Estimated Reading Time: 8 minutes Learn how businesses use Discreet Censorship to manage online dissent on Instagram by identifying harmful contributors, addressing destructive loyalty, and countering manipulative behavior, all while fostering a positive and thriving online community.
The Strategic Role of BIM and LEED Certifications in the European Construction Market
Estimated Reading Time: 5 minutes BIM and LEED enhance efficiency and sustainability in construction, optimizing resources, reducing environmental impact, and supporting net-zero goals.
Startup Marketing Psychology: How Psychological Principles Strengthen Brand Perception
This article explores how psychology-driven marketing strategies can help startups build and strengthen their brand perception. Startups operate under unique conditions—limited resources, high uncertainty, and the critical need to differentiate themselves in crowded or emerging markets. By understanding psychological principles such as social proof, scarcity, identity alignment, and emotional resonance, founders and marketers can craft more effective campaigns and cultivate lasting customer relationships. The discussion covers the importance of positioning and authenticity, as well as the role of storytelling in shaping consumer perception. Case examples illustrate how startups can leverage consumer psychology to gain a foothold in competitive landscapes. The article concludes by emphasizing that responsible marketing—anchored in genuine value propositions and ethical considerations—ultimately drives sustainable growth and fosters brand loyalty.
By Samareh Ghaem Maghami, Cademix Institute of Technology
Table of Contents
Introduction
Startups often face an uphill battle in establishing a foothold in the marketplace. Unlike established corporations, which enjoy significant brand recognition and large budgets, early-stage ventures must deploy strategic thinking and creativity to grab consumer attention. In this environment, psychology becomes a valuable tool. By tapping into the motivations, emotions, and cognitive biases that guide human behavior, startups can create compelling brand stories and offerings that resonate more powerfully with their target audiences.
Modern consumers are increasingly informed and highly attuned to branding efforts. They can easily research competitors, read reviews, and compare features. Consequently, crafting a brand identity that is both genuine and psychologically engaging is not optional; it is a pivotal part of differentiating a product or service from the noise. At the same time, startups must be mindful of ethical considerations. A short-term campaign that exploits fear or misleading claims might drive initial sales, but it can erode trust in the long run. The most successful brands offer real value while understanding—and respecting—the emotional and cognitive drivers of their customers.
Psychology in marketing is not limited to orchestrating emotions or building superficial hype. It involves identifying authentic value and aligning that with the underlying needs and self-perceptions of potential users. From harnessing social proof with early adopters to using storytelling to communicate problem-solving, these techniques can have a profound effect on a startup’s trajectory. This article explores the psychological principles most relevant to entrepreneurial contexts, detailing how they apply to brand perception, product positioning, and long-term success.
Understanding the Psychological Landscape in Startup Marketing
Startups have distinct challenges and advantages compared to established firms. On one hand, limited resources demand more precise, impactful strategies; on the other, their smaller scale makes them more agile, able to quickly adapt marketing messages in response to feedback or market shifts. Recognizing the psychological landscape of potential consumers enables startups to deploy this agility effectively.
Emotional vs. Rational Decision-Making
People often consider themselves rational decision-makers, yet emotional drives regularly trump logic when it comes to making purchases. A convincing brand narrative that resonates emotionally can shape consumer preferences even if the product’s features are similar to those of competing offerings. For startups, this insight highlights the necessity of creating a distinctive brand “feeling” that goes beyond a mere list of features. Emotions like excitement, aspiration, or trust can become major catalysts for early adoption.
Influence of Social Proof
Social proof, the phenomenon where individuals mimic the actions of others in uncertain situations, is particularly potent in the startup ecosystem. Prospective customers frequently look to user reviews, media coverage, or influencer endorsements to gauge trustworthiness. Early adopters who share testimonials or success stories can become powerful advocates, reducing the perceived risk of trying something new. Though generating social proof initially might be challenging—given a lack of existing customer base—tactics like beta programs, referral incentives, and collaborations with credible partners can accelerate trust-building.
Scarcity and Urgency
Scarcity is rooted in the fear of missing out (FOMO), a concept linked to the human survival instinct of securing limited resources. It can push consumers from mere interest to immediate action. However, relying on artificial scarcity—such as presenting items as “limited edition” when they are not—may backfire if discovered. Startups must balance the strategic use of scarcity and urgency with honesty to maintain credibility. For instance, a genuine limited supply or an early-bird discount can be highly motivating for potential customers.
Cognitive Consistency and Brand Cohesion
Cognitive consistency theory suggests that people strive to align their perceptions, attitudes, and behaviors. When a startup communicates a brand identity consistently across every touchpoint, from product packaging to social media interactions, it reduces cognitive dissonance for users. A coherent brand experience signals professionalism and reliability, reinforcing consumer trust. If a startup’s website, app interface, and social media messaging appear disjointed, it may undermine the sense of competence that potential customers look for when deciding whether to invest their time and money.
Innovator Identity and Belonging
In markets driven by innovation, many early adopters see themselves as risk-takers or tech-savvy explorers. Startups can tap into this identity by framing their offerings as avant-garde or community-driven, thus making adopters feel part of something cutting-edge. This sense of belonging is vital because it reinforces the consumer’s decision to try something new, validating their identity as pioneers. Over time, as the startup grows, maintaining this sense of innovation and belonging can differentiate the brand from more traditional players in the market.
Positioning and Differentiation
A startup’s positioning defines how it wishes to be perceived in the marketplace relative to competitors. Effective positioning resonates psychologically with target audiences by directly addressing their needs, aspirations, and pain points. This requires a keen understanding of consumer personas and the context in which they make choices.
Authentic Value Propositions
A value proposition is more than just a list of benefits; it answers the fundamental question, “Why should someone care about this product or service?” A psychologically compelling value proposition underscores how the offering resolves key emotional or functional needs. It might highlight efficiency for time-strapped professionals, or a sense of belonging for niche hobbyists. Authenticity is crucial. If the startup overpromises or misrepresents what it can deliver, disillusionment spreads quickly in our interconnected digital landscape.
Emphasizing Differentiators
With a flood of new ventures entering the market every day, standing out is no small feat. The best approach is often to identify the unique qualities of the startup’s solution and tie them to meaningful benefits. This might involve specialized features, sustainability angles, or a unique brand ethos. However, simply stating “We are different” is insufficient. Marketers must connect that difference to what the target audience genuinely values—offering a clear, psychologically resonant reason for customers to choose one product over another.
Storytelling as a Differentiation Strategy
Stories act as powerful vehicles for emotional connection. When a startup narrates how it was founded—perhaps the founder’s personal struggle with a problem or a passion for making a difference—it humanizes the brand and fosters empathy. Emotional resonance is heightened when the story aligns with the audience’s own experiences or aspirations. Visual storytelling formats, such as short videos or photo-based social media campaigns, can further amplify this connection. The result is that people remember stories and the emotions they evoke more than a simple product pitch.
Perception Shaping Through Symbolism and Design
Branding elements like logos, color schemes, and typography influence psychological perception. Vibrant colors may convey energy and innovation, whereas muted tones might evoke sophistication. Design choices communicate the brand’s personality at a glance. Coupled with carefully chosen language, they can either reinforce the core message or create dissonance. Startups that harmonize visual design with their stated values and mission statements strengthen brand perception, reinforcing a sense of trust and consistency in the minds of consumers.
Nurturing Loyalty from Day One
Differentiating is not just about gaining attention; it is about laying the groundwork for ongoing loyalty. Consistency in messaging, quality service, and evidence of steady product improvements can convert first-time buyers into repeat customers. Loyalty programs or referral incentives can further solidify this relationship by rewarding long-term engagement. The psychological dynamic here is built on reciprocity, where customers feel valued and reciprocate by becoming brand advocates.
Building Emotional Connections with Early Adopters
Securing early adopters is pivotal for startups, as these individuals are not merely customers but also influential advocates who can validate the concept and spread the word. Emotional connection plays a large role in this process, shaping how early adopters perceive and engage with a product. These adopters often identify with the brand’s mission, values, or innovative spark, feeling invested in its success.
The Appeal of Exclusivity and Access
Early adopters frequently relish the chance to be “first” at something, aligning with their self-image as forward-thinking trailblazers. Offering exclusive access—like beta invites, limited-edition product runs, or access to private community groups—can feed this desire for exclusivity. However, the exclusivity must be genuine. If every marketing message claims “exclusive” deals, the term loses its impact and may even alienate audiences who discover they are not receiving anything unique.
Personal Interaction and Feedback Loops
Unlike large corporations, startups can often afford personal interactions with users. Founders might conduct one-on-one onboarding sessions, host small-group demos, or collect direct feedback via social media. This type of engagement fosters a sense of partnership and validation, making customers feel like co-creators rather than passive recipients. The psychological effect is substantial: people who feel listened to are more likely to remain loyal and recommend the brand to their networks.
Social Identity and Community Building
Many early adopters view themselves as part of a broader movement or community, especially if the product resonates with their values or interests. Encouraging user-generated content—like unboxing videos, testimonials, or how-to guides—lets these adopters publicly display their affiliation and helps newcomers gauge the product’s authenticity. A vibrant online community can further strengthen these ties. By regularly showcasing user stories and achievements, startups reinforce the sense that they are all part of something meaningful.
Leveraging Feedback to Improve Products
Early adopters can offer invaluable insights into product strengths and weaknesses. Startups that actively incorporate this feedback into updates and improvements show a commitment to user satisfaction. Public acknowledgments, such as listing top contributors or labeling a feature with a user’s handle, can enhance loyalty by demonstrating genuine appreciation. This psychologically validates users who see their input shaping the product’s evolution, further entrenching their loyalty.
Emotional Anchoring Through Milestones
Celebrating milestones—even modest ones—can foster emotional anchoring among early adopters. Whether it is the startup’s hundredth sale, a successful crowdfunding campaign, or a positive review from a respected publication, involving users in these achievements nurtures a shared sense of accomplishment. This emotional anchoring cements the relationship, making it less transactional and more about collective progress, a powerful dynamic that keeps early adopters engaged and enthusiastic.
Scaling Up: Leveraging Psychological Insights for Sustainable Growth
Once a startup has achieved product-market fit and a solid base of early adopters, the next challenge is scaling. Growth brings new complexities, including reaching broader audiences who may not share the pioneering spirit of the early crowd. The core psychological principles that aided initial traction remain relevant, but they must be adapted to suit the demands of a more diverse, possibly more skeptical user base.
Maintaining Authenticity During Rapid Expansion
Rapid growth can strain brand authenticity if new hires, strategic shifts, or external pressures dilute the startup’s original values and culture. For instance, a company that once championed transparent communication might be tempted to limit details about its supply chain under intense investor scrutiny. This can cause cognitive dissonance in loyal customers who joined for those very values. To mitigate this, successful scaling often involves reinforcing organizational culture, clear internal communication of brand values, and retaining a customer-centric focus in marketing decisions.
Adapting Messaging for Broader Markets
While early messaging might have been highly niche, mass marketing requires broader appeal. This shift poses a psychological challenge: How can a startup maintain the intimacy and exclusivity valued by early adopters while also welcoming new users who may have different motivations? Marketers may employ segmented campaigns, tailoring ads to distinct customer personas. The idea is to preserve specialized messaging for core enthusiasts while offering simplified, universally appealing narratives for newcomers. Ensuring these narratives remain cohesive is key to preventing brand dilution.
The Power of Incremental Trust Signals
Entering new markets or demographics can be facilitated by trust signals that resonate with a broader audience. These might include formal certifications, partnerships with well-known brands, or endorsements from reputable industry publications. Testimonials from diverse customer groups can also alleviate doubts among prospective users who are unfamiliar with the startup’s niche origins. Each trust signal serves as a psychological anchor, reducing perceived risk and building confidence that the product or service can deliver on its promises.
Scaling Customer Relationships
As user numbers grow, maintaining a sense of personal connection may require different approaches. Chatbots, automated email campaigns, and more sophisticated customer relationship management (CRM) tools can extend outreach capabilities. However, automating interactions must be done thoughtfully to avoid an impersonal or mechanized feel. Even small personal touches—like addressing users by name or recalling past interactions—can uphold a sense of care and attentiveness. Striking a balance between automation and genuine engagement is central to retaining psychological closeness with a larger customer base.
Influencer Collaborations at Scale
In the early stages, startups might rely on micro-influencers whose audiences are small yet highly engaged. As growth accelerates, marketing teams may partner with macro-influencers or celebrities to reach broader audiences quickly. The psychological principle remains the same: trust is often transferred from a recognized or admired individual to the product. However, large-scale partnerships carry higher visibility and risk. A celebrity misalignment or negative publicity can quickly backfire. Meticulous vetting and alignment of values minimize this risk, ensuring collaborations feel natural rather than purely transactional.
Creating Continuous Value
To sustain momentum, a startup must consistently demonstrate value beyond the initial product offering. This can involve new features, product line expansions, or value-add content like tutorials, webinars, or exclusive events. Regular innovation keeps the brand fresh in customers’ minds, aligning with the psychological desire for novelty and improvement. By consistently rolling out meaningful updates, startups reaffirm their commitment to solving user problems and exceeding expectations, nurturing a loyal customer base that supports ongoing growth.
Conclusion
Psychology plays an indispensable role in startup marketing, offering a framework for building brand perception that goes beyond surface-level promotion. From understanding emotional drivers and employing social proof to cultivating a sense of belonging among early adopters, these principles help startups stand out and foster deep loyalty in an increasingly crowded marketplace. Authenticity and ethical considerations remain critical, especially as the startup begins to scale and faces the challenge of retaining its initial spirit and values.
By leveraging insights into human behavior, startups can craft compelling narratives, design impactful user experiences, and communicate genuine value. These elements combine to create a resilient brand identity that resonates across multiple demographics and market conditions. Rather than viewing psychology as a manipulative tactic, successful brands treat it as a means of truly aligning with customer motivations. In this way, the fusion of marketing and psychology can lay the groundwork for sustainable, meaningful growth—transforming a fledgling venture into a recognized, trusted name in its industry.
