This article critically analyzes the complex relationship between semiconductor fabrication methods and optical packaging challenges in quantum integrated photonics, examining the limitations of foundry services, the influence of organizational and policy frameworks, and the intricacies of device characterization protocols. By highlighting barriers in scalability, reproducibility, and long-term reliability, it underscores the need for strategic interventions, interdisciplinary collaborations, and standardized practices to ensure that emerging quantum photonic devices transition effectively from laboratory concepts to manufacturable, high-fidelity systems. This discussion provides a comprehensive understanding of the current landscape and suggests directions for improved fabrication tolerance, robust packaging solutions, and enhanced foundry infrastructure.
By: Dr. Javad Zarbakhsh, Cademix Institute of Technology
Table of Contents
Introduction
The promise of quantum integrated photonics has driven an intense effort to translate laboratory-scale quantum optical experiments into manufacturable technologies that can be deployed on a large scale. Within this evolving landscape, semiconductor fabrication processes and optical packaging strategies represent crucial pillars determining whether these quantum photonic devices can truly achieve the performance, scalability, and cost-effectiveness necessary for practical applications. Quantum integrated photonics draws upon well-established manufacturing methods borrowed from the semiconductor industry, yet the unique requirements imposed by quantum protocols introduce complexities that exceed those encountered in classical photonics or electronics.
The challenges are multifaceted. On one hand, the semiconductor fabrication of quantum photonic devices demands extraordinary control over material quality, layer thickness, waveguide dimensions, and integration with specialized quantum components such as single-photon detectors or entangled photon sources. On the other, optical packaging, often underappreciated, must ensure stable coupling of external fibers, accurate alignment of quantum optical elements, and long-term reliability in potentially harsh operating environments. Achieving this delicate balance is further complicated by the scarcity of foundry services tailored to quantum needs, the lack of standardized design libraries, and the absence of universally accepted metrics for device characterization.
This review takes a critical stance, examining both the technical and policy dimensions that shape semiconductor fabrication and optical packaging in quantum integrated photonics. Rather than proposing definitive solutions, the emphasis lies on uncovering latent obstacles and systemic issues that stand between current prototypes and commercially viable devices. By considering the interplay of technical constraints, organizational cultures, global funding policies, and the human skill sets required for this emerging field, we aim to illuminate paths that might guide future endeavors. Ultimately, the journey from conceptual quantum devices to industrial-scale fabrication lines underscores the urgency of addressing these challenges and adopting long-term strategies that promote reproducibility, scalability, and sustainable growth in the quantum photonics sector.
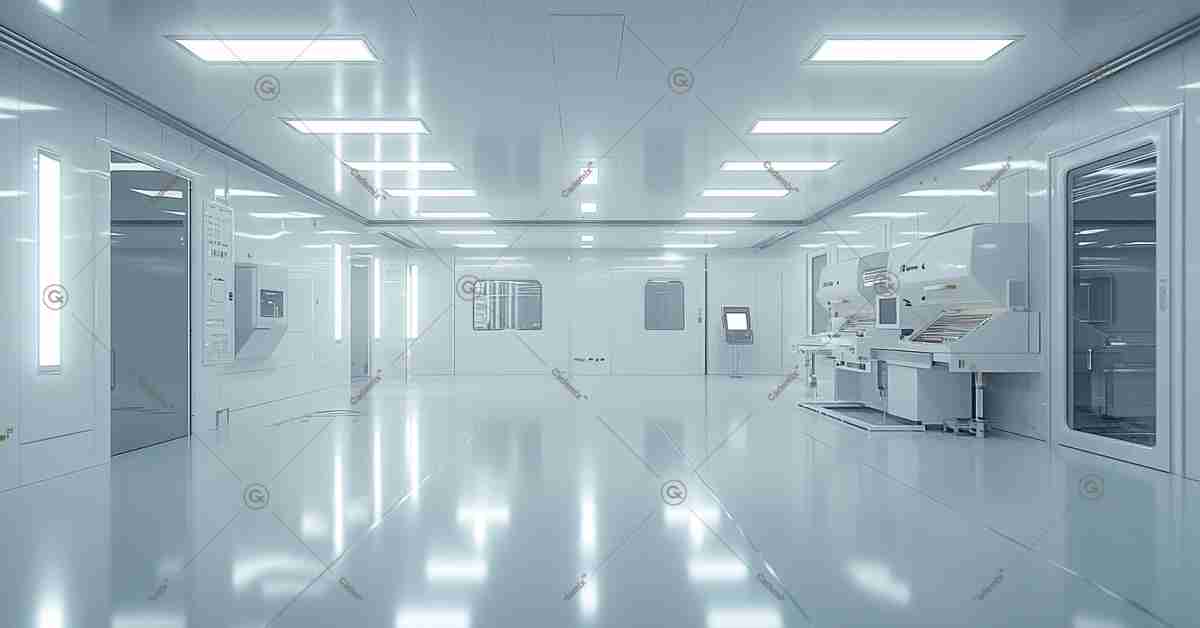
Historical Roots and Evolution of Semiconductor Fabrication in Photonics
Semiconductor fabrication, a process once confined to the microelectronics industry, has witnessed a steady evolution as photonics emerged as a complementary technology. Historically, the techniques developed for silicon chips—photolithography, etching, doping, and thin-film deposition—provided a robust framework for integrated photonics. Silicon photonics, in particular, benefited from the microelectronics ecosystem, allowing for CMOS-compatible manufacturing that leveraged existing infrastructure and expertise. Early integrated photonic circuits targeted classical communication and signal processing, seeking low-loss waveguides and compact modulators.
