This article critically evaluates the workflows and methodologies guiding tape-out procedures and layout optimization in photonic integrated circuit (PIC) design. Focusing on the software tool KLayout and its integration with foundry services, it dissects the technical, organizational, and cultural challenges associated with preparing PIC designs for fabrication. By reviewing state-of-the-art layout optimization techniques, examining the interplay between design rules and foundry constraints, and highlighting the influence of global supply chains and policy frameworks, the analysis provides actionable insights for engineers. The discussion emphasizes the need for standardized design kits, interdisciplinary collaboration, and education-driven initiatives to streamline workflows and increase yield. Ultimately, this review underscores the importance of adapting design strategies to evolving technical landscapes and aligning engineering practices with broader ecosystem requirements to ensure reliable, high-performance PICs.
Dr. Javad Zarbakhsh, Cademix Institute of Technology, Austria
Table of Contents
Introduction
As photonic integrated circuits mature from research prototypes into commercial products, the pressure to achieve efficient and reliable tape-outs intensifies. Tape-out procedures, once the domain of microelectronics, now guide how engineers translate PIC designs into physical wafer patterns ready for fabrication. Behind the scenes lie subtle dependencies: the layout must satisfy rigorous design rules set by foundries, align with evolving industry standards, and maintain fidelity to the original optical schematics. Engineers face the challenge of ensuring that their carefully simulated circuits reach the foundry floor without suffering from unforeseen geometric errors, device mismatches, or process-induced distortions.
In this changing landscape, tools like KLayout have emerged as indispensable allies. KLayout, known for its user-friendly graphical interface and support for diverse file formats, helps designers visualize complex circuits, apply automated checks, and integrate third-party technology files. Yet, relying on a single tool cannot solve every challenge. The tape-out workflow involves multiple stages: initial design entry, geometric corrections, process rule enforcement, device labeling, final verification, and submission to the foundry. Each step introduces its own complexities, influenced by human factors (engineer experience, communication), organizational culture (adherence to best practices, training availability), and policy frameworks (standardization initiatives, public funding for design tool improvements).
This article aims to shed light on these interconnected aspects of tape-out and layout optimization. It does not promise definitive solutions—no single prescription fits all foundries or every design—but instead offers a broad perspective. Readers will gain an understanding of the technical intricacies of preparing PIC layouts, the strategic importance of foundry integration, and the cultural and organizational shifts needed to optimize workflows. By weaving together technical depth with insights into industry practices, education needs, and policy interventions, the discussion aspires to inform engineers, managers, and decision-makers as they navigate the delicate dance of turning virtual designs into tangible photonic chips.
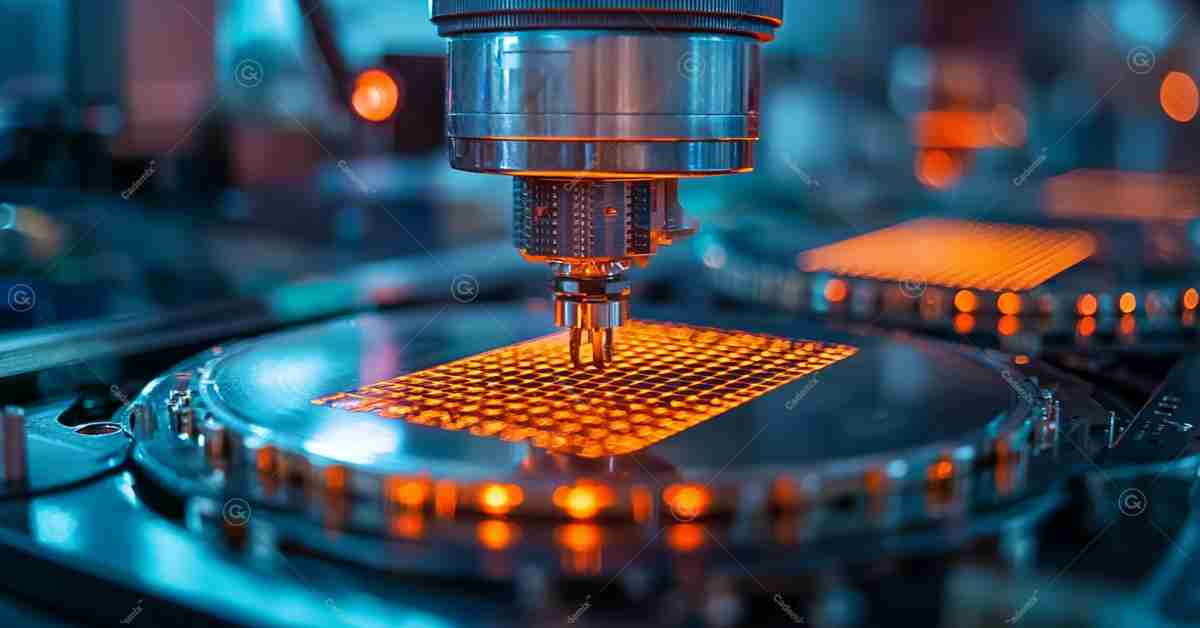