Beyond Entertainment: How Digital Engagement Strategy is Reshaping Business and Thought Leadership
Digital engagement has rapidly transcended its roots in entertainment to become a powerful force reshaping business models, consumer behavior, and the very nature of thought leadership. It is no longer a passive, one-way interaction of content delivered to a passive audience. Rather, digital platforms now empower users to become participants, collaborators, and even co-creators. This dynamic shift has far-reaching implications for businesses, influencers, and institutions across multiple sectors.
Where once engagement was a marker of marketing success or entertainment value, it now serves as an indicator of trust, authority, and social proof. Corporations increasingly recognize that every post, comment, or video triggers a feedback loop that can refine product development, brand identity, and even corporate values. Thought leaders, too, find themselves in a new environment where credibility is not solely dictated by academic credentials or institutional pedigree but by the ability to cultivate and sustain meaningful digital interactions.
In this article, we explore the expanded role of digital engagement—why it matters, how it has evolved from mere entertainment to strategic necessity, and how it shapes the emergence of modern thought leaders. We begin by examining the transition from passive consumption to active participation, highlighting the ways in which audiences now shape and influence content. We then delve into the business ramifications of an engagement-driven world, considering how brands and organizations can harness the power of interactive digital media to drive sales, deepen customer loyalty, and accelerate innovation. Turning to the ascent of digital thought leadership, we analyze the platforms, tactics, and mindsets that amplify an individual’s capacity to steer industry conversations. We also offer a range of strategies for maximizing digital engagement—spanning from interactive content formats and community-building approaches to algorithm-savvy distribution techniques. Finally, we consider what lies on the horizon for digital engagement, pondering the potential effects of new technologies like AI, VR, and decentralized content networks. The article concludes by underscoring the enduring significance of ongoing, authentic interactions in shaping both business success and the next wave of influential voices.
Keyphrases: Digital Engagement Strategy, Thought Leadership in Social Media, Business Influence Online
Table of Contents
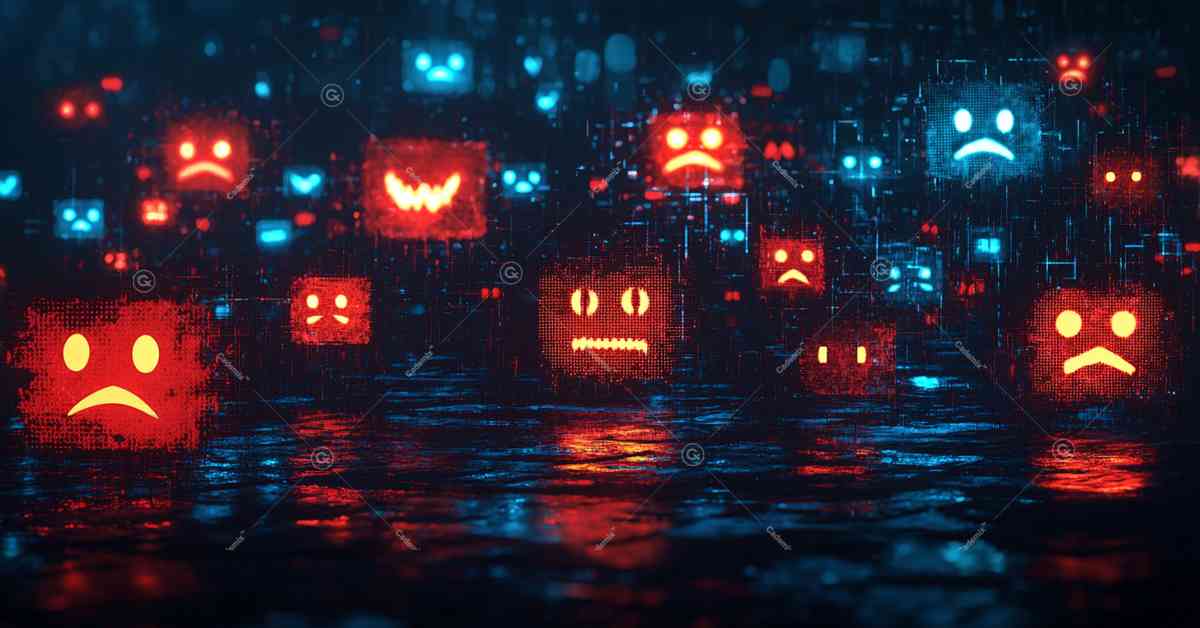
Introduction
Digital engagement has revolutionized the way we communicate, learn, and conduct business. Gone are the days when organizations and professionals could simply broadcast information into the public sphere and hope it stuck. Today, engagement metrics—likes, comments, shares, watch times—serve as real-time indicators of how people respond to, internalize, and act upon content. The magnitude of this shift cannot be overstated: in a saturated media ecosystem, messages that fail to elicit meaningful interaction fade quickly, while highly engaging content can spark movements, define purchasing decisions, and influence entire industries.
Historically, the entertainment sector was the first to recognize engagement as a powerful currency. Social media influencers, YouTube creators, and gaming platforms relied on user feedback, subscriber counts, and community dialogue to refine and expand their offerings. However, as digital platforms grew into ubiquitous forums for everything from political discourse to professional networking, the concept of engagement broadened. It now stretches beyond entertainment into the core of modern commerce, education, and governance.
In the context of business, digital engagement has become a key performance indicator for a broad range of outcomes: brand awareness, customer loyalty, lead generation, and even employee morale. Enterprises spend vast resources optimizing their presence on platforms like LinkedIn, Twitter, YouTube, TikTok, and Instagram, each of which operates on distinct algorithms prioritizing certain types of interactions. This dynamic environment rewards businesses that adapt quickly and penalizes those that cling to static, outdated marketing strategies.
Parallel to corporate interests, public figures and entrepreneurs—aspiring to establish themselves as thought leaders—have discovered how digital engagement can catapult them into the spotlight. Through interactive live streams, crowdsourced research, and real-time debates on social platforms, thought leaders can bypass traditional media gatekeepers, connect with diverse audiences, and influence industry agendas.
Yet with these opportunities come challenges. Audiences are not just viewers but active participants who can readily criticize, shape, or even hijack a brand narrative. Skepticism and short attention spans compound the complexity of capturing and maintaining the public’s interest. Against this backdrop, digital engagement stands out not as a passing trend but as a reconfiguration of how relationships—between brands and consumers, influencers and followers—are formed and sustained. As we navigate the following sections, we will see that digital engagement has transcended the boundaries of entertainment, embedding itself as a core element of strategic success in business and thought leadership.
The Shift from Passive Consumption to Active Participation
From Broadcast to Dialogue
Traditional media formats like television, radio, and newspapers operated on a broadcast model: a small group of creators delivered messages to a large, relatively passive audience. Feedback loops were limited to the occasional letter to the editor, phone-in radio show, or third-party market research. While these forms of engagement offered some avenues for audience input, they were neither immediate nor universally accessible.
Digital platforms, conversely, have upended this dynamic by enabling continuous, real-time interaction. Social networks, blogs, and streaming services allow users to comment, react, and share content in a matter of seconds. The boundaries between producer and consumer blur as amateurs can become content creators themselves, while professional brands are compelled to respond and adapt to user feedback.
Emphasis on User-Generated Content
One significant hallmark of active participation is the explosion of user-generated content (UGC). Enthusiasts unboxing products, fans reviewing a new software update, or customers sharing creative ways to use a tool—these grassroots voices often carry more weight with consumers than polished corporate messaging. Recognizing this influence, brands now actively encourage UGC, running campaigns that invite users to submit photos, videos, or stories for promotional initiatives. By empowering the audience, companies foster a sense of shared ownership, driving deeper loyalty.
UGC’s influence is also evident in knowledge-sharing communities like Reddit or specialized forums, where participants answer questions, troubleshoot problems, and collectively refine community knowledge bases. For businesses, these organically formed micro-communities can offer invaluable market insights while simultaneously providing free, peer-to-peer customer support.
Interactive Experiences
Beyond text-based comments and reviews, active participation now includes a wide spectrum of interactive experiences. Live-streamed events on YouTube, Twitch, or LinkedIn often feature Q&A sessions where hosts field audience questions in real time. Virtual conferences and webinars incorporate polls, breakout rooms, and interactive whiteboards, transforming online gatherings from passive lectures into collaborative experiences. In the realm of e-commerce, features like shoppable livestreams or augmented reality (AR) try-ons let consumers engage with products in novel ways before making a purchase.
Such high levels of interactivity spark new forms of creativity and revenue generation. Brands partner with key influencers to host live product demos; educational institutions run virtual classes enriched by real-time conversation threads; activists coordinate global events with an immediacy that was once unimaginable.
Challenges of Active Participation
While empowering, this epoch of active participation also introduces complexities. The speed at which content circulates can quickly escalate minor issues into viral public relations crises. Businesses must be prepared to respond promptly and transparently to user feedback, positive or negative. Failure to do so risks a blow to credibility and goodwill.
Moreover, the democratization of content creation can lead to misinformation or brand identity dilution. Users who misunderstand or misrepresent a product can mislead others, requiring brand custodians to undertake a delicate balancing act—correcting inaccuracies without appearing overly controlling. Astroturfing campaigns and troll farms can fabricate community sentiment, further complicating the perceived authenticity of online engagement.
Ultimately, the shift from passive consumption to active participation has moved digital engagement to the forefront of strategic planning. Those who thrive in this environment recognize that an engaged user base not only drives views or sales but also shapes the brand’s narrative and fosters ongoing innovation.
The Business Impact of Digital Engagement
Brand Trust and Authority
In an increasingly crowded marketplace, trust is both elusive and essential. Engaged audiences can significantly bolster a brand’s credibility. When consumers interact positively with a brand—through supportive comments, reviews, or shares—they offer social proof that resonates more powerfully than any top-down advertising campaign. Indeed, platforms like G2, Capterra, and Yelp have become critical channels where peer reviews carry substantial weight in purchasing decisions.
Active, two-way communication plays a crucial role in establishing this trust. Brands that openly address questions and concerns demonstrate accountability, a quality that resonates deeply in an era of heightened skepticism. Regularly publishing transparent, behind-the-scenes content or prompt explanations in response to product issues can transform challenges into opportunities for rapport-building.
Sales and Conversions
Digital engagement also has a direct impact on revenue generation. The correlation is simple but powerful: an audience that engages more frequently with a brand is statistically more likely to convert, whether that means buying a product, subscribing to a service, or recommending a company to peers. Email click-through rates, webinar attendance, and average watch time on brand videos all function as leading indicators of potential sales.
E-commerce sites leverage interactive elements—like real-time chatbots or integrated social proof—and see tangible results in the form of higher conversion rates. Interactive product demonstrations or AR-based previews further reduce skepticism, encouraging confident purchasing decisions. Influencer partnerships add yet another layer: an influencer’s engaged following, built on trust and relatability, often translates into higher-quality leads and sustained sales.
Customer Retention and Loyalty
Retaining existing customers typically requires fewer resources than acquiring new ones, making loyalty a prized metric. Persistent engagement keeps a brand top-of-mind, reminding customers of the value and relevance the brand provides. Loyalty programs that encourage ongoing interaction—point systems, tiered rewards, exclusive community forums—are proven to reduce churn and increase customer lifetime value.
Moreover, an actively engaged customer base often evolves into a community. In these environments, customers feel an emotional connection, forging relationships with both the brand and each other. Such communities can become self-sustaining networks for mutual support, troubleshooting, and shared enthusiasm. The net result is not just higher retention but also a powerful word-of-mouth engine that lowers marketing costs.
Innovation Through Feedback Loops
One of the most underappreciated benefits of strong digital engagement is its capacity to fuel innovation. Through direct interactions—comment sections, surveys, user testing, or forum discussions—companies can gather near-instantaneous feedback on new features, product lines, or marketing approaches. This continuous dialogue helps identify pain points, refine functionality, and even spark entirely new ideas that might not emerge from in-house brainstorming alone.
Agile companies integrate digital feedback loops at every stage of the product lifecycle. Some even invite select customers to beta test offerings, creating a sense of co-ownership. The result: quicker iteration, reduced misalignment with market demands, and a deeper understanding of customer desires. Meanwhile, customers appreciate that their voices contribute to shaping the products or services they use, forging lasting loyalty.
Pitfalls and Risk Management
Despite the advantages, the high visibility of digitally engaged brands introduces reputational risks. Missteps—such as insensitive content, mishandled criticism, or data breaches—are amplified through viral sharing, rapidly escalating potential damage. Crisis management now unfolds in real time; a slow or evasive response can irreparably harm public opinion.
Moreover, unscrupulous competitors or malicious entities can exploit engagement channels to spread disinformation or stage coordinated harassment. Consequently, businesses must invest in robust moderation protocols and community guidelines to safeguard the integrity of their digital environments.
Overall, digital engagement wields transformative power over how businesses grow and sustain themselves. Through brand trust, direct conversions, customer loyalty, and innovation, meaningful interactions become the cornerstone of competitive advantage in the digital era.
The Rise of Thought Leadership in Digital Spaces
Democratization of Expertise
In previous decades, earning the status of a “thought leader” typically involved ascending hierarchical career ladders, publishing in academic journals, or obtaining coverage in prestigious media outlets. While these pathways remain relevant, social media and other digital platforms have lowered entry barriers. Individuals with fresh insights, compelling content, and the ability to spark meaningful engagement can quickly rise to prominence, regardless of traditional credentials.
This democratization of expertise allows independent consultants, start-up founders, and passionate enthusiasts to influence discussions alongside established experts. By consistently sharing high-quality, insightful posts or videos, newcomers can cultivate significant followings. In turn, these followings can propel them into speaking engagements, book deals, or brand collaborations, effectively launching them into recognized thought leadership roles.