However, the advent of quantum integrated photonics has exposed limitations in applying these established processes wholesale. Where classical photonics could tolerate small variations or slightly elevated loss parameters, quantum applications often demand ultra-low loss and exquisite phase stability. Even minor imperfections during fabrication—subtle sidewall roughness, non-uniform doping, or layer thickness deviations—can degrade the coherence of single photons or reduce the fidelity of quantum gates. As a result, fabrication tolerances must be tightened, and quality control becomes paramount. Many existing foundries are not yet equipped to meet these demands, and the required improvements will likely involve both technical refinements and strategic investments.
Despite these hurdles, the foundational principles guiding semiconductor fabrication remain relevant. Cleanroom environments, controlled deposition and etching processes, and advanced metrology tools continue to underpin the fabrication of waveguides, couplers, resonators, and detectors. The transition from classical to quantum integrated photonics does not require discarding these methods, but rather refining and extending them. Achieving uniformity across wafers, controlling stress in layers, and developing novel etching chemistries to ensure smooth sidewalls can all build on proven techniques, albeit guided by more stringent specifications.
The Quantum Context: Why Fabrication Matters for Fidelity
Quantum photonic devices rely on manipulating and measuring individual photons or small ensembles that retain quantum coherence. For instance, a quantum photonic chip might implement a linear optical quantum gate based on interference in waveguides, or generate entangled photon pairs through nonlinear processes. In each scenario, the device performance is intimately linked to fabrication-induced losses, scattering, and phase drifts. These are not merely technical nuisances—they strike at the heart of the quantum advantage. Even a few additional dB of loss across the chip can drastically reduce the probability of successful quantum operations, undermining scalability.
Beyond loss, device fidelity depends on uniform component behavior. Quantum protocols often assume identical performance from multiple identical elements, such as identical phase shifters or couplers. Fabrication variations that yield slightly different waveguide widths or refractive index profiles across the wafer translate into non-uniform phase shifts and coupling ratios. Such discrepancies accumulate as photons traverse complex circuits. In a field where quantum states are fragile and interference patterns must be pristine, the lack of component uniformity quickly compromises results.
As a result, fabrication processes tailored to quantum photonics must meet stricter metrics. They require wafer-scale uniformity, improved reproducibility, and reduced roughness. Techniques like chemical mechanical polishing, advanced lithography, and low-temperature deposition might help. Similarly, foundry services interested in serving quantum customers must develop process design kits with tighter specifications, or offer customization options that allow researchers to tune the fabrication recipe for their quantum device architectures. Achieving this level of refinement presents both a technical and organizational challenge, as it involves bridging a gap between the general-purpose capabilities of many foundries and the specialized demands of quantum photonic users.
Optical Packaging: The Overlooked Bottleneck
While semiconductor fabrication often dominates the conversation, optical packaging represents another formidable bottleneck. Packaging refers to the series of steps that encase and protect the chip, align input and output fibers, and integrate additional components such as lenses, beam splitters, or detectors. For quantum integrated photonics, packaging must be executed with extreme precision to avoid coupling losses or mode mismatch that would erase quantum correlations or reduce single-photon detection efficiencies.
