The main agenda of FMEA is to reduce the effects and failures during the design and production process in manufacturing industries.
By Jyothsna Sai Swaroop Surisetty, Associate Consultant in R&D and Career Coaching, Cademix Institute of Technology
Introduction of Failure Mode and Effects Analysis (FMEA)
Over the decades, FMEAs have been used as a method to detect and minimize risk. Firstly, in the 1940s, the US military used the commonly recognized FMEAs. They developed the technique to minimize variance sources and subsequent possible failures in munitions production – and proved a highly successful method. After that automotive industry started to adapt to FMEA in the 1970s.
There are many examples of products that are poorly designed or processed, that we will review in the following. In fact, these product failures are discussed in the public where manufacturers, service providers, and suppliers are shown to be incapable of providing a safe product. However, to overcome these problems FMEA is one of the precise tools that is used to reduce failures. We will discuss the pros and how it works in large, medium, and small scale industries.
The word “Failure modes” means how something could go wrong or how it might go wrong. That means it includes errors or defects that may be potential or actual, particularly those affecting the customer.
The word “Effects analysis” refers to the study of the impacts of these deficiencies.
FMEA is not a substitute for good engineering but it improves good engineering by applying the knowledge and experience of certain Teams. It is to check the progress of the design of a product or process by measuring its risk of failure.
Types of FMEA
FMEA is divided into two categories:
Design FMEA: It examines the possibilities for product malfunctions, reduced product lifecycle, and safety regulations. Below are a few things that should take into consideration before designing a product
- Material properties
- Tolerances
- Interfaces with other parts
- Geometry
Process FMEA: It Identifies failures affecting product quality, reduced process reliability, customer complaints, and safety or potential pollution that can be obtained from materials. Here are some important factors while such as
- Human concerns
- Methods adopted during handling
- Materials used
Advantages
Firstly, It improves a manufacturing firm’s efficiency by exploring the FMEA process Secondly, it reduces the development time and cost during the production process. Also, FMEA reduces the time required to take into account possible conflicts with the design concept and prevents the breakage of vital elements of the project. Likewise, it helps define characteristics of critical quality.
Reason for Failure Mode and Effect Analysis (FMEA) in Manufacturing Industries
While design or manufacturing a product, it’s better to identify the failures at the starting point of the process, or else the impact will show deadly results at the ending stage which leads to poor performance.
Below are some of the following examples:
- Improves Design for Manufacturing and Assembly (DFMA)
- It Open doors to solve many severe problems
- Solutions for cost reduction
- Continuous improvement, Process improvement is possible
- Collaboration among product design and process.
When to Perform Failure Mode and Effects Analysis (FMEA) in Manufacturing Industries
- When you want to develop a new product, service, or process
- If you choose to perform the procedure in a different way
- When you want to target a particular phase of change
In addition to that, an FMEA should occasionally be carried out throughout the process. On the other hand, for optimal results, quality and reliability have to be consistently checked and improved.