Authentic Engagement as a Credibility Metric
In the digital realm, engagement metrics function as powerful proxies for influence. A high number of likes or shares can indicate resonance, but thoughtful comments and extended discussions signify deeper impact. Thought leaders who only broadcast information without engaging in dialogue risk being perceived as out of touch. By contrast, those who respond to comments, solicit feedback, and adapt their perspectives based on community input gain a reputation for authenticity and adaptability.
Platforms like LinkedIn, YouTube, and Twitter serve as primary arenas for professional thought leadership. Long-form articles, how-to videos, live stream debates—each format invites a specific kind of audience participation. Thought leaders who master platform-specific engagement strategies stand out, as they grasp not only the type of content that flourishes on each platform but also the tone, pacing, and format that best resonate with their target audience.
Building a Personal Brand
Digital thought leadership and personal branding go hand-in-hand. A compelling personal brand clarifies the topics, values, and expertise that define a thought leader, ensuring consistency across multiple platforms. Visual elements—like a logo, color palette, or style of cover image—help establish recognition. But the real differentiator is the tone and substance of content.
Leading voices often craft a distinct narrative that resonates with a particular niche. For instance, a tech entrepreneur might focus on ethical AI, blending personal anecdotes about founding a startup with industry insights on machine learning regulation. A public health expert could blend academic credentials with relatable stories of on-the-ground patient care. The personal brand emerges as a unifying thread, tying together content in a cohesive, meaningful way that audiences learn to trust.
The Role of Consistency
Consistency is critical for sustaining an audience’s engagement and trust. Thought leaders who periodically vanish from their platforms risk losing momentum, while those posting erratically may confuse followers. Conversely, regularly published content—be it weekly blog posts, monthly webinars, or daily short-form videos—builds anticipation and loyalty.
However, consistency does not imply rigidity. Thought leaders need to remain agile, responding to relevant news stories, emerging technologies, or shifting social sentiments. Balancing consistency with timeliness allows thought leaders to remain authoritative yet adaptable, meeting audience needs without sacrificing the coherence of their personal brand.
Challenges and Critics
Of course, rapid ascendancy to digital thought leadership has its pitfalls. Skepticism can arise if an individual appears to oversimplify complex topics or if they wield inflated credentials. Additionally, an echo chamber effect may occur when leaders cultivate an audience that uncritically agrees with every statement, limiting constructive debate and critical feedback.
Moreover, the public’s growing sensitivity to “performative” social media behavior means that grandstanding or insincere messaging can quickly backfire. Authentic thought leadership must be earned through consistent, genuine interactions rather than hollow posturing. The capacity to engage in dialogue, to admit mistakes, and to refine perspectives remains crucial for maintaining long-term influence.
Despite these risks, the heightened accessibility of thought leadership signifies a major cultural shift. The internet is now an expansive forum for the exchange of ideas, governed less by editorial gatekeepers and more by the tastes and judgments of engaged communities. Harnessed effectively, digital platforms can catapult dedicated individuals into impactful leadership roles that shape industries, policies, and collective mindsets.
Strategies for Maximizing Digital Engagement
1. Prioritize Interactive Content
Static, one-way content often fails to spark sustained attention. Instead, leveraging interactive elements can transform a post or video into a conversation starter:
- Polls and Surveys: Ideal for platforms like LinkedIn or Twitter, polls invite quick participation while gathering valuable audience insights.
- Live Q&A Sessions: Hosting real-time events on YouTube, Twitch, or Clubhouse encourages viewers to pose direct questions and clarifications.
- Interactive Infographics: Visually appealing graphics that allow users to click on data points or hover for extra context can deepen engagement.
Interactive content not only piques curiosity but also grants audiences a sense of collaboration and investment in the discussion. This sense of ownership motivates people to revisit and share the content, extending its reach.
2. Foster Community-Building
Building a community around a brand or idea is one of the most effective ways to drive ongoing engagement. Communities can take many forms:
- Private Groups: Whether hosted on Facebook, Slack, Discord, or LinkedIn, private groups create a sense of exclusivity, encouraging members to open up and share.
- Membership-Based Platforms: Subscription models on Patreon or Substack reward loyal followers with premium content while generating recurring revenue.
- Offline Extensions: Bringing the community together at conferences or meet-ups can bolster the sense of belonging cultivated online.
A successful community thrives on shared goals, mutual respect, and clear guidelines. Moderation is essential to maintain constructive dialogue, while regular content—such as weekly discussion prompts or expert AMA (“Ask Me Anything”) sessions—keeps energy levels high.
3. Adapt to Platform-Specific Algorithms
Each social media platform employs unique algorithms that rank content. Understanding these algorithms is key to boosting visibility:
- LinkedIn: Rewards professional conversations. Posts that spark extended comment threads tend to rank higher.
- Twitter: Favors real-time updates and hashtag-driven discovery. Timing posts to coincide with peak traffic can significantly improve reach.
- Instagram: Visual storytelling is paramount; reels and stories often outperform static posts, especially when they leverage trending audio or filters.
- TikTok: Emphasizes short-form, fast-paced videos with high retention rates. Creative hooks in the first few seconds can make or break a post’s performance.
Staying informed about algorithm changes—and iterating content strategies accordingly—enables continued relevance. Simple tactics, like using the right hashtags or posting at strategic times, can yield outsized engagement gains.
4. Encourage User-Generated Content
User-generated content humanizes a brand and fosters communal ties. UGC can include:
- Customer Testimonials: Inviting buyers to share their success stories with a product or service.
- Creative Campaigns: Contests or hashtag challenges that ask followers to interpret a brand message or share personal anecdotes.
- Collaborative Projects: Co-creating eBooks, webinars, or research with volunteers from the audience.
Beyond building rapport, UGC often has higher credibility among peers. When people see content from others who resemble them—rather than polished corporate ads—it resonates more deeply. This authenticity can trigger a cycle of further engagement, with new audiences discovering the brand through community-driven posts.
5. Leverage AI and Data Analytics
Data-driven insights are invaluable for refining engagement tactics. AI-powered platforms can reveal:
- Optimal Posting Times: Identifying when a specific audience is most active online.
- Sentiment Analysis: Gauging overall reactions to a campaign or piece of content, allowing for timely pivots if sentiment is negative.
- Content Topic Recommendations: Highlighting trending keywords or topical gaps where a brand can stand out.
Some advanced tools even offer predictive analytics, anticipating the type of content that might perform best with a given audience segment. Integrating these insights enables marketers and thought leaders to continually experiment, measure outcomes, and refine their strategies.
6. Maintain Authentic Interactions
In an environment saturated with automated messages and curated personas, genuine human interaction cuts through the noise. Thought leaders who respond personally to comments, or brands that acknowledge user feedback with empathy and clarity, are more likely to cultivate loyal supporters. Authenticity cannot be faked long-term; over time, insincerity or neglect become evident, damaging credibility.
This emphasis on authenticity extends to acknowledging mistakes. Whether it’s a delayed product release or an oversight in an article, transparency in taking responsibility can turn a potential crisis into a moment of positive engagement. People generally respect openness more than the appearance of flawless perfection.
The Future of Digital Engagement Strategy
Technological Innovations
The next frontier of digital engagement is being shaped by emerging technologies that promise increasingly immersive experiences:
- Virtual Reality (VR) and Augmented Reality (AR): These tools elevate audience interaction from two-dimensional screens to immersive, interactive environments. VR conferences, 3D product demonstrations, and AR overlays in physical retail spaces have the potential to revolutionize how consumers engage with brands.
- Artificial Intelligence (AI) and Machine Learning: Beyond analytics, advanced AI-driven chatbots can offer near-human conversational experiences. AI-generated content—such as dynamically personalized videos or interactive storylines—may blur the line between content creator and consumer.
- Voice Interfaces: As more households adopt smart speakers and voice assistants, voice-activated engagement will become a new channel for brand interaction, content dissemination, and community-building.
Although these innovations hold promise, they also introduce new challenges. Data privacy concerns, potential biases in AI algorithms, and the digital divide all demand ethical, user-centric solutions.
Decentralized Platforms and Web3
Another major shift looms in the rise of decentralized platforms and Web3 technologies. Blockchain-based social networks, peer-to-peer content distribution systems, and cryptocurrency reward models could reshape engagement dynamics by giving users direct ownership stakes or tokens within communities. In such ecosystems, content creators and participants might benefit financially from the engagement they generate, potentially redistributing how value is captured.
However, the decentralized model is not without obstacles. Regulatory uncertainty, technical barriers, and market volatility can hinder mass adoption. Additionally, establishing trust and consistency in decentralized communities poses a unique challenge, particularly as content moderation becomes more fragmented.
Evolving User Expectations
As the digital environment grows more sophisticated, so do audience expectations. Tomorrow’s consumers will likely demand:
- Immediate, Personalized Responses: Patience for standardized or delayed customer service may wane as AI bots improve.
- Inclusive and Ethical Engagement: Audiences increasingly scrutinize brands on social justice, sustainability, and diversity. Engagement efforts that appear opportunistic or lack sincerity risk backlash.
- Multi-Platform Consistency: While each platform has its own tone, values, and user base, audiences expect brand messages to remain coherent across channels.
Meeting these evolving standards will require agility, as well as continued investment in both technology and the human capital needed to manage complex engagement strategies.
Continuous Evolution of Metrics
Metrics measuring digital engagement will also become more nuanced. Basic counts of likes and shares, while still relevant, may not fully capture the depth and quality of interactions. Future analytics could integrate:
- Dwell Time: How long someone spends consuming or interacting with a piece of content.
- Quality of Comments: Distinguishing between generic praise versus thoughtful, constructive dialogue.
- Cross-Platform Influence: Mapping audience journeys across multiple social channels and digital touchpoints.
By refining these metrics, businesses and thought leaders can gain a more accurate understanding of their impact and refine their strategies accordingly.
Conclusion
Digital engagement has transcended its early association with entertainment to become the bedrock of modern business strategy and thought leadership. It represents a sea change, moving from passive consumption to a model where individuals actively shape brand narratives, co-create content, and hold significant sway over reputations. This interconnected ecosystem fosters communal ties, places authenticity at a premium, and demands rapid adaptation from anyone seeking to remain relevant.
The business implications are profound. An engaged community can propel a company’s growth through organic advocacy, continual feedback loops, and sustained loyalty. Meanwhile, for professionals and public figures aspiring to lead conversations, consistent and genuine engagement cultivates credibility that increasingly overshadows traditional credentials. Thought leaders who master the art of digital interaction find themselves at the helm of industry-shifting dialogues, influencing not only products and services but also the broader societal landscape.
Looking ahead, developments in AI, AR, VR, and decentralized platforms will further expand the scope and complexity of digital engagement. These emerging technologies promise an era of hyper-personalization and immersive experiences, yet they also demand conscientious design and ethical conduct. Moreover, audiences will continue to raise their expectations, rewarding those who demonstrate transparency, inclusivity, and genuine care.
In this context, digital engagement is not a one-time campaign or an accessory to a marketing plan. Rather, it is a continuous process of conversation, co-creation, and community-building. Its influence permeates how businesses innovate, how thought leaders gain and maintain relevance, and how global communities converge around shared passions. To overlook its power is to be relegated to obscurity in a marketplace defined by active participation. Conversely, those who recognize engagement as more than just a metric—indeed, as the central currency of online influence—stand poised to shape the future of industry, culture, and collective thought.
Step-by-Step Guide to Programming an Intelligent Conveyor Belt Control System with TIA Portal
This article presents a step-by-step guide to programming an intelligent conveyor belt control system using TIA Portal, Siemens’ comprehensive engineering software for PLC programming and industrial automation. This project, tailored for applications in manufacturing and material handling, demonstrates key concepts in PLC programming, such as variable speed control, object detection, and automated stopping, providing a practical introduction to industrial automation. The system integrates an intuitive Human-Machine Interface (HMI) to allow operators seamless control over conveyor functions, real-time monitoring, and safety management. Additionally, we explore advanced features like predictive maintenance and fault handling to enhance operational reliability.
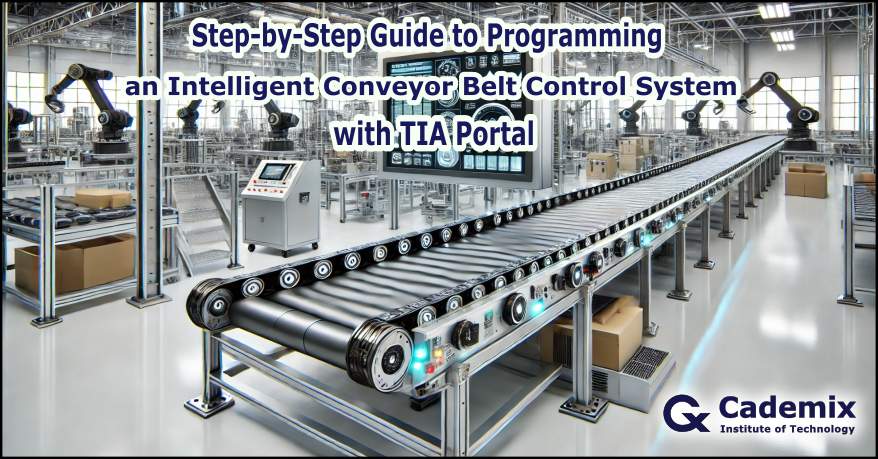
1. Introduction to TIA Portal and Its Industrial Applications
Overview of TIA Portal
TIA Portal (Totally Integrated Automation Portal) is a powerful, integrated engineering software developed by Siemens, widely used in industrial automation. It serves as a unified environment where engineers can design, program, simulate, and monitor systems across an entire industrial process. With TIA Portal, various automation tasks can be handled within a single platform, making it highly efficient for engineers.