KLayout as a Central Tool in Layout Optimization
KLayout sits at the intersection of usability and functionality, providing a platform for viewing, editing, and verifying PIC layouts. Unlike some proprietary tools constrained by licensing or specialized formats, KLayout’s open-source nature encourages community contributions and the rapid addition of custom scripts. Engineers can leverage this flexibility to develop macros that implement design rule checks (DRCs), enforce minimum spacing constraints, or automatically detect certain geometric anomalies. This adaptability is critical because PIC fabrication processes vary widely, and no single rulebook dictates how to implement every component or coupling structure.
However, KLayout is not a magic wand. Its value depends on the quality of input data, the clarity of foundry-provided process design kits (PDKs), and the skill of the engineers using it. Without comprehensive PDKs specifying device parameters, layer stacks, and acceptable geometric tolerances, designers risk guessing their way through tape-out. In real-world practice, some foundries provide robust PDKs complete with simulation models, component libraries, and process constraints. Others are less mature, leaving designers to rely on trial-and-error or partial information gleaned from limited documentation. KLayout can facilitate bridging these gaps, but only if engineers invest time in customizing checks, validating device geometries, and maintaining close communication with foundry liaisons.
Organizational culture and training also influence KLayout’s effectiveness. If a company prioritizes ongoing education and encourages engineers to develop proficiency in layout tools, KLayout workflows become more streamlined. In contrast, a workforce that lacks training resources or managerial support may underutilize KLayout’s capabilities. Communication channels matter, too. Relying on scattered email threads, outdated wikis, or fragmented notes can hinder knowledge transfer. Centralized documentation systems, internal forums, and mentorship programs can reinforce best practices, ensuring that layout optimization efforts do not rest solely on a few experts.
Engineers must also remain mindful of the evolving nature of photonic design rules. As foundries refine their processes, reduce feature sizes, or add new device layers, the rules embedded in PDKs and DRC scripts must be updated. A static approach to layout optimization is not sustainable. Instead, KLayout’s flexibility can support iterative improvements. Over time, a culture of continuous learning and adaptation will emerge, where design teams treat tape-out procedures as living processes rather than static checklists. This mindset shift aligns with broader industry trends emphasizing agility, knowledge sharing, and multi-stakeholder collaboration in PIC design and fabrication.
Comparing KLayout and Cadence for PIC Photonic Layouts and Electronic Circuits
KLayout and Cadence are two powerful tools used in designing layouts for photonic integrated circuits (PICs) and electronic circuits, each with unique strengths and focus areas. KLayout is a free and open-source layout editor particularly popular for its lightweight nature and flexibility in photonics design. Cadence, on the other hand, is a comprehensive suite often preferred in the semiconductor industry for its robust features, scalability, and tight integration with electronic design automation (EDA) workflows.