How to Execute Failure Mode and Effects Analysis (FMEA) in Production Industries
FMEA is carried out in seven steps and these steps are divided so that to ensure that each move is attended by exactly the right team members. Here is the sample example that how FMEA works in these seven steps
Function | Type of failure | Impact | Severe | Major cause | OCC | Identify | RPN |
Analyse the material in brief | What leads to go wrong | What is the major impact? | How bad is it to the customer | Reason for the cause? | How often is the occurrence? | How easy is it to identify | Risk priority number |
PVC profiles (Polyvinyl chloride) function: Specially used in doors and windows , durable material | Long and flat window profiles | Unable to use the product as it doesn’t reach the exact requirements such as size, shape, colour and internal faults | 10 | Quality of the product and lack of mechanical properties of the material | 4 | 5 | 200 |
Action Needed | Responsibility | Action taken | Severe | OCC | Identify | RPN |
What are the possibilities in reducing the causes? | Who is responsible? | What actions are taken into account? | ||||
Replacing the item and better to have extra profiles | Manufacturer | Replacement of the item and carrying out additional profiles | 4 | 3 | 5 | 60 |
After a detailed analysis by the group of members, the team will be able to calculate the risk priority number (RPN) = Severity * Occurrence * Identify
Here is the step by step analysis of a product that is shown below to overcome the failures
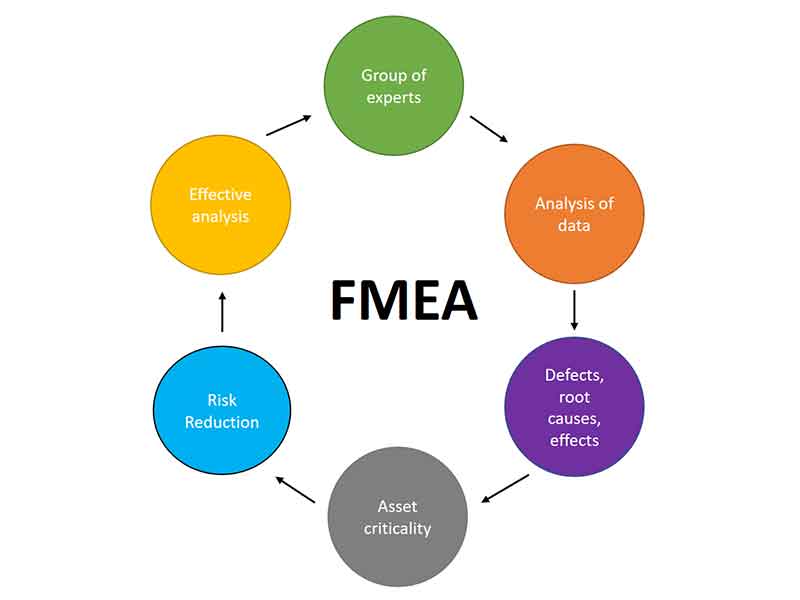
Setting Preferences
Thus from the above table, it can be seen that once all failure modes have been identified, the team should modify the FMEA to mention the failures in the RPN descending order. There is no definite RPN threshold which areas should be the most carefully considered. It depends on a variety of factors, including market requirements, legal and security standards, and regulations. Likewise, the starting point for prioritization is the application of the Pareto rule typically, 80% of issues are caused by 20% of potential problems. As a rule of thumb, teams can initially focus their attention on failures with the top 20% of the highest RPN scores.
Making Corrective Actions
Once goals are decided, one of the last steps of the team is to establish adequate corrective measures to minimize or at least improve the frequency of fault modes. The FMEA leader should take over these steps and set target completion dates
After corrective steps have been taken, the team can meet again to evaluate and assess the severity, probability of identification of the top modes of failure. This would make it easier for them to measure the efficacy of corrective measures. These tests may be beneficial if the team determines that new disciplinary steps must be implemented in Product development
FMEA Relationship to Problem Solving
Failure modes in an FMEA are similar in problem solving to a problem statement or problem description. Causes in an FMEA are the same in problem solving as possible root causes.
- In the verification of the root cause and continuous corrective action, design or process controls in an FMEA (PCA).
- For future product planning or process consistency, data obtained from problem-solving shall be included in an FMEA. In order to make FMEA more efficient and complete, it should accept real failures, defined as failure modes and triggers.
Related keywords for manufacturing industries:
Analyze, Six Sigma, Design Process, Automotive, Root cause analysis, Process control, Cross-functional, Failure analysis, Mitigate, fabrication, Corrective action, Aerospace, Hazard
Methodologies, Prioritize, Severity, Problem-solving, Fault tree analysis, Reliability engineering, Worksheet, High risk, Defect. Lean Six Sigma, Handbook, Criticality, DFMEA, PFMEA, Risk analysis, Preventive