A significant aspect of TIA Portal is its compatibility with Programmable Logic Controllers (PLCs) and Human-Machine Interfaces (HMIs). PLCs, often considered the “brains” of an automated system, are programmable devices used to control machinery and processes. HMIs, on the other hand, are interfaces that allow operators to interact with machines, providing control, data visualization, and system feedback. By integrating both PLC and HMI programming into one software, TIA Portal makes it easier for engineers to create, test, and implement control logic and user interfaces. This seamless integration has made TIA Portal one of the most popular tools for industrial automation engineers.
TIA Portal’s ability to streamline engineering workflows has led to its widespread adoption across industries. The software allows engineers to create flexible and scalable solutions, regardless of the project’s complexity, making it a top choice for designing modern automated systems.
Importance in Modern Industry
In today’s manufacturing landscape, there’s a strong emphasis on automation. Industries such as automotive, pharmaceuticals, food and beverage, and logistics rely heavily on automation to increase efficiency, reduce costs, and enhance safety. The demand for advanced, reliable control systems continues to grow as companies look to automate more processes.
TIA Portal plays a crucial role in meeting this demand. By enabling engineers to design highly integrated systems, TIA Portal allows companies to improve production accuracy, minimize downtime, and maximize productivity. The software supports the development of complex systems that can handle tasks autonomously, making it ideal for industries seeking to stay competitive and meet high production standards.
Automation also contributes to better product quality and consistency. With TIA Portal, engineers can set precise control parameters, reducing human error and ensuring consistent output. The ability to simulate and monitor systems within TIA Portal also enables predictive maintenance, helping companies prevent equipment failure before it impacts production.
As a result, TIA Portal has become invaluable for industries moving towards smart factories and Industry 4.0, where interconnected, data-driven systems work together to optimize production processes.
Project Overview
This article focuses on a specific application of TIA Portal: programming an intelligent conveyor belt control system. Conveyor belts are essential in industries such as manufacturing, warehousing, and logistics, where they move materials and products along a controlled path. Traditional conveyor belts typically operate at fixed speeds and do not have the capability to respond dynamically to objects or obstacles in their path.
The project presented in this guide goes beyond basic conveyor control. Using TIA Portal, we’ll design a conveyor belt system with advanced features, including:
- Variable Speed Control: Adjusting the conveyor’s speed based on conditions or requirements.
- Object Detection: Using sensors to detect objects on the conveyor, allowing for actions like automated stopping or starting.
- Automated Stopping: Implementing safety features that stop the conveyor if an object is detected, preventing damage or accidents.
These features make the conveyor system smarter and more adaptable, ideal for handling different materials, adjusting to varying workloads, and ensuring safety in the workplace.
By demonstrating the development of this intelligent conveyor belt system, this article aims to provide readers with a practical introduction to TIA Portal’s capabilities, illustrating its application in real-world industrial settings. Through this project, readers will gain insights into how TIA Portal can be used to create automated systems that are efficient, reliable, and customizable, showcasing the skills and expertise required in today’s automated industry.
2. Project Requirements and Objectives
System Specifications
To create an intelligent conveyor belt system, several essential requirements must be met to ensure functionality, efficiency, and safety. The main specifications for this project include:
- Speed Adjustment: The conveyor belt should be capable of variable speed control. This flexibility allows operators to adjust the speed based on production needs, improving efficiency and accommodating different material types and processing times.
- Object Detection: The system needs to detect objects on the conveyor. Sensors placed along the conveyor will identify when an item is present. This detection enables advanced actions, such as triggering an automatic stop to prevent collisions or slowdowns based on detected load.
- Automatic Stopping: Safety is a key concern in industrial automation, so this project includes an automatic stopping mechanism. When the sensors detect an obstacle or an overload, the conveyor should stop automatically. This feature prevents potential accidents and minimizes wear on the equipment.
- Operator Control: An intuitive interface is essential to make the system user-friendly. Operators should be able to control speed, start and stop the conveyor, and monitor sensor statuses easily. This control will be provided through a Human-Machine Interface (HMI) designed to be clear and straightforward for users.
These specifications create a flexible and reliable conveyor belt system that can handle different materials efficiently, ensure safety, and allow for easy operator interaction.
Hardware Components
To implement the intelligent conveyor system, specific hardware components are required, each compatible with Siemens’ TIA Portal to enable seamless integration. Below are the primary components:
- Programmable Logic Controller (PLC): The PLC serves as the core control unit for the conveyor belt system. It executes the control logic programmed in TIA Portal, handling tasks such as speed adjustment and response to sensor inputs. Siemens PLCs are recommended for compatibility with TIA Portal, offering flexibility, reliability, and scalability for this project.
- Sensors: Sensors play a crucial role in detecting objects on the conveyor. For this project, proximity sensors or photoelectric sensors are ideal, as they can quickly detect objects without physical contact. The sensors provide feedback to the PLC, allowing it to make real-time decisions, like stopping the conveyor when an object is detected.
- Motors: The motor is responsible for driving the conveyor belt. A variable frequency drive (VFD) motor is preferred in this case, as it supports variable speed control, allowing the PLC to adjust the conveyor speed based on requirements. This motor setup also ensures smoother operation, reducing mechanical stress and extending the system’s lifespan.
- Human-Machine Interface (HMI): An HMI panel provides the user interface, enabling operators to monitor and control the conveyor system. Siemens HMI panels, compatible with TIA Portal, are suitable for this project. Through the HMI, operators can view sensor statuses, control conveyor speed, and stop or start the conveyor. The HMI interface is programmed to be intuitive, providing easy access to all necessary controls and information.
These components work together to create a fully integrated conveyor system, with the PLC acting as the brain, sensors providing feedback, motors driving the system, and the HMI serving as the user interaction point.
Objectives of the Project
The primary objective of this project is to design a smart, user-friendly conveyor belt system that meets modern industrial requirements. The goals of this project are:
- Reliability: The system should operate with minimal downtime. Through real-time monitoring and responsive controls, the conveyor system will run efficiently, ensuring production continuity and reducing the chance of breakdowns.
- Flexibility and Control: By integrating variable speed control and automated stopping, the conveyor can adapt to different operational conditions. This flexibility increases productivity by allowing operators to fine-tune the system according to specific needs.
- User-Friendly Interface: The HMI should be simple and intuitive, allowing operators with various skill levels to control and monitor the system. The interface should display all essential information, such as speed settings and sensor statuses, in an easily accessible format.
- Safety Features: Safety is paramount in industrial environments. The system’s automatic stopping mechanism, activated by sensors detecting obstacles, ensures that the conveyor can stop immediately to prevent accidents. This feature helps protect both equipment and personnel.
- Scalability and Compatibility with Future Enhancements: The system is designed to be scalable, allowing for additional features like predictive maintenance, remote monitoring, or expanded sensor coverage. TIA Portal’s integration makes it straightforward to add new functions or devices as requirements evolve.
By achieving these objectives, this project aims to showcase a high level of technical competence in using TIA Portal for industrial automation, while demonstrating an understanding of practical requirements in real-world applications. This intelligent conveyor system project not only illustrates essential skills in PLC programming and HMI design but also aligns with the demands of industries focused on automation, efficiency, and safety.
3. Setting Up the Development Environment
In this section, we’ll walk through setting up the development environment in TIA Portal for the intelligent conveyor belt control system. This setup process includes installing TIA Portal, initializing the project, and configuring the PLC with the necessary components for our application. This guide is structured to be accessible for both beginners and experienced users, providing a solid foundation for developing and managing automated systems within TIA Portal.
Installation and Configuration of TIA Portal
To start developing in TIA Portal, the first step is installing the software. TIA Portal is compatible with Windows, and Siemens provides a comprehensive installation package that includes the necessary PLC and HMI programming tools.
- Downloading TIA Portal: Visit the Siemens website to download the TIA Portal installation package. Make sure to select the correct version for your project, as each version has its specific hardware compatibility. For this project, TIA Portal V16 or higher is recommended, as it offers enhanced features and improved performance for industrial applications.
- Running the Installer: Once downloaded, run the installer. The installation process will prompt you to select the components you need. At a minimum, install the following:
- STEP 7: This component enables PLC programming.
- WinCC: Required for HMI design and visualization.
- StartDrive: For motor and drive configuration (if applicable to your hardware).
- Activating Licenses: TIA Portal requires licenses to access full functionality. You can activate the licenses either via a USB license dongle provided by Siemens or through an online activation. Ensure that all licenses are activated before proceeding.
- Launching TIA Portal: After installation, open TIA Portal. The software will display a startup screen with options to create a new project, open an existing project, or explore example projects.
Project Initialization
With TIA Portal successfully installed, the next step is to create and configure a new project. This setup will define the core environment for developing the intelligent conveyor belt system.
- Creating a New Project: From the startup screen, select “Create new project.” A dialog box will appear, prompting you to enter a project name, author information, and location. For easy organization, name the project something descriptive, like “Intelligent Conveyor Belt Control.”
- Selecting the Hardware Model: After creating the project, TIA Portal will ask you to select the hardware components used in your setup. To add the main PLC, select “Add device,” then choose the PLC model. For this project, a Siemens S7-1200 or S7-1500 is recommended due to their compatibility and processing power.
- Configuring Project Settings: Once the PLC is added, TIA Portal will display a project view with options for programming and configuration. In the project settings, configure parameters such as:
- IP Address: Assign a unique IP address to the PLC to enable network communication.
- Cycle Time: Set the cycle time for the PLC based on project needs. For conveyor control, a fast cycle time is recommended to ensure timely responses.
- Memory Allocation: Define memory resources according to the complexity of your control logic.
Setting up the project ensures that TIA Portal recognizes the PLC and any connected devices, providing a structured environment for further development.
PLC Configuration
The next stage in the setup process is configuring the PLC to communicate with the sensors, motors, and HMI. This configuration is essential for integrating each hardware component and enabling them to work together within the conveyor belt system.
- Connecting Sensors: To integrate sensors with the PLC, navigate to the “Devices & Networks” section in TIA Portal. Here, you can add sensors as I/O devices, specifying their connection type (digital or analog) and addresses. For this project:
- Proximity Sensors: Connect these to digital input terminals, configuring them to detect object presence.
- Photoelectric Sensors: Similarly, connect photoelectric sensors to detect obstacles, assigning unique addresses for easy reference in the control logic.
- Configuring Motors and Drives: The motor, responsible for moving the conveyor, must be configured to allow speed adjustments. If using a Variable Frequency Drive (VFD), add the drive to the project. In the “Hardware Catalog” section, locate the VFD model and configure parameters such as:
- Speed Control: Set the drive to accept commands from the PLC, enabling variable speed control based on the PLC’s logic.
- Safety Stop: Configure an input dedicated to emergency stop functions, allowing the PLC to halt the conveyor in case of a fault or obstacle detection.
- HMI Integration: The HMI provides a user-friendly interface for operators. In TIA Portal, go to “Add device” and select an HMI model compatible with your project, such as a Siemens Basic Panel or Comfort Panel. Once added:
- Define Control Elements: Create interface elements like start, stop, and speed adjustment buttons.
- Status Display: Configure data blocks to display real-time data, like conveyor speed and sensor status, providing visual feedback for operators.
- Network Communication: For the PLC, sensors, drives, and HMI to communicate effectively, set up the network configuration within TIA Portal. Use the “Devices & Networks” screen to create a connection between all devices. Ensure each component has a unique IP address to prevent conflicts. Verify that the communication protocol (e.g., PROFINET or EtherNet/IP) is supported by all connected devices.
- Testing Connectivity: Before finalizing the setup, test the connections between the PLC and each device. TIA Portal provides diagnostic tools for checking signal status and data flow. Run a quick connectivity test to confirm that all devices are responding as expected.
Setting up the development environment in TIA Portal is a vital step in creating a functional, reliable conveyor control system. By following this setup process, you ensure that all hardware components are correctly recognized and configured, establishing a solid foundation for developing, testing, and deploying the intelligent conveyor belt system. This structured setup allows for easy adjustments and debugging, streamlining the development process and enhancing the overall effectiveness of the control system.
4. Programming the Conveyor Belt Control Logic
This section covers the essential programming steps needed to control the intelligent conveyor belt system in TIA Portal. We’ll start with the basic programming concepts for PLCs, then dive into the specific control logic, such as speed control, object detection, and fault handling. Each step is designed to be clear and actionable, helping both beginners and experienced engineers create a reliable, automated conveyor system.
Basic PLC Programming Concepts
Programming a PLC involves using specialized logic structures, and TIA Portal offers several programming languages, the most common of which are Ladder Logic and Function Blocks. Here’s a quick overview of each:
- Ladder Logic (LAD): This is a graphical programming language resembling electrical relay logic, which makes it accessible to those familiar with traditional electrical circuits. Ladder logic is composed of “rungs,” each representing a set of conditions and actions. It’s ideal for simple on/off controls and is commonly used in conveyor belt applications.
- Function Block Diagram (FBD): Function Blocks are another visual language in TIA Portal, allowing for more complex functions to be grouped and reused. FBD is ideal for programming repetitive control sequences, such as those in conveyor belt speed and sensor-based controls.
For this project, we’ll primarily use ladder logic due to its simplicity and suitability for the control requirements. However, function blocks may be used for reusable modules, such as the speed control function.
Implementing Speed Control
Variable speed control allows the conveyor to adjust based on operational needs, improving efficiency and flexibility. In this section, we’ll set up the control logic to increase or decrease the conveyor’s speed based on specific triggers.
- Defining Speed Variables: Begin by creating variables for speed levels (e.g., Low, Medium, and High) within TIA Portal. These variables will allow you to adjust the conveyor speed as required. Use integer data types to define each speed level, assigning values that correspond to the motor’s speed control settings.
- Programming Speed Control Logic:
- Ladder Logic for Speed Levels: In the ladder editor, create rungs for each speed level. For instance, the first rung can represent Low Speed, the second rung for Medium Speed, and the third for High Speed.