The difficulty lies partly in the fact that quantum photonic devices often require operation at cryogenic temperatures, integration with superconducting detectors, or complex mode engineering that cannot be realized by simple butt-coupling a fiber to a waveguide. Packaging solutions that work for classical photonics may fall short here. Complex alignment procedures, on-chip mode converters, or 3D-printed micro-optics might be required to achieve acceptable coupling efficiencies. These methods introduce additional steps, costs, and risks of mechanical failure over the device’s lifetime.
Packaging challenges cannot be separated from fabrication constraints. The design of the chip itself must consider how it will be packaged downstream. If the waveguide facets are not well-defined or if the coupling region does not match standard fiber modes, packaging technicians must resort to ad hoc solutions, adding complexity and cost. This interplay suggests that packaging and fabrication teams must collaborate more closely, working from the beginning of the design cycle to ensure that both chip structure and packaging workflow are aligned toward a common goal: stable, low-loss optical coupling that preserves quantum states.
Foundry Services and Their Limitations
Many in the photonics community have looked to foundry services as a means of democratizing access to high-quality fabrication. Foundries typically offer standardized process flows, design rules, and component libraries, allowing customers to submit layouts without needing their own cleanroom facilities. This model has served classical photonics well, enabling small companies and academic groups to experiment with integrated circuits at a reasonable cost. Yet, for quantum integrated photonics, foundry services may not always meet the specialized needs.
One key limitation is that foundries tend to optimize for volume production and standard component sets, while quantum prototypes often require custom designs, materials, or processes. A foundry optimized for telecom wavelengths and classical modulators may struggle to adapt to single-photon detectors or nonlinear materials needed for entangled photon generation. The result is a tension: quantum researchers want custom solutions, but foundries seek stable, repeatable processes that minimize risk and uncertainty.
Moreover, the intellectual property and confidentiality frameworks at foundries can restrict knowledge sharing and slow down iterative improvements. If a researcher cannot access certain process details, adjusting their design to mitigate fabrication issues may be challenging. This lack of transparency hinders the open exchange of best practices that could accelerate progress. To overcome these limitations, some argue for the establishment of specialized quantum photonic foundries or public-private partnerships that blend academic flexibility with industrial rigor. Such entities could create tailored process design kits, host training programs, and encourage standardized characterization protocols that benefit the entire community.
Organizational and Cultural Factors in Scaling Quantum Photonics
As quantum integrated photonics matures, organizational and cultural challenges increasingly influence how semiconductor fabrication and packaging are approached. Traditional semiconductor culture emphasizes mature, proven processes and high yields, while the quantum photonics domain, still in a nascent stage, often values exploratory approaches, rapid iteration, and unconventional materials. Bridging these cultural differences requires new models of collaboration.
One approach is to foster interdisciplinary teams that combine the expertise of quantum physicists, photonic engineers, and semiconductor manufacturing specialists. These teams can better understand each other’s constraints and requirements, reducing miscommunications that lead to suboptimal designs or unrealistic expectations. Academic curricula and industry training programs that emphasize system-level thinking, encouraging engineers to understand quantum protocols and physicists to appreciate fabrication tolerances, can also break down cultural silos.
Policy frameworks and funding mechanisms can shape organizational behavior. For instance, large-scale international programs, like the European Quantum Flagship or US National Quantum Initiative, incentivize collaboration across domains and organizations. By linking funding to demonstration of reproducibility, scalability, and practical device characterization, these initiatives can push stakeholders to align their efforts more closely with industrial standards and commercialization goals. In this way, the organizational culture shifts from academic curiosity-driven exploration to a more structured approach that includes robust fabrication processes and reliable packaging solutions.
The Impact of Policy and Funding Structures
Policy interventions and funding structures have the potential to accelerate or stall the development of quantum integrated photonics. By directing resources toward strategic areas—such as improving foundry capabilities for quantum devices or funding packaging research—governments and consortia can lower barriers that currently impede progress. Well-structured calls for proposals can mandate coordination between fabrication facilities, device designers, and end-users, ensuring that the resulting technologies align with real-world needs.