Strengths of KLayout
KLayout is highly regarded for its accessibility and extensibility. As an open-source tool, it supports Python scripting, enabling users to customize functionalities according to specific requirements in photonics design. KLayout excels in handling large GDSII files efficiently and is commonly used in academic and research settings due to its cost-effectiveness. It is particularly suitable for photonic layouts because of its adaptability to the custom design rules often required in this domain. Moreover, its user interface is intuitive, making it easier for beginners to adopt.
Strengths of Cadence
Cadence is a market leader in EDA tools, offering advanced capabilities for both electronic and photonic circuits. Its integration with simulation environments and physical verification tools such as DRC and LVS makes it indispensable for production-grade designs. Cadence’s Photonic Design Suite incorporates comprehensive features tailored for PICs, including photonic component libraries, co-simulation capabilities with electronic circuits, and precise fabrication-aware design constraints. For electronic circuits, Cadence provides unmatched support for analog, digital, and mixed-signal designs, making it the industry standard in IC design.
Key Differences: KLayout or Cadence ?
While KLayout is lightweight and versatile, it lacks the deep integration with simulation and verification tools that Cadence provides. KLayout is often used in the early stages of photonic layout design or for quick edits, whereas Cadence is better suited for end-to-end design workflows, including simulation, layout, and verification. Cadence’s ecosystem is designed for scalability, accommodating complex, multi-disciplinary projects, which can include both photonic and electronic components.
Application Context
The choice between KLayout and Cadence depends on the project’s complexity and budget. Research institutions and startups often prefer KLayout for its cost-efficiency and flexibility in prototyping PICs. Larger enterprises working on advanced technologies with strict verification requirements and co-design needs often choose Cadence, despite its higher cost, for its robust ecosystem and comprehensive features. KLayout and Cadence both play essential roles in the domain of PIC and electronic circuit design, catering to different user needs and project scales. For those prioritizing customization and cost-effectiveness, KLayout is a strong contender, while Cadence remains the go-to solution for comprehensive, production-grade designs requiring high accuracy and integration.
Tape-Out Procedures: Bridging Design and Fabrication
Tape-out procedures represent the final bridge between virtual designs and physical wafers. Here, abstraction ends and tangible patterns must conform to photolithography, etching, deposition, and planarization constraints. Unlike purely electronic devices where planar doping and metallization dominate the process, PICs require carefully engineered waveguides, couplers, grating structures, and active elements. These geometries must maintain tight dimensional tolerances to ensure that the optical modes behave as predicted. Minor deviations in waveguide width or thickness can alter propagation constants, coupling efficiencies, or resonant frequencies.
In practice, tape-out involves multiple verification steps to confirm that the layout obeys foundry rules. Designers often run DRC scripts that detect violations of minimum spacing, overlap, or layer misassignments. They might then apply layout vs. schematic (LVS) checks to ensure the physical geometry matches the intended circuit design. Once the layout passes these checks, the final geometry is typically exported to standard file formats (e.g., GDSII or OASIS) and sent to the foundry. Delays at this stage can be costly. If errors are discovered late, engineers must iterate again, pushing back fabrication schedules and incurring extra costs.
Cultural and psychological aspects also come into play. Engineers may feel pressure from managers or clients to finalize a design quickly, risking insufficient verification. On the other hand, excessive caution and repetitive checks might slow progress. Finding the right balance demands organizational support for robust workflows. Some teams embrace peer reviews or multi-step sign-off procedures, ensuring that multiple experts examine the layout before submission. Mentorship programs that pair junior designers with experienced tape-out engineers can accelerate learning while mitigating the risk of overlooked details.
External factors like global supply chains and policy frameworks also influence tape-out procedures. Certain foundries specialize in specific material platforms or process steps. Policy decisions—such as subsidies for domestic fabrication facilities or international trade agreements—can shape which foundries engineers choose. In turn, the chosen foundry’s capabilities and documentation standards affect how tape-out unfolds. Without transparent communication from the foundry, engineers may rely heavily on guesswork, leading to suboptimal designs and reduced yields. Conversely, a foundry that invests in clear guidelines, timely updates, and user-friendly PDKs empowers engineers to optimize layouts confidently.