- Condition-Based Triggers: Each speed level should activate based on specific conditions. For example, set a low speed when the conveyor is empty or has light loads, medium speed for standard operation, and high speed when there’s a heavy workload.
- Timers for Smooth Transitions: Use timers to gradually increase or decrease speed, preventing sudden jerks that can damage the conveyor system.
- Linking to HMI Controls: To give operators control over speed, create buttons or a slider on the HMI. Link these controls to the speed variables so that operators can adjust the speed directly through the HMI interface.
This speed control logic makes the system adaptable to different loading conditions, improving overall efficiency.
Object Detection and Stop/Go Logic
Object detection is essential to prevent collisions and ensure safe operation. Using sensors, we can detect items on the conveyor and automatically stop or resume the belt as needed.
- Configuring Sensors in TIA Portal: Ensure that sensors are connected to the PLC’s digital input ports. Configure these inputs in TIA Portal, assigning each sensor a unique address for easy identification.
- Programming Object Detection Logic:
- Ladder Logic for Sensor Feedback: Create a rung in ladder logic that checks the status of each sensor. If a sensor detects an object (indicating an obstacle), the PLC should trigger the conveyor’s stop function.
- Stop/Go Logic: Set up two branches in the ladder logic: one for “Stop” when an obstacle is detected and another for “Go” when the path is clear. When a sensor is activated, the PLC interrupts the motor’s operation, stopping the conveyor. When the sensor clears, the PLC resumes operation.
- HMI Feedback: Provide visual feedback on the HMI to inform operators of any obstacles detected. This feedback can be in the form of a warning icon or message on the HMI display, enabling quick identification of any blockage.
This object detection and stop/go logic ensures the conveyor operates safely and prevents potential damage to both materials and equipment.
Fault Handling and Safety
Safety is a top priority in industrial automation. This project includes fault handling and emergency stop features to ensure a robust, compliant system.
- Emergency Stop Logic:
- Dedicated Emergency Stop Input: Assign a digital input on the PLC to an emergency stop button, which operators can use to halt the system in case of danger.
- Emergency Stop Rung in Ladder Logic: Create a rung that triggers an immediate stop when the emergency input is activated. Ensure that this rung has the highest priority so that the conveyor halts regardless of other conditions.
- Fault Detection Logic:
- Detecting Common Faults: Program the PLC to detect common faults, such as motor overloads or sensor malfunctions. For example, you can use a current sensor to detect if the motor is drawing excess power, indicating an overload.
- Fault Diagnosis: When a fault is detected, the PLC should stop the conveyor and display a diagnostic message on the HMI. Create a rung that links each fault condition to specific error codes or messages.
- HMI Safety Alerts: For each safety event, such as an emergency stop or fault, display an alert on the HMI. Operators should be able to see clear, actionable messages guiding them on how to resolve the issue or reset the system.
These safety measures make the conveyor belt system compliant with industry standards, ensuring protection for both personnel and equipment.
This control logic setup provides a comprehensive solution for managing conveyor belt speed, object detection, and fault handling, creating a reliable, intelligent system that enhances safety and efficiency. The use of TIA Portal’s ladder logic and HMI integration ensures that this setup is both effective and easy for operators to understand and control. By following these programming steps, you’ll develop a robust control system that can adapt to various industrial applications.
5. HMI Design for User Interaction
A well-designed Human-Machine Interface (HMI) is essential for allowing operators to interact with the conveyor system efficiently and safely. In this section, we’ll cover how to create a user-friendly HMI in TIA Portal, display real-time data, and integrate safety features to enhance system usability.
Creating a User-Friendly HMI
In TIA Portal, HMI screens can be customized to provide operators with intuitive controls and easy-to-read displays. The goal is to make it simple for operators to manage the conveyor’s functions without needing extensive training.
- Setting Up the HMI Panel: Start by selecting the HMI model compatible with your setup (e.g., a Siemens Basic or Comfort Panel) in TIA Portal’s “Devices & Networks” view. Assign it an IP address to enable communication with the PLC.
- Screen Layout Design: To keep the HMI user-friendly, divide the screen into clearly defined sections:
- Control Panel: Place buttons for starting, stopping, and adjusting speed in a central area so they’re easy to locate.
- Status Display: Reserve a section for displaying real-time data, like conveyor speed and object detection alerts, enabling operators to monitor the system at a glance.
- Alerts and Messages: Add an area for safety alerts, so operators can quickly identify any issues or warnings.
- Design Consistency: Use consistent colors and icons to represent specific actions (e.g., green for “Start,” red for “Stop,” and yellow for “Alert”). Consistency makes it easier for operators to understand the interface and reduces the likelihood of errors.
This structure ensures that operators can control the system efficiently and respond quickly to any issues.
Display and Controls
The HMI should display critical information about the conveyor system’s status and allow operators to control the system effectively. Below are key elements to include:
- Real-Time Data Display:
- Conveyor Speed: Display the current speed in real-time. Use a digital display or a simple bar graph to represent the speed visually.
- Object Detection Status: Show the status of the sensors in real-time, indicating if an object is detected on the conveyor. Use icons or colored indicators (e.g., green for “Clear” and red for “Object Detected”) to make this information quickly understandable.
- Control Buttons:
- Start/Stop Buttons: Place prominent buttons for starting and stopping the conveyor. Assign the start button a green color and the stop button red, aligning with standard industrial practices.
- Speed Adjustment: Add buttons or a slider control for operators to increase or decrease the conveyor speed. Connect these controls to the PLC’s speed control variables to allow real-time speed changes.
- Reset Button: Provide a reset button that can clear any active alarms or alerts and restart the system after an emergency stop. Ensure this button is slightly smaller and positioned away from the start/stop buttons to avoid accidental presses.
- Data Logging (Optional): If required, configure the HMI to log key data points, like conveyor speed changes or sensor activity. This feature can be valuable for maintenance and troubleshooting, allowing operators to review system performance over time.
These display and control elements make the HMI both informative and functional, enabling operators to manage the system smoothly.
Integrating Safety Features on HMI
Safety is a critical component in industrial automation. The HMI should allow operators to access safety features easily, ensuring a quick response in case of any issues.
- Emergency Stop Button:
- Position and Color: Add a prominent red emergency stop button on the HMI. Position it on the top or bottom of the screen so it’s easy to find in an emergency.
- PLC Connection: Link the emergency stop button directly to the PLC’s emergency stop logic. When pressed, this button should immediately halt the conveyor and display an emergency alert on the HMI.
- Alert System:
- Visual Alerts: Configure the HMI to display alerts for faults, such as motor overloads or sensor malfunctions. Use icons or flashing colors to capture attention quickly. For example, a yellow icon can indicate a minor issue, while a red flashing alert can signify a critical problem.
- Audible Alerts: Enable an audio signal for critical alerts, if supported by the HMI. This feature adds another layer of notification, ensuring operators notice important issues even if they’re not looking at the screen.
- Clear Instructions for Safety Protocols:
- Alarm Acknowledgment: Include a feature for operators to acknowledge alarms. Once they acknowledge an alert, the system will mark it as reviewed, helping operators focus on unresolved issues.
- Guidance Messages: Add brief text instructions in the alert section, guiding operators on what to do in case of specific alerts. For example, “Check Sensor Connection” or “Reduce Speed” provides immediate guidance on troubleshooting.
Integrating these safety features ensures that operators can respond quickly to emergencies, enhancing both the safety and reliability of the conveyor system.
This HMI design not only makes the conveyor system easier to operate but also helps maintain safety and efficiency in an industrial setting. The intuitive layout, real-time data display, and built-in safety features make this HMI both practical and user-friendly, meeting the demands of modern industrial automation. By following this approach, you create an interface that supports clear communication and empowers operators to control the system with confidence.
6. Testing and Validation
Testing and validation are crucial for ensuring that the intelligent conveyor belt system performs reliably and meets all project specifications. This section provides a step-by-step guide to testing the control logic in TIA Portal’s simulation environment, debugging common issues, and conducting real-world tests to validate the system under actual operating conditions.
Testing the Control Logic in TIA Portal’s Simulation Environment
TIA Portal includes powerful simulation tools that allow you to test the PLC logic and HMI functionality without needing physical hardware. This saves time and resources while ensuring the program behaves as intended.
- Setting Up the Simulation:
- Open the project in TIA Portal and navigate to the “Online” menu.
- Select “Start Simulation” for the PLC program. This activates a virtual environment where the PLC logic runs as if it were connected to physical hardware.
- For the HMI, enable runtime simulation to test its interaction with the PLC in real-time.
- Testing Key Functions:
- Speed Control: Adjust speed levels through the HMI interface in the simulation. Verify that the PLC updates the motor control variables accordingly.
- Object Detection: Simulate sensor inputs by manually toggling digital input values in the simulation environment. Check that the conveyor stops or resumes operation based on the sensor status.
- Emergency Stop: Activate the emergency stop function in the simulation. Confirm that all operations halt immediately and the HMI displays a corresponding alert.
- Using Diagnostic Tools:
- Use the “Watch Table” in TIA Portal to monitor variable values in real-time. This tool helps verify that sensor inputs, speed adjustments, and control outputs are processed correctly.
- Analyze the logic flow by stepping through the program in simulation mode to ensure all conditions and outputs function as expected.
Simulating the system in TIA Portal helps identify and correct issues early, streamlining the development process before moving to physical hardware.
Debugging Tips and Common Issues
Even with careful programming, issues can arise during testing. Below are common problems and practical solutions:
- Incorrect Sensor Responses:
- Symptom: The conveyor doesn’t stop when an object is detected.
- Solution: Verify the sensor’s digital input configuration. Ensure that the sensor address matches the input configured in the PLC program. Use the “Watch Table” to confirm the PLC receives the sensor signal.
- Speed Control Failures:
- Symptom: The conveyor doesn’t change speed or responds inconsistently to HMI inputs.
- Solution: Check the ladder logic for speed control. Ensure the rungs are correctly linked to the speed variables and verify the values being sent to the motor control output.
- HMI Button Malfunctions:
- Symptom: Buttons on the HMI do not trigger the intended actions.
- Solution: Check the tag assignments in the HMI configuration. Ensure that each button’s action is correctly linked to a PLC variable. Also, confirm that the HMI and PLC are connected and communicating via the same network protocol.
- General Debugging Tips:
- Simplify Tests: Test individual rungs or sections of the program separately before running the full system.
- Review Error Logs: Use TIA Portal’s diagnostic messages to identify and resolve errors. Error codes often point directly to the problem’s source.
- Peer Review: Have a colleague review the program logic. A fresh perspective can often catch overlooked errors.
Proactively addressing these issues during the simulation phase ensures a smoother transition to physical testing.
Real-World Testing
After successful simulation testing, real-world testing is essential to validate the system’s performance under actual operating conditions. This step ensures the hardware and software interact seamlessly and the system is ready for deployment.
- Hardware Setup:
- Connect the PLC to the physical hardware, including sensors, motors, and the HMI.
- Verify that all devices are powered and communicate correctly with the PLC. Use TIA Portal’s “Devices & Networks” view to check the connections and IP addresses.
- Functional Testing:
- Speed Control: Use the HMI to adjust the conveyor speed in real-time. Observe the motor’s response and ensure it matches the programmed speed levels.
- Object Detection: Place objects on the conveyor and confirm the sensors detect them. The conveyor should stop or resume based on sensor feedback as programmed.
- Emergency Stop: Test the physical emergency stop button. Ensure it halts all operations immediately and displays an alert on the HMI.
- Stress Testing:
- Run the conveyor continuously for an extended period to test its durability and reliability under regular operating conditions.
- Introduce edge cases, such as rapid speed changes or closely spaced objects, to ensure the system handles unexpected scenarios effectively.
- Operator Feedback:
- Have operators use the system and provide feedback on the HMI design and overall usability. Adjust the interface or logic based on their suggestions to improve functionality and user experience.
- Final Validation:
- Compare the system’s performance against the initial project requirements. Ensure all features, including speed control, object detection, and safety mechanisms, work as intended.
- Document the test results and any adjustments made during the validation process for future reference.
Testing and validation ensure the intelligent conveyor belt system is robust, reliable, and ready for deployment. By leveraging TIA Portal’s simulation tools and conducting thorough real-world tests, you can identify and resolve potential issues, delivering a high-quality automated solution tailored to industrial needs.
7. Project Optimization and Advanced Features
After implementing and validating the intelligent conveyor belt system, further optimization and the addition of advanced features can significantly enhance its performance, reliability, and usability. This section explores strategies for fine-tuning system performance, incorporating predictive maintenance, and integrating advanced HMI features.
Optimizing System Performance
To ensure the conveyor system operates at peak efficiency, it is essential to identify and address potential performance bottlenecks. The following optimization techniques can improve the system’s functionality and responsiveness:
- Fine-Tuning Sensor Sensitivity:
- Adjustment: Sensors play a critical role in object detection. Fine-tune their sensitivity to minimize false positives or missed detections. For instance, adjust the detection range and angle for proximity sensors to better match the conveyor’s layout and material characteristics.
- Testing: Regularly test sensors under different lighting conditions, object materials, and conveyor speeds to ensure consistent performance.
- Smoother Speed Transitions:
- Ramp-Up/Ramp-Down Logic: Introduce ramp-up and ramp-down logic in the PLC to ensure the conveyor accelerates or decelerates smoothly. This reduces mechanical stress on the motor and minimizes the risk of damage to transported items.
- Adaptive Speed Control: Use feedback from sensors to dynamically adjust conveyor speed based on the load. For example, the conveyor can slow down when detecting closely spaced objects to prevent collisions.
- Energy Efficiency:
- Idle Mode: Program the system to enter an energy-saving mode during periods of inactivity. This can involve slowing the conveyor to a minimal speed or stopping it entirely until a new object is detected.
- Load-Based Motor Control: Optimize motor power based on the conveyor’s load, reducing energy consumption during light workloads.
