready for production and that it operates reliably under real-world conditions.
- Pre-Commissioning Tests:
- Before active commissioning, engineers conduct pre-commissioning tests to validate system components and logic. These tests include verifying I/O functionality, testing communication protocols, and reviewing control sequences. Pre-commissioning allows engineers to catch potential issues early and make adjustments before full deployment.
- System Calibration:
- Calibration ensures that sensors, actuators, and control parameters are correctly set to achieve the desired accuracy and performance. For instance, in a temperature control system, calibration adjusts sensor readings to reflect actual temperature conditions. Calibration also aligns control responses with production targets, ensuring consistent quality and reliability.
- Safety Verification and Risk Assessment:
- Ensuring safety is a critical aspect of commissioning. Engineers validate all safety interlocks, alarms, and emergency shutdowns to protect both operators and equipment. Safety verification involves running failure scenarios to confirm that the system responds appropriately in emergencies.
- Risk assessments are conducted to evaluate potential hazards and confirm that all necessary safety features are in place. Any identified risks are mitigated through adjustments to control logic, additional safety components, or operational guidelines.
- Performance Validation and Acceptance Testing:
- Performance validation tests confirm that the system meets production requirements, such as speed, accuracy, and reliability. Engineers compare system outputs against set standards and make final adjustments to optimize performance.
- Acceptance testing, often conducted with the end-users or plant operators, verifies that the system meets all contractual and operational criteria. Once the system passes acceptance testing, it is officially commissioned and ready for production.
Documentation and Operator Training
After successful commissioning, thorough documentation is created to serve as a reference for system operation, troubleshooting, and maintenance. Documentation typically includes:
- Control Logic Descriptions: Clear explanations of each control sequence and algorithm, making it easier for operators and technicians to understand how the system works.
- Parameter Settings: A record of control parameters, such as setpoints, PID values, and alarm thresholds, to provide a baseline for future adjustments.
- Wiring and Network Diagrams: Visual representations of the PLC’s connections, I/O points, and communication channels, essential for troubleshooting hardware issues.
- Safety and Emergency Procedures: Detailed instructions for handling emergencies and conducting safe shutdowns.
Training operators and technicians on the new system is crucial for smooth operation. Training sessions cover system operation, alarm recognition, and basic troubleshooting steps, ensuring that staff can confidently manage the PLC system and respond to issues promptly. Well-trained operators are essential to maintaining productivity and preventing unnecessary downtime.
Ongoing Monitoring and Continuous Improvement
Even after commissioning, the PLC system requires ongoing monitoring and periodic reviews to ensure optimal performance. Continuous improvement strategies involve analyzing production data to identify potential enhancements, adjusting control parameters, or upgrading software to incorporate new features.
Data collected during operation provides insights into areas where the system can be further optimized. By tracking metrics like cycle time, energy usage, and system uptime, engineers can identify patterns and make informed decisions about future improvements. Regular software updates, recalibrations, and hardware upgrades keep the system up-to-date with the latest industry standards, supporting sustained efficiency and productivity.
Troubleshooting, optimization, and commissioning form the foundation of a reliable and efficient PLC system. Through careful identification of issues, refinement of control parameters, and rigorous testing, engineers ensure the system meets production needs while minimizing downtime and enhancing safety. Proper documentation, training, and ongoing improvement efforts support the long-term success of the PLC system, allowing it to adapt to changing demands and continue delivering high performance in industrial automation.
7. Future Trends in PLC Programming and Automation
The field of industrial automation is evolving rapidly, driven by technological advancements and increasing demands for efficiency, flexibility, and sustainability. PLC programming, as a core component of automation, is influenced by trends that are reshaping how industrial systems operate and interact. From the adoption of Industry 4.0 principles to the integration of Artificial Intelligence (AI) and the Internet of Things (IoT), these trends highlight the direction of modern automation. This section explores key future trends in PLC programming and their implications for industries worldwide.
Industry 4.0 and Smart Manufacturing
Industry 4.0, also known as the Fourth Industrial Revolution, represents the digital transformation of manufacturing through intelligent and interconnected systems. PLCs are central to this transformation, enabling seamless data exchange between machines, systems, and people. With Industry 4.0, PLCs are evolving beyond standalone controllers and becoming integral components of smart manufacturing environments.