Foundry Integration and the Role of Standardized Design Kits
The success of any tape-out depends on close integration with the chosen foundry. While KLayout and internal design rules can guide initial efforts, true optimization requires alignment with foundry-supplied PDKs. These PDKs bundle critical information: layer definitions, device footprints, recommended geometries, simulation models, and DRC rules. They also reflect the foundry’s experience, capturing lessons learned from previous runs and adapting to process improvements. Standardized PDKs allow designers to trust that following certain guidelines will produce yield-friendly layouts that respect lithographic limits, material stress conditions, and thermal budgets.
However, not all foundries offer equally mature PDKs. Smaller or newer foundries might lack comprehensive libraries. Engineers in such scenarios must rely on incomplete data, experiment with multiple layouts, and potentially accept higher risk. This discrepancy can discourage smaller businesses or research institutions from using certain foundries, skewing the industry toward a handful of well-equipped players. The resulting concentration of know-how might stifle competition, limit innovation, or increase dependency on a few dominant service providers.
Cultural and educational strategies can mitigate these issues. If industry consortia or professional bodies collaborate to define common standards for PIC PDKs, consistency across foundries could improve. Joint initiatives can encourage knowledge sharing, reducing fragmentation. For instance, the European Union’s research projects or the U.S. National Photonics Initiative could fund workshops, training modules, and open-source libraries to unify PDK standards. The result would be a more predictable design environment, lower barriers for newcomers, and healthier global competition.
Engineers must also be open to adapting their workflows to each foundry’s requirements. While universal standards remain a goal, practical differences will persist. Learning to navigate these variations is a valuable skill. Mentorship and continuous training ensure that engineers develop intuition about how to interpret a given PDK and adjust layouts accordingly. A flexible mindset also helps teams handle sudden changes, such as a foundry updating a process step or introducing a new device layer. In a field as dynamic as PIC fabrication, adaptability is an asset.
Challenges in Layout Optimization and Potential Remedies
The path to layout optimization is strewn with challenges. At the technical level, dealing with complex component arrangements can push KLayout’s capabilities. Automated checks can flag thousands of minor violations that may require human judgment to resolve. Searching for optimal device placements or minimizing insertion loss often leads to nonlinear optimization problems. Engineers might spend hours tweaking layouts, only to discover that a small fabrication tolerance forces them to revert to a previous design iteration. The resulting time pressure can create frustration and fatigue, especially if organizational policies favor quick fixes over structural improvements.
At the cultural level, organizations may undervalue rigorous layout optimization. If management measures success solely by the number of tape-outs per quarter, teams might rush to submission without thorough checks. Alternatively, if the workforce lacks interdisciplinary training, optical engineers might struggle to understand fabrication constraints, while process engineers might not fully appreciate optical mode shaping. Bridging these cultural divides requires deliberate strategies. Cross-training engineers in both optical physics and fabrication processes, encouraging interdisciplinary dialogues, and promoting knowledge-sharing events can all improve the collective ability to tackle layout optimization issues.
Policy interventions can also help. Funding agencies might support research on advanced design automation tools, including AI-driven algorithms that propose optimal layouts under given constraints. Openly available training materials and best-practice guidelines, supported by industry consortia, can raise the baseline competence of the entire workforce. If policymakers incentivize transparency in foundry services—such as requiring foundries to publish certain process details or performance metrics—engineers can make more informed decisions, reducing guesswork and trial-and-error.
Yet, no single remedy will solve every challenge. The complexity and interdependencies suggest that incremental improvements must accumulate over time. Establishing a culture of continuous improvement, where each tape-out run yields lessons for the next, is crucial. Over multiple design cycles, teams gain experience, refine DRC scripts, and update PDK interpretations. In turn, foundries learn from returned feedback, improving their documentation and technology files. This iterative loop, fueled by trust and open communication, can gradually alleviate the pains of layout optimization.