However, policy also comes with risks. Overemphasis on short-term deliverables or a narrow set of metrics can create incentives to pursue incremental improvements rather than fundamental breakthroughs. If funding agencies demand quick successes, researchers may focus on low-risk fabrication tweaks rather than investing in radical new processes that could yield leaps in performance. Balancing this tension requires policies that support both incremental refinements and exploratory research paths, acknowledging that quantum integrated photonics is still evolving and that long-term gains might outweigh immediate deliverables.
Moreover, policy can influence the development of standardized testing and characterization protocols. Without common benchmarks, it is difficult to compare devices from different foundries or packaging solutions from different providers. Standardization, if encouraged by policy frameworks, helps stabilize expectations, reduces guesswork, and allows the market to mature around well-defined metrics. Such stabilization could, in turn, attract private investment, further expanding the capabilities of foundries and packaging houses and improving the overall ecosystem.
Device Characterization: The Underlying Metrics of Success
Characterization protocols serve as the bridge between fabrication outputs and the performance metrics demanded by quantum applications. Without reliable measurement techniques and benchmarks, claims of device quality or scalability remain speculative. Yet, characterizing quantum integrated photonics poses unique challenges. Measuring single-photon transmission, assessing entanglement fidelity, or verifying low-loss waveguide performance at cryogenic temperatures each requires specialized setups and instruments.
Inadequate or inconsistent characterization can hide fabrication flaws or packaging issues. For instance, a device might appear to have acceptable losses at room temperature and classical intensities, only to fail when tested at single-photon levels or in cryogenic conditions. Characterization tests must thus mirror operational scenarios as closely as possible, and standards must emerge to guide these procedures. Once reliable characterization tools and benchmarks are in place, foundries can offer guaranteed specifications, and designers can confidently select processes and materials that meet their quantum requirements.
Developing these characterization protocols necessitates an interdisciplinary effort. Metrologists, quantum physicists, and industrial testing laboratories must converge to define relevant parameters, acceptable tolerance ranges, and methods to probe device performance across various operational regimes. Published reference data, open-access databases of material properties, and shared test protocols could expedite progress. Without these common yardsticks, evaluating competing fabrication processes or packaging strategies remains guesswork.
Psychological and Cultural Dimensions of Technology Adoption
Beyond policy and organizational factors, psychological and cultural elements also shape the path to scalable quantum photonics. Many researchers and engineers have grown accustomed to established microelectronic workflows and might feel uneasy venturing into quantum territory with its unusual device structures, nonlinear materials, and nonstandard operating conditions. Overcoming this hesitation requires educational initiatives, clear communication of success stories, and demonstration projects that show how refined fabrication processes and careful packaging can indeed produce stable quantum devices.
Cultural norms influence whether organizations embrace external collaborations. Some foundries or packaging firms might prefer to keep their methods proprietary, fearing that sharing knowledge will undermine competitive advantage. Such insularity can slow the collective progress necessary for quantum integrated photonics to thrive. Shifting cultural attitudes to embrace pre-competitive collaboration, where stakeholders share baseline information and jointly develop certain standards, could dramatically lower entry barriers for new players.
Education plays a key role in changing mindsets. If academic programs introduce quantum photonics concepts early, highlight the importance of reproducible fabrication, and involve students in interdisciplinary research projects, the next generation of professionals will enter the workforce already comfortable navigating these complexities. Over time, these cultural shifts can accumulate, making the adoption of improved fabrication and packaging methods more seamless and widespread.
Strategies for Overcoming Technical and Organizational Barriers
While this review focuses on challenges rather than definitive solutions, discussing potential strategies can provide a sense of direction. Technically, improving fabrication tolerances could involve deeper integration of inverse design methodologies, machine learning algorithms to optimize process parameters, or advanced metrology tools to detect nanoscale imperfections early in the manufacturing line. Packaging approaches might benefit from more robust 3D integration, micro-optical elements tailored to quantum wavelengths, and stable cryogenic packaging technologies that maintain precise alignment over time.
On the organizational front, fostering closer relationships between foundries, research institutions, and industry partners can streamline the feedback loop between design, fabrication, and characterization. Collaborative consortia, funded by governmental programs, might serve as neutral grounds where participants share insights, challenge assumptions, and develop collective strategies for improvement. These consortia could pilot testbeds where different packaging solutions are tried and characterized using standardized protocols, enabling the community to converge on best practices more rapidly.