Implementing these optimizations enhances the system’s efficiency, reduces wear and tear, and lowers operational costs.
Adding Predictive Maintenance
Predictive maintenance leverages sensor data and analytics to identify potential issues before they result in system failures. By incorporating predictive maintenance, the conveyor system becomes more reliable and cost-effective.
- Monitoring Critical Components:
- Motor Health: Install sensors to monitor motor temperature, vibration, and current draw. Abnormal readings can indicate issues such as overheating or mechanical wear.
- Belt Wear: Use tension sensors or visual inspection cameras to detect signs of wear or misalignment on the conveyor belt.
- Data Analysis:
- Threshold Alerts: Program the PLC to trigger alerts when sensor readings exceed predefined thresholds. For example, if motor vibration increases beyond acceptable levels, the system can notify operators via the HMI.
- Trend Analysis: Store sensor data over time and analyze trends to predict when maintenance will be needed. For instance, a gradual increase in motor current draw may indicate impending failure.
- Automated Adjustments:
- Self-Correction: Integrate logic for automatic adjustments, such as reducing conveyor speed when excessive vibration is detected. This allows the system to operate safely until maintenance can be performed.
- Maintenance Alerts: Configure the HMI to display clear, actionable alerts, such as “Inspect Motor Bearings” or “Replace Belt,” helping operators address issues proactively.
Predictive maintenance reduces unplanned downtime, extends equipment life, and improves overall system reliability.
Advanced HMI Features
Enhancing the HMI with advanced features improves operator experience and enables better system monitoring and control. Below are some suggestions for incorporating advanced HMI functionalities:
- Remote Access:
- Cloud Integration: Allow the HMI to connect to a cloud-based platform, enabling remote monitoring and control of the conveyor system. Operators and managers can access real-time data and alerts from any location.
- Mobile Compatibility: Develop a mobile-friendly interface for operators to monitor and control the system using smartphones or tablets.
- Data Logging:
- Operational Records: Configure the HMI to log key performance metrics, such as conveyor speed, object detection events, and energy consumption. These logs can be invaluable for troubleshooting and optimizing operations.
- Export Options: Enable data export to formats like CSV or Excel, allowing managers to analyze system performance offline.
- User-Defined Alerts:
- Customizable Notifications: Allow operators to define their own alert thresholds based on specific operational requirements. For example, an operator can set a notification for when the conveyor speed drops below a certain level.
- Prioritized Alerts: Implement a tiered alert system, where critical alerts (e.g., motor failure) are distinguished from minor warnings (e.g., sensor misalignment) using color-coding or sound variations.
- Interactive Training Modules:
- Guided Tutorials: Add interactive tutorials to the HMI for new operators. These can provide step-by-step instructions for operating and troubleshooting the system.
- Simulation Mode: Include a simulation mode on the HMI for training purposes, allowing operators to practice using the system without affecting real operations.
These advanced features make the system more versatile and user-friendly, aligning it with modern industrial automation trends.
By optimizing system performance, integrating predictive maintenance, and adding advanced HMI features, the intelligent conveyor belt system evolves into a highly efficient and reliable industrial solution. These enhancements demonstrate a forward-thinking approach, showcasing your ability to design systems that meet current needs while anticipating future challenges. This level of innovation and attention to detail is a valuable asset in the field of industrial automation.
8. Conclusion
The development of the intelligent conveyor belt system highlights the potential of modern industrial automation tools like TIA Portal to create flexible, reliable, and efficient solutions. This section summarizes the project’s goals and accomplishments, discusses opportunities for future enhancements, and emphasizes the relevance of these skills to broader industrial applications.
Summary of Project Goals and Accomplishments
The primary goal of this project was to design and implement a conveyor belt system with intelligent features that address modern industrial needs. This was achieved by incorporating key functionalities:
- Variable Speed Control: The system offers dynamic speed adjustments to handle different workloads and optimize efficiency. Operators can easily modify speeds using the intuitive HMI interface.
- Object Detection and Safety: Sensors enable the system to detect objects on the conveyor and trigger appropriate responses, such as stopping to prevent collisions. The inclusion of an emergency stop mechanism ensures safe operation, protecting both equipment and personnel.
- User-Friendly HMI: The HMI was designed to be clear and intuitive, providing operators with real-time data, control options, and actionable alerts for enhanced usability.
- Robust Testing and Validation: Thorough testing in simulation and real-world environments ensured the system’s reliability and readiness for industrial deployment.
These accomplishments demonstrate the ability to create an integrated system that balances technical complexity with operational simplicity, showcasing advanced programming, design, and troubleshooting skills.
Future Enhancements and Learning Outcomes
While the project successfully met its objectives, there are opportunities for further improvement:
- Enhanced Predictive Maintenance:
- Future versions could integrate advanced analytics, such as machine learning algorithms, to predict potential failures with greater accuracy.
- Adding real-time cloud monitoring would enable remote diagnostics and further reduce downtime.
- Scalability:
- The system could be expanded to handle multiple conveyors working in synchronization. This would require advanced communication between PLCs and coordinated control logic.
- Incorporating robotic arms or automated sorting mechanisms could make the system more versatile.
- Energy Optimization:
- Implementing energy-efficient components and algorithms to minimize power consumption during idle or low-load periods could improve the system’s sustainability.
- Operator Training and Simulation:
- Expanding the HMI to include detailed training modules or simulation environments would help new operators learn the system more effectively.
Personal Learnings: This project provided valuable insights into designing and implementing complex automated systems. Key takeaways include:
- The importance of thorough testing and debugging to ensure reliability.
- The need for clear, user-centric HMI design to make advanced systems accessible to operators.
- The value of predictive maintenance in reducing operational costs and increasing system longevity.
These experiences reflect a commitment to continuous improvement and adaptability in tackling technical challenges.
Relevance to Industrial Applications
The skills demonstrated in this project are highly applicable to a wide range of industrial scenarios, making them valuable to prospective employers:
- Broad Industry Applicability:
- The system’s design principles can be applied to various sectors, including manufacturing, logistics, food processing, and pharmaceuticals.
- Features such as object detection, speed control, and HMI design are critical for optimizing workflows and ensuring safety in these industries.
- Scalable Expertise:
- The ability to design modular systems means the expertise gained here can scale to larger, more complex projects, such as multi-line production facilities or automated warehouses.
- Alignment with Industry 4.0:
- By integrating predictive maintenance, real-time monitoring, and user-friendly controls, this project aligns with the goals of Industry 4.0, which emphasizes automation, data exchange, and smart systems.
- The forward-thinking design demonstrates a readiness to contribute to cutting-edge industrial initiatives.
Navigating the Evolving Job Market in Central Europe: Insights on Domesticity, Regulation, and High-Demand Fields
Estimated Reading Time: 19 minutes Europe’s job market is both competitive and diverse, attracting skilled professionals from around the world who seek robust career growth, work-life balance, and high-quality living standards. However, navigating the European job market is challenging, particularly due to the differences in domesticity and regulation across professions. Each profession in Europe may require varying degrees of local knowledge, professional licensing, and qualifications, impacting how accessible certain roles are for international job seekers.
Legal Loopholes and Ethical Marketing: How Companies Can Navigate Content Boundaries
In an era where digital marketing and social media engagement drive business success, companies must navigate a fine line between maximizing impact and remaining within legal and ethical boundaries. Regulatory loopholes, shifting policies, and evolving consumer expectations require businesses to craft strategies that both satisfy legal requirements and preserve public trust. Although legal gray areas are often framed negatively, they can offer innovative avenues for marketers—provided they do not compromise ethical standards or erode brand credibility. This article explores how companies can leverage legal ambiguities responsibly, highlighting transparency as a competitive advantage and dissecting the crucial role of consumer perception in shaping long-term brand trust.
Keyphrases: Ethical Marketing, Regulatory Loopholes in Advertising, Consumer Trust in Brand Strategy
Table of Contents
Introduction
Marketing has always been about persuasion, but the modern digital ecosystem has introduced both unprecedented reach and unparalleled scrutiny. Traditional advertising channels such as print and broadcast television have given way to multi-platform campaigns that connect brands with global audiences in seconds. While this interconnected environment presents exciting opportunities to capture consumer attention, it also carries heightened legal and ethical complexities.
Agencies and regulators struggle to keep pace with the rapid evolution of online platforms, leaving gaps in existing laws that companies might exploit for competitive advantage. Simultaneously, public awareness of unethical marketing tactics has soared; social media allows users to swiftly call out practices that seem manipulative, inauthentic, or harmful. The tension between pushing creative boundaries and adhering to standards of transparency and fair play has never been more pronounced.
At the heart of this tension lies the question of brand reputation. Even when certain marketing tactics are technically legal, they can erode consumer trust if perceived as disingenuous. Negative viral attention can lead to PR crises, diminished sales, or even regulatory crackdowns—hardly worth the short-term gains. Consequently, it’s not only about following the law but also about considering the broader societal implications of every marketing strategy.
This article delves into how companies can navigate these sometimes murky waters. We begin by examining the role of legal loopholes in modern advertising, illustrating how certain marketing tactics skirt the edge of compliance. We then explore the ethical considerations that separate savvy strategy from outright manipulation. From there, we turn to transparency—arguing that proactive disclosure and honest communication can function as powerful differentiators. We also analyze the dynamics of consumer perception and how swiftly it can shift, even when marketing strategies are legally sound. Finally, we outline actionable steps for balancing legal compliance with ethical marketing, underscoring why responsible stewardship of public trust is a core determinant of sustainable success.
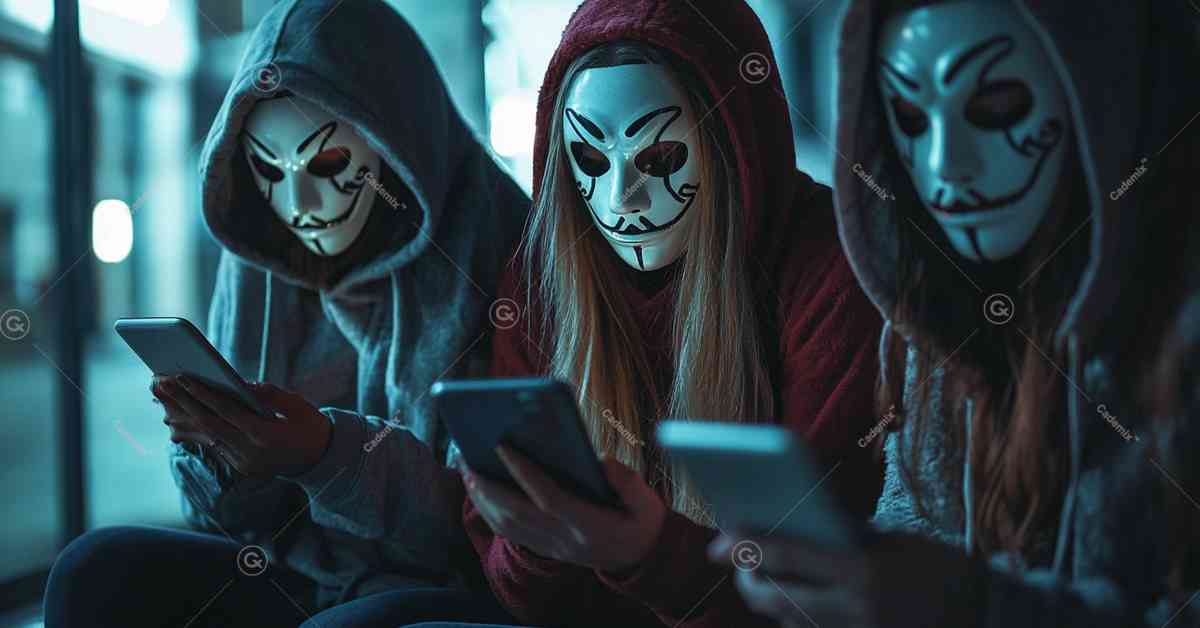
The Role of Legal Loopholes in Marketing
A Changing Legal Landscape
The regulatory environment that governs advertising is in a constant state of flux. Laws designed for print or broadcast media do not always translate cleanly into the realities of digital campaigns. In many jurisdictions, internet-focused regulations lag behind technological innovation, opening the door for companies to adopt creative interpretations that stray near the edge of compliance.
For instance, influencer marketing has exploded in popularity, yet guidelines for disclosing paid partnerships can be ambiguous and vary by region. An influencer might bury a sponsorship disclosure at the bottom of a lengthy description, or use vague language like “thanks to Brand X” rather than explicitly stating a paid arrangement. Legally, such disclaimers may suffice—or they may sit in a gray area, causing confusion and potential legal exposure.
Exploiting Ambiguity: Common Loopholes
Companies and marketers often feel pressure to squeeze maximum value from every campaign. In doing so, they might rely on tactics such as:
- Influencer and Sponsored Content: While many nations require labels like #ad or #sponsored, the exact rules for clarity can be loose. Brands may push the boundaries by making disclosures easy to overlook, trusting that most audiences won’t notice the fine print.
- Targeted Advertising and Data Privacy: Regulations such as the General Data Protection Regulation (GDPR) and the California Consumer Privacy Act (CCPA) govern personal data usage. Yet companies frequently find legal ways to micro-target by aggregating or anonymizing data in a manner that arguably skirts strict consent requirements.
- Comparative Advertising: Certain jurisdictions allow comparative ads if they are “technically true,” even if the broader picture might be misleading. A brand might highlight that its product has one feature better than a competitor’s, omitting the competitor’s other strong points.
- Pricing Strategies: Online retailers might artificially inflate a “regular price” to make a sale price look more appealing. Although borderline deceptive, these strategies can be legally permissible if disclaimers exist, or if regional laws do not strictly address the practice.
- Psychological Tricks: Scarcity marketing and FOMO (fear of missing out) tactics—countdown timers, limited availability notices—may be legal, yet can be perceived as manipulative if the scarcity claim isn’t genuine.