Conclusion and Call to Action
Tape-out procedures and layout optimization represent critical junctures in the PIC design process, where theoretical plans meet the realities of foundry fabrication. Tools like KLayout, robust PDKs, and well-defined workflows can significantly streamline these efforts, but the underlying challenges are multifaceted. Technical issues—such as complex geometries and nonlinear optimization—intersect with cultural, organizational, and policy-based factors. Without careful attention to training, communication, and standardization, even the most advanced design environments may struggle to achieve consistent, high-yield outcomes.
Addressing these challenges calls for a multidimensional approach. Engineers must embrace continuous learning, developing not only tool proficiency but also an appreciation for the fabrication constraints that shape PIC performance. Organizations should foster a culture of collaboration, where experts in optics, microfabrication, and software engineering share insights freely. Policy interventions that encourage standardized PDKs, knowledge exchange forums, and open documentation can reduce fragmentation and level the playing field. Programs like professional training workshops, open-source library initiatives, and industry-sponsored mentorship networks can guide newcomers and veterans alike.
If stakeholders commit to this holistic strategy, layout optimization can evolve from a bottleneck into a robust, efficient stage of PIC development. By investing in education, communication, and incremental improvements, the entire ecosystem stands to benefit: foundries achieve higher yields, engineers save time and reduce stress, researchers can push more complex designs, and industry at large reaps the rewards of stable, scalable photonic integrated circuits. In an era where photonics promises to revolutionize computing, sensing, and communication, refining tape-out procedures and layout optimization is not just a technical necessity—it is a strategic imperative for the future of the field.
References and Further Reading
Bogaerts, W., & Chrostowski, L. (2018). Photonic integrated circuit design automation: past, present, and future. IEEE Nanotechnology Magazine, 12(2), 20–29. https://doi.org/10.1109/MNANO.2018.2819409
Flamini, F., Spagnolo, N., & Sciarrino, F. (2018). Photonic quantum information processing: a review. Reports on Progress in Physics, 82(1), 016001. https://doi.org/10.1088/1361-6633/aad5b2
Nielsen, M. A., & Chuang, I. L. (2010). Quantum Computation and Quantum Information: 10th Anniversary Edition. Cambridge University Press. https://doi.org/10.1017/CBO9780511976667
Perez, D., Gasulla, I., & Capmany, J. (2017). Field-programmable photonic arrays. Optics Express, 25(3), 282–294. https://doi.org/10.1364/OE.25.000282
Politi, A., Matthews, J. C. F., Thompson, M. G., & O’Brien, J. L. (2009). Integrated quantum photonics. IEEE Journal of Selected Topics in Quantum Electronics, 15(6), 1673–1684. https://doi.org/10.1109/JSTQE.2009.2026060
Soref, R. (2010). The past, present, and future of silicon photonics. IEEE Journal of Selected Topics in Quantum Electronics, 16(1), 167–176. https://doi.org/10.1109/JSTQE.2009.2035196
Wang, J., et al. (2018). Multidimensional quantum entanglement with large-scale integrated optics. Science, 360(6386), 285–291. https://doi.org/10.1126/science.aar7053
Xu, X., et al. (2020). Photonic inverse design: from fundamentals to applications. Advanced Optics and Photonics, 12(3), 828–887. https://doi.org/10.1364/AOP.381966
Zhang, H., et al. (2021). Integrated quantum photonics: current status and future prospects. APL Photonics, 6(7), 071101. https://doi.org/10.1063/5.0045024
European Quantum Flagship. (2021). Strategic Research Agenda for Quantum Technologies. https://qt.eu/roadmap
Zarbakhsh, J. (2022) From Photonic Crystals to PICs: Educational Insights into Lumerical and Synopsys Simulation Tools for Quantum-Enhanced Circuits