- Real-Time Data Collection and Analysis: PLCs in Industry 4.0 environments are equipped with sensors and connectivity that enable real-time data collection. This data is analyzed to optimize processes, reduce downtime, and improve product quality. For example, a PLC in a smart factory may adjust machine settings based on sensor data, preventing equipment wear and minimizing production waste.
- Interconnected Systems: In a smart manufacturing setup, PLCs communicate with each other and with higher-level systems, such as SCADA (Supervisory Control and Data Acquisition) and ERP (Enterprise Resource Planning). This connectivity allows for centralized monitoring and control, making it easier to manage complex production lines and improve overall efficiency.
Internet of Things (IoT) Integration
The Internet of Things (IoT) is revolutionizing how devices interact, with PLCs playing a critical role in this interconnected ecosystem. IoT-enabled PLCs collect and share data with cloud-based platforms, enabling remote monitoring, predictive maintenance, and even automation of control decisions.
- Remote Monitoring and Control: IoT connectivity allows engineers to monitor and control PLCs from remote locations. Through mobile devices or cloud platforms, they can check system status, make adjustments, and troubleshoot issues without being on-site. This capability is particularly valuable in industries with remote or hazardous locations, such as mining or offshore drilling.
- Predictive Maintenance: IoT integration enables predictive maintenance by continuously monitoring equipment health and performance metrics. PLCs with IoT capabilities analyze data, such as vibration, temperature, and pressure, to detect signs of wear or impending failure. Predictive maintenance reduces downtime and extends the lifespan of equipment, lowering maintenance costs.
Artificial Intelligence (AI) and Machine Learning (ML)
Artificial Intelligence (AI) and Machine Learning (ML) are becoming increasingly relevant in industrial automation, with applications ranging from process optimization to predictive maintenance. While traditional PLCs operate based on predefined logic, AI-powered PLCs can learn from data, identify patterns, and make adjustments autonomously.
- Adaptive Control Systems: AI-powered PLCs enable adaptive control, where the system learns from past performance data and adjusts control parameters accordingly. For instance, in a manufacturing line, AI algorithms might learn the optimal speed and temperature settings for different product batches, improving both quality and efficiency.
- Fault Detection and Diagnosis: Machine learning algorithms can analyze historical data to identify patterns associated with faults. AI-driven PLCs use these patterns to detect potential issues before they lead to failure. This capability enhances system reliability and reduces maintenance costs by addressing problems proactively.
Edge Computing in Industrial Automation
Edge computing involves processing data locally, close to the source, rather than relying on cloud-based processing. In industrial automation, edge computing allows PLCs to analyze data and make decisions in real-time, without delays from sending data to and from the cloud.
- Reduced Latency: For time-sensitive applications, such as robotic control or assembly line coordination, even small delays can disrupt operations. Edge computing enables PLCs to process data on-site, reducing latency and ensuring faster response times. This capability is crucial in applications requiring precise timing and synchronization.
- Enhanced Data Privacy and Security: By keeping data processing local, edge computing reduces the amount of data transmitted to the cloud, enhancing data privacy and security. For industries handling sensitive information, such as pharmaceuticals or food production, edge computing helps maintain compliance with regulatory standards.
Cybersecurity for PLC Systems
As PLCs become increasingly connected through IoT and cloud platforms, cybersecurity is becoming a top priority. Cyberattacks targeting industrial systems can lead to production downtime, data breaches, and even equipment damage. Future PLC systems will incorporate advanced security features to protect against these threats.
- Network Security Protocols: PLCs are incorporating robust security protocols, such as encryption and authentication, to safeguard data and prevent unauthorized access. Firewalls, intrusion detection systems, and secure network configurations help protect PLCs from cyber threats.
- Firmware Updates and Patching: Regular firmware updates are essential to maintaining security in connected PLCs. Manufacturers are developing systems to distribute updates securely, ensuring PLCs have the latest protections against known vulnerabilities.
Programming Standardization and Unified Platforms
With the growing complexity of industrial automation, there is a push toward standardized programming languages and unified platforms. Standards such as IEC 61131-3 provide a consistent framework for PLC programming, allowing engineers to work across different PLC brands and models without needing extensive retraining.
- Cross-Compatibility: Standardization simplifies integration in multi-vendor environments, as engineers can use the same programming languages (such as Ladder Logic, Function Block Diagram, or Structured Text) across various PLCs. This cross-compatibility reduces learning curves and enhances flexibility when expanding or updating automation systems.