While such maneuvers can offer short-term boosts, the risk of reputational damage looms large. Consumers increasingly share their experiences on social media; once suspicious or unethical tactics go viral, a brand’s carefully orchestrated campaign may backfire.
The Innovation vs. Exploitation Debate
Some executives argue that exploring legal loopholes is simply part of business innovation. Historically, industries from finance to pharmaceuticals have leveraged loopholes to gain a competitive edge, prompting new regulations to close those gaps over time. In the marketing world, similarly, forward-thinking businesses seek to “stay ahead” of regulators.
However, a fine line separates creative interpretation of existing rules from blatant exploitation. The latter can quickly degrade consumer trust and invite strict regulatory scrutiny. In the age of instant online backlash and persistent public memory, short-term tactics that appear exploitative can undermine brand equity built over years. From a sustainability viewpoint, persistent reliance on loopholes is a vulnerable strategy: once regulators step in or the public mood shifts, a brand can lose a key competitive advantage—and possibly face hefty legal penalties.
Ethical Considerations: The Thin Line Between Strategy and Manipulation
Beyond Legal Compliance
While compliance may protect a company from fines or lawsuits, it doesn’t necessarily shield against broader ethical questions. A marketing strategy can be perfectly legal but still feel manipulative or deceitful to an audience. When consumer perception sours, it can result in lost sales, negative press, or irreversible harm to brand loyalty.
For instance, let’s consider disclaimers in social media ads. If a brand prints essential information in minuscule text or uses cryptic legal jargon that everyday consumers can’t easily understand, it may be “compliant” with regulations requiring disclosure. Yet from an ethical standpoint, such practice conceals vital details from the very audience the regulation is meant to protect. Over time, that gap between technical compliance and transparent communication creates distrust.
Consumer Autonomy and Informed Choice
One of the cornerstones of ethical marketing is respecting consumer autonomy. People have a right to make decisions based on accurate information, free from undue manipulation. Strategies that prey on cognitive biases—such as illusions of scarcity or hidden auto-renewal clauses—can weaken consumer agency. These approaches might yield short-term sales or sign-ups, but they also erode genuine goodwill.
Marketing that empowers consumers, by contrast, tends to foster durable loyalty. This might involve clarifying terms and pricing, offering free trials without complex cancellation policies, or providing clear disclaimers on influencer content. Enabling an informed choice does not preclude persuasive advertising; it simply ensures that persuasion respects the consumer’s ability to judge and decide.
Ethical Pitfalls in the Social Media Era
Social media magnifies ethical concerns by amplifying both successes and failures at lightning speed:
- Viral Outrage: A single tweet accusing a brand of misleading advertising can spark a wave of negative publicity. Even if a company can legally defend its campaign, public sentiment may not be swayed by technicalities.
- Echo Chambers: Online communities can form strong echo chambers, meaning both positive and negative narratives about a brand can gain momentum independently of objective facts.
- Influencer Ethics: An influencer’s entire persona is often built on authenticity; undisclosed sponsorships, or obviously staged content, can damage an influencer’s reputation and by extension, the partnering brand.
Beyond the immediate fallout, unethical practices can lead to calls for stronger regulations, industry blacklists, or mass boycotts. Such outcomes rarely remain confined to a single campaign but can have ripple effects across product lines and markets.
Long-Term Brand Health
Ethical considerations also have a strong correlation with long-term brand health. Executives sometimes view marketing as a short-term, numbers-driven venture. However, a purely transactional approach neglects the reality that trust—once broken—can be difficult to rebuild. Customers who feel duped are more likely to share negative experiences, significantly impacting a brand’s reputation.
By contrast, a transparent and fair approach to marketing has a cumulative, positive effect. Even if a particular campaign doesn’t yield maximal immediate returns, it can strengthen the intangible goodwill that forms the backbone of sustained brand success. Investors increasingly account for reputational risk and ethical conduct, as indicated by the rise of ESG (Environmental, Social, and Governance) frameworks influencing corporate valuations. In this sense, an ethical marketing strategy isn’t just a moral stance—it’s a pragmatic, forward-thinking investment.
Transparency as a Competitive Advantage
Redefining Transparency
Traditionally, transparency in marketing meant adhering to legal requirements for disclosures—such as listing ingredients on a food package or clarifying an interest rate in a financial product. Today, the concept extends far beyond minimal compliance. Brands that exceed basic mandates—voluntarily revealing relevant information, explaining complexities in plain language, and engaging openly with consumer inquiries—often gain a halo of trust.
In a world where skepticism runs high and social media can amplify missteps, going “above and beyond” is no longer a nicety; it’s a strategic move. Transparency can differentiate a company from competitors still operating near the limits of legality or clarity. For example, a supplement brand might provide third-party lab test results on its website, even if not strictly required by law. Such transparency demonstrates accountability and builds confidence among health-conscious consumers who fear misleading claims.
The Elements of Authentic Transparency
To wield transparency effectively, organizations need to integrate it throughout the marketing lifecycle:
- Prominent, Plain-Language Disclosures: Instead of burying disclaimers in fine print, place them where consumers naturally look. Use simple language to explain any potential risks, fees, or data usage policies.
- Proactive Communication: Anticipate consumer questions or doubts and address them in marketing materials or FAQ sections, rather than waiting for complaints to surface.
- Open-Source or Behind-the-Scenes Views: Providing glimpses into supply chains, production methods, or product development fosters a sense of authenticity. This approach is especially potent for brands aiming to highlight ethical sourcing or sustainability.
- Consistent Messaging: Transparency is undermined if a brand’s claims on social media contradict what’s stated on product labels or official websites. A coherent approach across all platforms signals reliability.
Case Study: Radical Transparency
Apparel brand Everlane popularized the term “radical transparency,” openly sharing factory information and itemized cost breakdowns—revealing how much money went into labor, materials, transportation, and markup. While not every company can adopt this extreme level of detail, Everlane’s success story underscores how authenticity can forge strong connections with consumers.
Importantly, radical transparency isn’t without risks: it invites scrutiny of every claim and number. However, for brands prepared to stand behind their processes, the resulting trust and loyalty can be invaluable. As with any marketing strategy, consistency is vital—breaking promises or obscuring details can quickly dissolve the goodwill earned.
The ROI of Being Transparent
Transparency yields tangible benefits. Research consistently shows that consumers are more likely to buy from brands they perceive as honest. Word-of-mouth recommendations also flourish among loyal fans who appreciate above-board practices. Over time, increased customer lifetime value, higher net promoter scores, and fewer public relations crises can more than offset any short-term gains sacrificed by refusing to exploit legal gray areas.
Moreover, transparency aligns a brand with broader cultural trends favoring social responsibility. Younger consumers, especially Gen Z, actively seek out companies that share their values on environmental stewardship, inclusivity, and community engagement. Clear, honest marketing can thus attract conscientious buyers and position the brand favorably among socially aware demographics.
The Impact of Consumer Perception
Regulation vs. Reputation
Regulatory compliance is vital but not the sole determinant of a marketing initiative’s success or failure. As public attitudes evolve, tactics that once seemed acceptable can fall out of favor practically overnight. Consider the rapid shift in attitudes toward data privacy. A few years ago, many users barely noticed how apps collected and leveraged their personal data. Today, revelations about data breaches or invasive tracking can ignite widespread outrage. Tech giants like Apple have introduced privacy changes (e.g., App Tracking Transparency) that reshape the entire advertising ecosystem.
This fluid landscape means companies must continuously monitor consumer sentiment and be prepared to adjust their marketing strategies. Even if an approach remains legally permitted, consumer backlash can outweigh any short-lived benefits. In some cases, negative public perception can spur legislation, effectively closing the loophole or restricting the practice altogether.
The Acceleration of Online Dialogue
Social media’s lightning-fast feedback loop adds another layer of complexity. A single disaffected customer can post a viral video or screenshot, drawing attention from journalists, advocacy groups, and regulators. Embarrassing marketing missteps can snowball into boycotts or become trending hashtags, severely damaging a brand’s standing.
Brands that ignore or dismiss initial criticism risk appearing tone-deaf. By contrast, rapid and respectful engagement demonstrates accountability. For instance, if consumers accuse a fashion label of greenwashing, an immediate, transparent response that includes third-party certifications or clarifies sustainability practices can mitigate damage. Silence or denial often fuels the backlash.
Trust as a Fragile Asset
Above all, consumer trust must be recognized as a fragile asset. It can be painstakingly built over years through consistent performance and messaging, yet undone in a matter of hours by an ill-advised campaign. Indeed, trust is the hidden currency in every marketing transaction. Consumers base their decisions not merely on product features or price but also on a company’s perceived integrity.
Interestingly, trust can be somewhat resilient if it has deep roots. Brands with longstanding positive reputations sometimes weather crises better, as loyalists offer the benefit of the doubt. Yet repeated ethical lapses or a pattern of borderline practices will eventually catch up, even with historically admired companies. Sincerity and reliability must be continuously reinforced through actions, not just words.
Shifts in Demographic Expectations
Younger generations, in particular, have grown up in an era dominated by social media and rapid information exchange. Their consumer choices often reflect a heightened sensitivity to ethical considerations, from labor practices to environmental stewardship. These demographics are more likely to mobilize collective pushback or boycott calls when a brand’s marketing crosses ethical lines.
Meanwhile, older consumers who once trusted traditional advertising may also feel betrayed if they discover manipulative tactics. In short, no demographic is immune to the influence of consumer perception. To remain viable in this environment, companies need more than just a surface-level compliance strategy; they need a genuine commitment to responsible marketing.
Strategies for Balancing Legal Compliance and Ethical Marketing
1. Anticipate Future Regulations
Rather than merely reacting to existing laws, ethical marketers consider the direction in which regulations are headed. Legislative bodies around the world are focusing on data protection, influencer disclosure, environmental claims, and fair pricing. Forward-thinking companies track these signals and adapt proactively, allowing them to differentiate themselves in a landscape where competitors may still rely on loopholes soon to be closed.
- Monitoring Regulatory Trends: Follow announcements from agencies like the Federal Trade Commission (FTC) in the U.S. or the European Commission. Attend industry seminars or maintain an internal compliance watchdog team.
- Voluntary Ethical Standards: Some sectors, like cosmetics or organic foods, develop self-regulatory guidelines or certifications. Participating in such initiatives can signal to consumers that a brand operates above the legal minimum.
2. Adopt a Consumer-First Mindset
At the core of ethical marketing lies the principle of prioritizing the consumer’s best interests. This approach involves designing campaigns and strategies that aim for clarity, honesty, and mutual benefit.
- User-Friendly Disclaimers: Ensure disclaimers and key information are not only legally compliant but also easily digestible by a lay audience.
- Accessible Customer Service: Offer multiple channels—email, chat, social media, phone—for consumers to ask questions or voice concerns, and respond promptly.
- Feedback Integration: When consumers point out confusing or misleading content, incorporate their feedback into immediate improvements. Publicly acknowledge and rectify mistakes.
This empathetic viewpoint fosters a relationship based on respect rather than exploitation. Consumers who sense genuine concern for their well-being often reward brands with loyalty and referrals.
3. Utilize Ethical AI and Automation
Automated marketing tools powered by artificial intelligence (AI) offer precision targeting and personalization, but can also cross ethical lines if not carefully configured. For example, AI might show ads to vulnerable demographics or harvest user data without explicit consent.
- Data Minimization: Collect and store only as much consumer data as necessary. Excessive data hoarding increases legal risk and can be perceived as invasive.
- Bias Audits: Test AI models for hidden biases that might target or exclude certain groups unfairly.
- Explainability: Strive for transparency about how AI-driven recommendations or personalization algorithms operate, particularly if they could influence major consumer decisions such as credit or insurance.
By setting clear ethical parameters for AI usage, marketers can leverage advanced technologies without straying into privacy violations or manipulative tactics.
4. Invest in Ongoing Compliance Training
Regulations and best practices evolve rapidly, particularly in digital marketing. Companies that treat compliance as a once-a-year checkbox exercise risk falling behind or inadvertently flouting new guidelines.
- Regular Workshops: Schedule quarterly or semi-annual sessions that update marketing teams on pertinent regulations, from GDPR expansions to updated FTC guidelines.
- Cross-Functional Alignment: Ensure legal, marketing, and product development teams maintain open lines of communication. Marketing campaigns often overlap with product functionalities—particularly regarding data collection or integrated user experiences.
- Cultural Integration: Emphasize that ethical and legal considerations aren’t an afterthought but an integral part of creative brainstorming and campaign development. Reward employees who spot potential pitfalls early.
5. Create an Accountability Framework
Implementing a robust accountability system can deter harmful shortcuts and encourage ethical decision-making at every level.
- Ethics Committees or Boards: Large organizations may establish committees that review proposed campaigns for potential ethical or reputational concerns.
- Whistleblower Protections: Encourage employees to voice concerns about misleading tactics without fear of retaliation.
- Transparent Reporting: Periodic public reports on marketing practices and user data handling can reinforce commitment to ethical standards, building trust among stakeholders.
Conclusion
Legal loopholes often emerge when regulations lag behind the fast-paced evolution of digital marketing. While it may be tempting for brands to exploit these gaps for short-term gains, doing so can come at a steep cost. In a landscape where consumers exchange information instantly and judge brand authenticity harshly, even technically legal strategies can spark public outrage if perceived as unethical or manipulative.
Long-term success hinges on more than simply avoiding lawsuits and fines. Indeed, the delicate interplay between legal compliance and ethical responsibility plays a determining role in brand perception, loyalty, and overall growth. Companies that strive for transparency, respect consumer autonomy, and anticipate emerging regulations can transform marketing compliance from a burden into a strategic differentiator. Ethical marketing isn’t just about virtue-signaling or meeting the bare minimum; it’s about aligning business objectives with genuine consumer value.