Culturally, initiatives that encourage open science, transparency in reporting fabrication yields, and open-access libraries of reference devices can demystify fabrication processes. A collective effort to publish data on process variability, packaging alignments, and long-term device stability could encourage a community-driven approach to improvement. As trust grows among stakeholders, joint ventures may emerge, tackling shared problems and accelerating innovation.
Conclusion and Call to Action
The complexity of semiconductor fabrication processes and optical packaging in quantum integrated photonics underscores a fundamental truth: the path from laboratory curiosity to industrial-scale technology is neither linear nor guaranteed. Current challenges—ranging from the ultra-tight fabrication tolerances required by quantum protocols to the delicate alignments needed for reliable optical packaging—highlight that quantum integrated photonics is still evolving. Solutions will not come from isolated efforts but from systemic interventions that align technical capabilities with organizational structures, policy incentives, and cultural attitudes.
Addressing these challenges demands a multifaceted approach. Foundry services must evolve to accommodate quantum-specific needs, embracing tighter controls, custom process design kits, and transparent communication channels. Packaging techniques must advance beyond traditional fiber-to-chip couplings, integrating novel optical elements and stable cryogenic solutions. Characterization protocols require standardization and consistency, ensuring that device metrics are not subject to interpretive ambiguity. Policy frameworks can guide resource allocation, incentivize collaboration, and encourage the development of open standards, while educational initiatives can prepare a workforce comfortable in this interdisciplinary space.
The call to action is clear. Stakeholders—researchers, engineers, policymakers, investors, and educators—must engage in a deliberate, coordinated effort. By identifying and confronting the barriers in semiconductor fabrication, optical packaging, and foundry services, the quantum photonics community can chart a path towards scalable, reliable devices that meet the stringent requirements of emerging quantum technologies. In doing so, they not only accelerate progress in quantum integrated photonics but also contribute to a broader ecosystem of innovation, where foundational insights and strategic vision shape the technologies that define our future.
References and Further Reading
Bogaerts, W., & Chrostowski, L. (2018). Photonic integrated circuit design automation: Past, present, and future. IEEE Nanotechnology Magazine, 12(2), 20–29. https://doi.org/10.1109/MNANO.2018.2819409
Carolan, J., Harrold, C., Sparrow, C., MartĂn-LĂłpez, E., Russell, N. J., Silverstone, J. W., Shadbolt, P. J., Matsuda, N., Oguma, M., Itoh, M., Marshall, G. D., Thompson, M. G., Matthews, J. C. F., Hashimoto, T., O’Brien, J. L., & Laing, A. (2015). Universal linear optics. Science, 349(6249), 711–716. https://doi.org/10.1126/science.aab3642
Flamini, F., Spagnolo, N., & Sciarrino, F. (2018). Photonic quantum information processing: a review. Reports on Progress in Physics, 82(1), 016001. https://doi.org/10.1088/1361-6633/aad5b2
Nielsen, M. A., & Chuang, I. L. (2010). Quantum Computation and Quantum Information: 10th Anniversary Edition. Cambridge University Press. https://doi.org/10.1017/CBO9780511976667
Nian, L., et al. (2020). Scaling and performance analysis of silicon photonics for quantum computing. Optics Express, 28(10), 14893–14912. https://doi.org/10.1364/OE.386638
Perez, D., Gasulla, I., & Capmany, J. (2017). Field-programmable photonic arrays. Optics Express, 25(3), 282–294. https://doi.org/10.1364/OE.25.000282
Politi, A., Matthews, J. C. F., Thompson, M. G., & O’Brien, J. L. (2009). Integrated quantum photonics. IEEE Journal of Selected Topics in Quantum Electronics, 15(6), 1673–1684. https://doi.org/10.1109/JSTQE.2009.2026060
Soref, R. (2010). The past, present, and future of silicon photonics. IEEE Journal of Selected Topics in Quantum Electronics, 16(1), 167–176. https://doi.org/10.1109/JSTQE.2009.2035196
Wang, J., et al. (2018). Multidimensional quantum entanglement with large-scale integrated optics. Science, 360(6386), 285–291. https://doi.org/10.1126/science.aar7053
Xu, X., et al. (2020). Photonic inverse design: from fundamentals to applications. Advanced Optics and Photonics, 12(3), 828–887. https://doi.org/10.1364/AOP.381966