- Unified Development Environments: Some manufacturers are developing unified platforms where engineers can program, simulate, and deploy automation code across multiple device types. These platforms streamline development and make it easier to manage complex systems with a single toolset, improving efficiency and reducing the likelihood of programming errors.
Sustainability and Energy Efficiency
Sustainability is increasingly influencing industrial automation, as companies seek to reduce energy consumption and minimize their environmental impact. PLCs are being developed with features to monitor energy usage, optimize resource allocation, and support sustainable production practices.
- Energy Monitoring and Optimization: Advanced PLCs include tools to monitor energy consumption in real-time, allowing operators to identify areas for improvement. By analyzing energy data, engineers can adjust equipment settings to reduce waste, leading to both environmental and cost benefits.
- Integration with Renewable Energy Sources: As industries shift toward renewable energy, PLCs are being integrated with solar, wind, and other renewable sources. These systems manage the variable nature of renewable energy by adjusting loads and scheduling non-essential processes during peak renewable generation times, contributing to a greener production process.
The future of PLC programming and automation is marked by increased connectivity, intelligence, and adaptability. As Industry 4.0, IoT, AI, and edge computing continue to influence automation, PLC systems will become even more powerful and flexible, enabling manufacturers to achieve higher levels of efficiency, quality, and sustainability. Engineers must remain up-to-date with these trends to ensure that they can leverage the latest technologies to optimize production processes and meet the demands of modern industrial environments. Embracing these future trends will allow industries to remain competitive, resilient, and responsive to the ever-evolving landscape of industrial automation.
8. Conclusion
PLC programming is a cornerstone of industrial automation, providing the precision and control necessary to optimize complex processes across various industries. This article has explored the essential steps in designing, programming, and commissioning PLC systems, highlighting how these technologies improve efficiency, reliability, and safety in modern production environments. With increasing advancements, PLCs are evolving to meet new demands, and understanding the full scope of these systems is essential for engineers and operators alike.
Designing effective control software is the first step in creating a robust automation system. By carefully selecting a programming language that suits the application—be it Ladder Logic for sequential control or Structured Text for complex calculations—engineers can build solutions that meet specific production needs. Establishing clear and accurate I/O mapping, communication protocols, and control logic creates a solid foundation for effective system functionality.
Developing and implementing control algorithms allows engineers to achieve specific operational goals, whether through open-loop control, closed-loop control, or PID control. Simulation and testing are crucial stages, as they help validate the logic and ensure that the system behaves as expected under various conditions. Calibration and documentation provide the final touches, making future adjustments and troubleshooting simpler and more efficient.
Integrating PLC systems into existing production environments is a strategic process that requires planning, assessment of compatibility, and attention to network communication protocols. As demonstrated, successful integration results in seamless communication between devices, ensuring that data flows accurately and efficiently to support optimized production. Redundancy and safety features add layers of protection, ensuring both equipment and personnel remain safe.
Troubleshooting and optimization are ongoing efforts in maintaining high-performing PLC systems. Engineers continually analyze system data to identify inefficiencies, refine control parameters, and implement predictive maintenance measures. These efforts contribute to maximizing production output, minimizing downtime, and extending equipment lifespan.
Commissioning a PLC system requires thorough validation and testing to confirm its readiness for full-scale production. Proper documentation and operator training ensure that everyone involved in the production process understands the system’s operation, enabling faster response times to issues and reducing the risk of human error. Regular monitoring and optimization further enhance the system’s adaptability to changing production demands, supporting long-term operational goals.
Future trends in PLC programming and automation reflect the growing influence of Industry 4.0, IoT, AI, and edge computing. These technologies offer unprecedented opportunities to improve production, from real-time data analysis to adaptive control systems and remote monitoring capabilities. As these technologies continue to advance, the role of PLCs in industrial automation will only expand, allowing for even greater control and efficiency.
In conclusion, PLC programming remains a critical skill for engineers and technicians in the automation field. As industry demands evolve and new technologies emerge, the flexibility and adaptability of PLC systems make them indispensable tools in achieving sustainable, high-performance production. By mastering the principles of PLC programming and staying informed about future trends, automation professionals can contribute to a more innovative, efficient, and sustainable industrial landscape.