Ultimately, the ability to navigate content boundaries without sacrificing integrity reflects a deeper commitment to doing right by the customer. It acknowledges that a brand’s most valuable currency in the digital age is not just revenue or market share, but the trust it earns—and keeps—among those it serves. Forward-thinking organizations recognize that sustainable, reputation-building marketing practices will always outlast fleeting advantages gained through questionable tactics. By championing both innovation and ethical rigor, companies can indeed leverage legal gray areas while upholding the principles that define responsible, enduring success.
Technology-Driven Career Acceleration: Why AI is Not Enough
Estimated Reading Time: 16 minutes Technology-Driven Career Acceleration needed! AI tools for career planning promise transformative potential, but their limitations, particularly for PhD graduates and international job seekers, highlight the need for human-centric, inclusive, and culturally sensitive approaches
Post-Event Evaluation: Why It Matters and How to Do It Right
Estimated Reading Time: 16 minutes A comprehensive post-event evaluation is essential in event management, as it enables continuous improvement, optimizes future event planning, and ensures stakeholder satisfaction by analyzing feedback, metrics, and trends
Psychological Factors in Digital Marketing: How Social Media Influences Purchasing Decisions
This article delves into the psychological underpinnings that shape consumer behavior in the context of digital marketing, with a particular focus on social media platforms. It examines how various cognitive and emotional triggers—including social proof, scarcity, personalization, and trust signals—can influence the way users interpret advertisements and make purchasing decisions. Drawing on a range of marketing and behavioral science principles, the discussion highlights both the opportunities and potential ethical pitfalls of harnessing psychological drivers to sway audiences. Real-world examples illustrate how brands engage followers through well-crafted messages, storytelling techniques, and influencer collaborations. The article closes by offering best practices for achieving marketing goals without compromising consumer well-being or trust. Marketers and business owners alike can benefit from understanding these foundational principles to design strategies that resonate with audiences, foster loyalty, and responsibly leverage the power of social media.
By Samareh Ghaem Maghami, Cademix Institute of Technology
Table of Contents
Introduction
The digital landscape has evolved dramatically over the past decade, reshaping how consumers interact with brands. Social media platforms—ranging from Facebook and Instagram to LinkedIn and TikTok—are no longer merely channels for personal connections; they have become powerful marketplaces where businesses can directly engage prospective buyers. This transformation has brought with it a deeper reliance on psychological triggers that influence attention, interest, and, ultimately, purchasing behavior.
Brands now have a plethora of tools at their disposal, from precise targeting algorithms to data analytics, enabling them to tailor messages to specific demographic and psychographic segments. This capacity to reach consumers “where they are” has amplified the importance of understanding the psychological mechanisms at play. While traditional advertising might have relied heavily on persuasive copy or eye-catching visuals, digital marketing must account for real-time feedback loops, ongoing audience interaction, and the swift propagation of trends.
Understanding these psychological factors is essential not only for optimizing campaigns but also for maintaining ethical standards. Tactics that exploit vulnerabilities—such as fear of missing out or social comparison—can backfire if perceived as manipulative. Hence, the social media age calls for a nuanced balance: leveraging core principles of behavioral psychology while respecting consumer autonomy. Within this article, readers will encounter a comprehensive overview of the key psychological drivers that can make or break a digital marketing campaign. The goal is to provide a framework for designing strategies that resonate emotionally and cognitively, encouraging sustainable, trust-based relationships between brands and their audiences.
The Role of Social Media in Consumer Behavior
Social media platforms serve as digital ecosystems where users not only consume content but also participate in creating and sharing it. This environment enables a constant interplay of information, social validation, and feedback, making it fertile ground for marketing efforts that tap into fundamental human needs—such as belonging, self-expression, and esteem.
In a traditional marketing funnel, awareness, interest, decision, and action were often delineated stages. Now, these stages can merge or even overlap in real time. A single post shared by an influential figure might spark immediate consumer action, bypassing the usual extended deliberation periods. Alternatively, a well-crafted comment section might prolong a user’s interest, allowing them to gather social proof from peers before making a purchase.
The shift toward digital-first advertising has also democratized marketing to some extent, enabling smaller businesses to compete with global brands if they can create engaging, shareable content. However, the challenge lies in understanding the psychological currents beneath the surface—why do certain memes go viral, while other well-crafted campaigns languish in obscurity? Often, it is the alignment with basic social and emotional drivers that propels a message to mass visibility.
Beyond virality, social media fosters a sense of community among consumers who identify with certain brands or lifestyles. These “brand communities” can become powerful advocacy networks, championing products or services based on genuine enthusiasm rather than purely transactional motives. Yet, this enthusiasm can be fragile. Instances of perceived deception, unethical data usage, or tone-deaf messaging can quickly erode trust and lead to public backlash.
Recognizing the magnitude of influence wielded by social media, marketers strive to refine strategies that resonate on both a rational and emotional level. The following sections unpack the core psychological drivers that fuel these strategies, clarifying why certain approaches succeed and how brands can remain mindful of ethical considerations while harnessing them.
Core Psychological Drivers
Cognitive and emotional processes guide how people perceive, interpret, and respond to marketing messages. Though these processes are universal, social media environments amplify their effects. By understanding these drivers, brands can craft campaigns that align with human tendencies, rather than working against them.
Curiosity and Novelty
Human beings are wired to seek new experiences and information. On social media, the endless scroll of fresh content feeds this desire for novelty. Marketers can harness curiosity by introducing intriguing headlines, preview snippets, or “teaser” visuals that pique interest. Whether it is the promise of behind-the-scenes revelations or limited-edition releases, triggering curiosity can lead to higher engagement and eventually a conversion.
Personalization and Self-Relevance
Personalization taps into the innate desire to feel special and understood. Custom product recommendations, dynamic ads, and relevant content curated by data analytics can create the impression of a one-on-one dialogue between brand and consumer. When users see content specifically aligned with their interests or past behaviors, they are more likely to engage and trust the source. Overuse or inaccurate personalization, however, can feel invasive, highlighting the delicate balance between relevance and intrusion.
Emotional Resonance and Storytelling
Stories activate parts of the brain associated with emotion, empathy, and even motor responses. This is why an emotional story—be it of triumph, struggle, or hope—can resonate more deeply than a straightforward sales pitch. On social media, successful campaigns often revolve around narratives that connect with shared values or aspirations. For instance, a brand championing environmental sustainability can evoke pride, urgency, or compassion, compelling consumers to support the cause by purchasing or endorsing the product.
Loss Aversion and Scarcity
People tend to fear losses more than they value gains. This bias manifests in marketing as the power of “limited-time offers” or “exclusive deals.” When individuals believe they might miss out on a unique opportunity or a finite product, they are spurred to act faster. Platforms like Instagram often amplify this scarcity principle through time-sensitive stories or countdown stickers, creating a real sense of urgency in the consumer’s mind.
Social Norms and Peer Influence
Humans are inherently social creatures, heavily influenced by perceived norms and the opinions of others. The digital equivalent of “keeping up with the Joneses” can be seen when users see their peers endorsing or using certain products and feel an urge to conform. Algorithms that show user likes, shares, or comments reinforce this dynamic. The fear of social exclusion or disapproval can play as much a role in decision-making as genuine product interest.
Habit Formation and Continuous Usage
Social media platforms often build features that encourage recurring interactions, from daily streaks to push notifications. This continuous engagement can create a habit loop—trigger, routine, reward—where the user returns to the app multiple times a day. Marketers who align their strategies with these habit loops have repeated opportunities to communicate with consumers. However, the challenge is to maintain authenticity and relevance; oversaturation or spam-like behavior can erode trust and lead to unfollows or ad fatigue.
Authority and Expert Endorsement
People are more likely to trust a source they perceive as an authority, whether it is a well-known brand, a recognized expert, or a celebrity. On social media, authority can be demonstrated by follower count, verified badges, or the display of professional credentials. Collaborations between brands and respected figures can lend credibility to a campaign, but authenticity remains paramount. A mismatch between the authority figure’s reputation and the brand’s values can evoke skepticism rather than trust.
Social Proof and Influencer Marketing
Social proof is a cornerstone of consumer psychology: when individuals observe others engaging in a particular behavior, they are likelier to follow suit. On social media, platforms that publicly display likes, comments, and shares provide instant social proof. Positive reviews, user-generated content, and testimonials serve as additional layers of validation that can significantly impact purchasing decisions.
User-Generated Content and Community Involvement
Inviting consumers to share their experiences or results—through photos, reviews, or testimonials—can create powerful endorsements that resonate with potential buyers. For instance, a fitness brand might encourage users to post workout selfies or transformation stories, fostering a sense of camaraderie and authenticity that is hard to replicate with traditional ads. This collective storytelling also feeds into the psychological need to belong, making the brand feel more like a community than a corporate entity.
Influencer Collaborations and Authentic Engagement
Influencer marketing has grown into a multi-billion-dollar industry, thanks to the potent mix of trust, relatability, and aspirational appeal that influencers can offer. When followers see an influencer they admire using or recommending a product, they perceive it as social proof. The best partnerships are those in which the influencer’s personal brand aligns closely with the product or service. A mismatch—such as a vegan influencer promoting a leather goods brand—risks backlash and undermines consumer trust.
Micro vs. Macro Influencers
The distinction between micro-influencers (smaller audience, often niche topics) and macro-influencers (very large following, mainstream appeal) hinges on reach versus intimacy. Micro-influencers tend to have high engagement rates and a close relationship with their audience, which can yield more authentic conversations and stronger influence on purchasing decisions. Macro-influencers or celebrities, on the other hand, might offer massive visibility but risk coming across as less personal. Marketers must weigh these trade-offs in designing their influencer strategies.
The Ethical Dimension
While social proof and influencer marketing are potent, marketers must navigate ethical considerations. Disclosures and transparency are key. Audiences are increasingly savvy about sponsored posts and can become cynical if they sense hidden agendas. Clear labeling of promotions and open acknowledgment of partnerships help preserve trust. Overly aggressive social proof techniques—such as faking likes or reviews—can lead to damaging public relations incidents, legal penalties, and long-term harm to a brand’s reputation.
Strategies for Ethical and Effective Marketing
Creating campaigns that respect consumer autonomy and well-being is not just a moral imperative; it also supports long-term brand loyalty. Tactics perceived as manipulative or exploitative might provide short-term gains but can degrade trust over time. By focusing on authenticity, transparency, and value-driven engagement, brands can build lasting relationships in a crowded digital marketplace.
Aligning with Core Values
Brands that articulate clear mission statements and corporate social responsibility initiatives often resonate more deeply with consumers who share those values. Whether it is sustainability, diversity and inclusion, or community building, integrating such values into content helps forge emotional connections. A campaign that genuinely aligns with these commitments will ring true, while one that merely pays lip service to popular causes may be dismissed as performative.
Storytelling with Purpose
Emotional narratives work best when they serve a genuine purpose rather than simply pulling at heartstrings to drive sales. Highlighting real customer stories or showcasing behind-the-scenes product development processes can offer transparency and forge trust. Audiences increasingly appreciate the chance to see the “human side” of a brand. This authenticity can be a powerful differentiator in a sea of polished but impersonal ads.
Interactive and Gamified Experiences
Some brands introduce polls, quizzes, or mini-challenges that invite active user participation. This approach can harness intrinsic motivators like curiosity, mastery, or competition. Gamified elements inject fun into the consumer journey, transforming what might otherwise be a passive advertising experience into something memorable. Careful design ensures that these elements enhance user engagement without resorting to manipulative tactics.
Building Communities and Fostering Dialogue
Instead of one-way broadcasting of promotional material, savvy brands host events like live streams or Q&A sessions, encouraging real-time interaction. This type of reciprocal communication fosters loyalty by making consumers feel heard and valued. It also generates user-generated content that can serve as social proof. However, brands must be prepared for transparent conversations, including constructive criticism, and handle such feedback with openness and respect.
Data-Driven Personalization with Consent
Data analytics allow for finely tuned personalization, but marketers must secure informed consent and protect user data diligently. Being transparent about data collection practices and offering clear opt-out mechanisms is vital in safeguarding consumer trust. Personalized ads that respect boundaries and stay relevant to user interests can lead to more positive brand associations than generic, scattershot campaigns.
Customer Support and Post-Purchase Engagement
The marketing journey does not end once a consumer makes a purchase. Follow-up messages, customer support interactions, or community spaces dedicated to product usage tips can all reinforce a positive experience. Responsive customer service channels on social media, such as dedicated Twitter accounts or Facebook Messenger bots, enable quick problem resolution and demonstrate a brand’s commitment to its audience.
Evaluating Performance and Iterating Responsibly
Metrics like click-through rates, conversion rates, and return on ad spend offer valuable insights, but they do not always tell the full story. Monitoring sentiment, brand mentions, and customer feedback can reveal whether campaigns resonate positively or provoke a negative reaction. Regularly iterating on strategies based on both quantitative and qualitative data helps maintain a dynamic yet consumer-friendly approach.
Conclusion
Social media’s role in digital marketing transcends mere advertising channels, weaving itself into the very fabric of consumer identity, community, and decision-making. By tapping into core psychological principles—such as social proof, scarcity, and emotional resonance—brands can more effectively capture attention, foster trust, and drive purchasing behaviors. The digital realm’s interactive nature presents both unprecedented opportunities and ethical obligations. As technology continues to evolve, marketers must remain vigilant about respecting user autonomy and building genuine relationships rather than relying solely on short-term manipulations.
In this environment, authenticity emerges as the ultimate differentiator. Campaigns that balance persuasion with respect, storytelling with transparency, and data-driven insights with privacy considerations are likely to stand out in a saturated market. Understanding the psychological dimension of consumer behavior equips businesses with a powerful toolkit for connecting with audiences on a deeper level. Yet, with great power comes great responsibility: those who deploy these strategies ethically will shape a future of digital marketing that is not only effective but also beneficial for brands and consumers alike.